关键词: 天竹纤维;染色棉纤维;色纺纱;因素;分析;措施
天竹纤维是中国继大豆蛋白纤维之后又一种我国独立研制开发并投入生产的一种再生纤维素纤维,其主要原料是生长在山区的竹子,经过人工催化处理,将甲种纤维素含量在35%左右的竹纤维提纯到93%以上,采用水解一碱法机多段漂白精制而成,它不仅集天然纤维与人造纤维的优点于一身,而且还具有天然抗菌性能,同时具有良好的生态环保性,是一种再生环保型纤维。染色棉由本色棉经过染色加工而成,用天竹纤维与染色棉根据不同的混纺比例纺制成色纺纱,用其加工的织物,布面风格独特,是不可多得的一种新型面料。目前色纺纱主要作为针织用纱,针织用纱对纱的质量要求比机织用纱高,因此,提高色纺纱质量就显得十分重要。本文结合色纺纱的生产实践,对影响其质量的因素进行了试验和分析,在提高色纺纱质量上作了探索。
1 原料性能与选配
天竹纤维:选用河北省吉藁化纤厂生产的天竹纤维,细度l.65dtex,长度38 mm,干强4.4l cN/dex,湿强3.9cN/dtex,干伸长19.8%,含油率0.35%,质量比电阻lg Pm为8.8,超长纤维率和倍长纤维率为0。
染色棉纤维:本色棉经过染色加工后,长度变短,均匀度变差,短绒率升高,单纤强力变低,此外,还存在弹性变差,天然卷曲和抱合力变差,包间与批间色差大,且有杂色现象。为提高色纱质量,应选择较好的原棉进行染色。
各染色棉性能见表1。
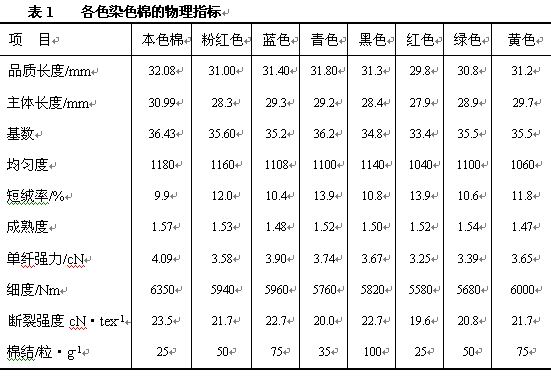

3.1 纺纱前预处理及混和方法
在天竹纤维上喷洒0.75%抗静电剂,以减少静电,保证后道工序顺利进行。要严格控制染色棉的回潮率,因为回潮率会影响色棉的色相,过高的回潮率会增加清梳工序的开松除杂难度。由于清棉混棉不易控制混纺比,所以色棉与天竹纤维采用并条混和。
3.2 各主要工序工艺参数
3.2.1 清棉工序
天竹纤维长度长,整齐度好,含杂较小,较蓬松,但抱合力差,容易开松,故打击速度不能太高,并适当缩小尘棒间隔距,适当增加打手与尘棒间隔距,避免损伤纤维和增加短绒。天竹纤维横截面呈中空,回潮率与粘胶接近,为避免粘卷,采用加粗纱方法和采用凹凸罗拉。温湿度是影响天竹纤维卷内在质量的一个关键因素,囚此清棉车间温度选择27℃~33℃,相对湿度50%~55%。其工艺参数为:卷子定量:385 g/m~395g/m,A036C型机打手速度425r/min,成卷机打手速度865r/min,棉卷罗拉速度11.5 r/min,A036C型机打手与给棉罗拉隔距11 mm,梳针打手速度495 r/min,打手与剥棉罗拉隔距2.5 mm,A092型机角钉帘速度50 m/min,卷子重量不匀率1.20A,以下,伸长率1.35%以下。
染色棉以开清混和为主,多松少打、多混少落、多包抓取、多包混和、打梳结合、早落少碎。为防止过分损伤纤维而增加短绒,要求在开清棉的第一阶段以扯松和自由打松为主,第二阶段以握持打松为主。各部件打手速度降低19%左右,流程不经过A036B型机,以减少一个打击点。A076C型成卷机的综合打手采用梳针式,减少棉块(束)的反复滚动,防止纤维纠缠成团。排包时要与其他纤维隔开,防止异性纤维混入。A002D型抓棉机要少抓、勤抓、少打击,以提高混和均匀性,A006B型机打手速度420 r/min,A036C型机打手速度485 r/min,A092型机打手速度420 r/min,A076型机综合打手速度800 r/min,这样能充分发挥棉箱均匀混和的作用。主要工艺参数为:卷子定量380g/m~395 g/m,伸长率1.4%以下,重量不匀率1.25%以内。
3.2.2 梳棉工序
天竹纤维整齐度好,抱合力小,梳棉采用“轻定量、低速度、中隔距、小张力”的工艺原则。为了更好地梳理和除杂,针布要保持四锋一准,以提高棉网清晰度和减少成纱棉结。采用中隔距能减少纤维损伤,而且还有利于分梳,增加纤维维在锡林盖板问的分梳和转移,减少纤维在两针面间的漂浮和搓揉,从而减少棉结和纱疵。采用较小的棉网张力,减少棉网落网现象。适当降低各部梳理速度,刺辊速度适当降低,而锡林刺辊问速比适当提高,以保证纤维顺利转移。梳棉工艺参数为:生条定量18.0 g/5 m~18.6 g/5 m,刺辊速度815 r/mir,锡林速度330 r/min,道夫速度21.5 r/min,盖板速度84 mm/min,锡林~盖板隔距0.25 mm,0.23 mm,0.20 mm,0.20 mm,0.23 mm,锡林~道夫隔距0.13 mm。
染色棉强力低,为避免损伤纤维,应适当降低各部速度。因染色棉的成熟度低,生条定量应偏轻控制,可减轻针面负荷,改善梳理效果,对棉束进行细致松解,并减少纤维问搓揉,防止棉结增加,除尘刀采用小角度,以增加排杂的效果。采用瑞上格拉夫针布,加强纤维的分梳,以提高纤维的分离度。工艺参数为:定量20 g/5m~2l.32 g/5 m,锡林速度305r/min,刺辊速度800 r/min,盖板速度1 98 mm/min~248 mm/min,锡林~刺辊隔距0.16 mm,给棉板~刺辊隔距0.16 mm,锡林~道夫隔距0.10 mm,道夫速度18.5 r/min~19.5 r/min,锡林~盖板隔距为0.23 mm,0.20 mm,0.18mm.0.18 mm.0.20 mm。
3.2.3精梳工序
因染色棉均匀度差、短绒率高、成熟度差、单纤强力差异大、棉结多,并且生条中含有大量的短绒和杂质,纤维的伸直平行度较差,所以必须进行精梳加工,以排除短绒,减少棉结杂质,提高纤维整齐度、伸直平行度和分离度,降低条干不匀率,以提高成纱质量。采用整体锡林和定量偏轻的小卷,同时要保持锡林和顶梳针齿锋利,增大落棉隔距,减少染色棉纤维的反复梳搓,减少棉结数量,精梳落棉率控制在18%~22%之间。
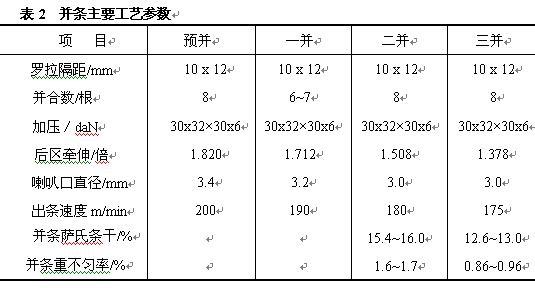
粗纱工序采用“低速度、大捻度、大卷绕密度、小集合器和钳口隔距”的工艺原则。发挥主牵伸区的主导作用,有利于控制浮游纤维,因为纤维间抱合力小,粗纱在细纱机上易产生意外伸长,所以粗纱成形不宜过大。适当降低锭速,稳定粗纱张力,能提高纤维的伸直平行度,减少意外牵伸和粗纱毛羽,提高粗纱条干水平。根据染色棉性能和天竹纤维的特点,将后区隔距适当缩小,可保证纤维在后区充分伸直。适当增大粗纱捻度、卷绕密度,对改善粗纱质量和提高细纱综合质量极为重要。其优化工艺参数为:粗纱定量4.2g/10m~4.6g/10m,后区牵伸倍数1.25倍~1.32倍,捻系数80~88,锭速500 r/min~550 r/min,前罗拉速度142 r/min~160 r/min,轴向卷绕密度为3.327圈/cm~3.375圈/cm,罗拉隔距22 mm~28mm,加压26 daN/双锭×15 daN/双锭×18 daN/双锭,钳口隔距3.0mm-4.0 mm,中区集合器(6 mmX4 mm)~(8 mmx6 mm),前区集合器8 mm~10 mm,萨氏条干不匀率15.8%以下,粗纱重量不匀率在0.7%以下。
细纱工序采用弹簧摇架加压、软弹不处理胶辊、内外花纹胶圈、气圈控制环、国产上销、小孔径镀瓷导纱钩和渗硫钢领钢丝圈,后区牵伸倍数偏小掌握,集中前区牵伸,以加强纤维在牵伸过程中的有效控制。采用新型锭带,及时检查锭带张力和锭速,尽量减小锭速差异,降低捻度不匀率,以提高单纱强力和降低单强CV值。细纱捻度偏大掌握,以保持须条问的紧密度,增加纤维间的抱合力,提高成纱质量。细纱工艺参数:捻系数350~375,锭速12 500 r/min~13 500 r/min,钳口隔距2.5 mm~3.0 mm,罗拉隔距18.5mm~29 mm,前罗拉速度160 r/min~165 r/min,平均成纱条干CV值为14.8%,百米重量偏差平均值为+0.2%~+0.3%,,重量不匀率在0.8%以下。
4 成纱质量(见表3)
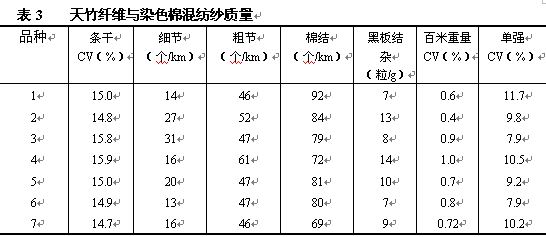
2、竹/CJ(青)89/11 14.5 tex
3、竹/CJ(黑)92/08 11.5 tex
4、竹/CJ(黄)90/10 11.5 tex
5、竹/CJ(绿)95/05 14.5 tex
6、竹/CJ(紫)85/15 13 tex
7、竹 / CJ(绿)92/08 14.5 tex
5 结束语
染色棉纤维强力低,弹性差,棉结多,成熟度和长度差异大,减少棉结和短绒是提高色纺纱质量的基础。在色纺纱加工中,保证天竹纤维与染色棉纤维混和均匀,能明显提高色纺纱强力。要保证混纺比准确和色泽均匀,混色方法以条混为佳。因色纺纱生产的主要问题是色差问题,因此清棉工序要以开松混和为主,应多松少打、多混早落,尽量使色棉均匀混和,减少棉结和色点的产生几率。梳棉是影响成纱棉结杂质的关键工序,优化梳棉工艺能提高生条质量。并条采用一混二并法能保证色泽稳定和均匀,容易控制混纺比。天竹纤维与染色棉混纺针织纱,可根据需要灵活搭配,色泽调整方便,风格独特,用其加工的针织织物,色泽和谐牢同,织物表面自然活泼,且悬垂性佳,手感柔软,穿着凉爽舒适,光泽亮丽。此外,还具有较好的天然抗菌功效,特别是吸湿性及透气性居各类面料之首,是夏季服用和贴身内衣的首选面料。天竹纤维与染色棉纤维产品可开发的品种很多,市场前景十分看好。