棉结是成纱质量中极为重要的物理指标,也是影响布面质量的主要因素,因此控制成纱棉结是提高布面质量,满足用户要求的重要工作。棉结的控制是一项系统工程,不能单一地将棉结问题归属于哪一个工序,但应以清梳工序为主。下面就清梳工序的工艺流程、设备性能以及打击力度等方面对棉结的控制作一介绍。
1产生棉结的原因
(1)开清棉工序工艺流程长,打击点多,各打击部件速度快,打击力度大,造成纤维损伤形成短绒,在梳棉工序揉搓形成棉结。
(2)开清棉工序开松效果不良,增加梳棉机梳理负担,降低分梳效果。
(3)分梳除杂元件的锐度、光洁度不良,造成梳理度下降;开松分梳元件损伤造成绕花、缠花,最终使棉结增加。
(4)由于各机件圆整度、平直度差异,造成工艺隔距不能完全一致,影响分梳效果。
2成纱棉结的控制
2.1缩短开清棉工艺流程
在保证开松效果的前提下,尽量缩短开清棉工序的工艺流程。我厂开始纺CJ 9.7 tex品种时的开清棉工艺流程为:
A002型抓棉机×2→A035AS型混开棉机→A035型豪猪开棉机→FA022型多仓混棉机→FA106型豪猪开棉机→A092型双棉箱给棉机×2→A076型成卷机×2
经过一段时间的摸索以及大量的试验数据表明,这一工艺流程对纤维的损伤较大,破坏了纤维原有的特性,因此基于CJ 9.7 tex品种原棉成熟度好,含杂少,细度较好的性能,我们相应地缩短了开清棉工艺流程,改后的工艺流程为:
A002型抓棉机×2→A035As型混开棉机→FA022型多仓混棉机→FA106型豪猪开棉机→A092型双棉箱给棉机×2→A076型成卷机×2
关闭A035型豪猪开棉机,这样自由打击点由原A035AS型混开棉机的双打手、A035型豪猪开棉机两个自由打击点改为只保留了A035AS型混开棉机双打手这一个自由打击点,大大降低了纤维的损伤,尽可能保留了纤维原有的特性不变。
合理确定各部打击速度,减少打击力度是降低棉结的重要措施。在选择各部打手速度时应处理好短绒、棉结与除杂效率、棉卷含杂率几者之间的关系,找出一个最佳的结合点,既能够使开松、除杂达到最佳效果,满足梳理要求,又能使短绒、棉结的增长率控制在最低限度,从而杜绝片面追求除杂效率及棉卷含杂率而忽略了短绒及棉结的增长。我厂CJ 9.7 rex品种使用的原料是31mm-35 mm的长绒棉,原棉中含杂较少,根据上述几者之间的关系,以及实际使用的原棉情况,我们对开清棉工序各打手速度进行了优选。
(1)A002型抓棉机抓棉打手速度由840 r/min降为750 r/min。
(2)A035AS型混开棉机第一打手速度由700r/min降为692 r/min,第二打手速度由828 r/min降为771 r/min,A035型豪猪开棉机打手速度由1086 r/min降为0 r/min(关闭)。
(3)FA106型豪猪开棉机打手速度由514 r/min降为400 r/min。
(4)A076型单打手成卷机综合打手速度由912 r/min降为804 r/min,各部短绒均有所下降(见表1)。
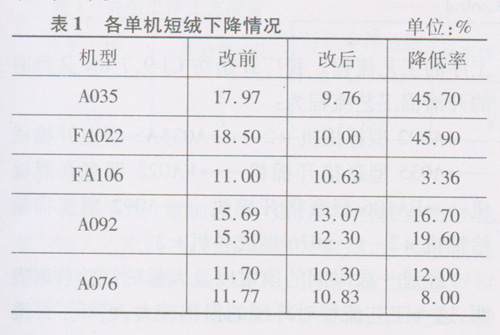
配棉的平均短绒率为10.8%,降速后棉卷短绒率为10.56%(人工检测16mm及以下),由此可计算出原棉至棉卷的短绒增长率为-2.22%,棉卷含杂率由原0.49%上升到0.57%增加0.08个百分点,但棉网棉杂粒数没有恶化,较好地处理了短绒率与棉卷含杂率之间的关系。
2.2优选分梳元件
从优化分梳元件为切入点,减少横向梳理差异,增强均匀混和作用,加强分梳作用,提高纤维均匀转移和有效转移。为此采用“矮、浅、尖、薄、密、小”的新型锡林针布,增加锡林针齿横向密度,减少梳理差异,提高梳理均匀度,道夫针布选择横向密度更大一些,针齿高一些的金属针布,防止纤维漏剥、揉搓形成棉结,采用较大密度的盖板针布来提高锡林与盖板之间的分梳作用。通过对分梳元件的优选达到棉网清晰度高、生条棉结杂质少、纤维分离度好、转移率高的目的。
2.3加强设备基础性管理工作
(1)严格控制针布包卷前滚筒裸磨工作,必须保证滚筒裸磨后平直度和圆整度不大于0.02mm,斜磨时应注意斜磨宽度与斜磨量相互匹配..滚筒磨砺的有关参数见表2。
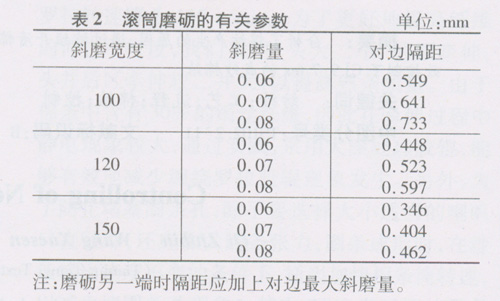
(2)严格控制针布包卷的速度,针布包卷速度应控制在8 r/min左右,以减少针布在包卷过程中的抖动和裂伤。
(3)确保盖板龙骨的平直度不大于0.05mm,盖板踵趾面根丝差异不大于0.02 mm,包卷后盖板五点平直度不大于0.07 mm,盖板的板丝差异小于0.1 mm。
(4)曲轨前后罩板和大小漏底表面光洁弧度应达标。
采取以上措施后,CJ 9.7 tex成纱棉结有了很大改善,成纱棉结由229粒/g下降至179粒/g,下降了21.8%。
3 结束语
棉结控制是一个系统工程,只有加强系统工艺研究,加强设备的基础性管理,加强试验分析,才能使棉结控制在一个较为稳定的水平。我们的体会是:(1)根据原棉特征合理制定开清棉工艺流程,做到分梳、除杂适度。(2)合理配置工艺参数,选配好各打手速度,做到短绒与结杂兼顾。(3)采用新型分梳元件,增加梳理度,增强分梳效果,提高棉网质量。(4)提高设备运转状态的稳定性,消灭台差、锭差,保证质量的稳定。