2探索研究、实践清梳联工艺,解决当前生条棉结、短绒问题
清梳联在开清棉部分实现了短流程及高产梳棉后主要靠高速化、锯齿化。在开清棉中纤维受到较高打击强度、梳理化开棉及高产量梳棉机较高梳理场强度的梳理。另一方面喂人高产梳棉机的筵棉结构与棉卷结构不同,使纤维遭到损伤,棉结、索丝增多。特别是在梳棉机棉结、短绒与梳理单根化、除杂这一对矛盾非常突出,不论引进各国清梳联设备还是国产清梳联都遇到这个问题,使短绒、棉结增加以至影响成纱条干、粗节、棉结。近几年来,我国广大清梳联科技工作者研究探索清梳联工艺,在解决棉结、短绒方面取得了较好的效果。
2.1探索研究的重点
清梳联在解决短绒、棉结方面重点研究原料物理性能及针布优选与配套和清梳联工艺相结合。要根据不同原料的物理性能与纱线最终产品质量要求,采用不同的工艺处理原则,使其达到最终产品的质量要求,不能以万能工艺来处理不同的原料,也不能将传统棉卷梳棉工艺用于清梳联。
棉纱的质量基础,在于清梳联半制品结构与生条质量水平,它与成纱质量是正相关的,研究纺纱工艺过程中对纤维损伤、减少棉结、减少短绒含量,力争保持纤维主体长度不受损伤,应是棉纺工艺研究的核心,是清梳联工艺研究中的重中之重。这是因为短绒是造成飞花、纱疵、毛羽的主要因素,短绒会增加棉结,使精梳落棉率增加,影响成纱的制成率与成本,短绒是并、粗、细牵伸工艺控制的重点,它影响成纱的条干、粗节、细节、棉结、毛羽、单强、单强CV以及细纱断头率与细纱生产的正常运行。
解决短绒、棉结问题,必须从源头抓起,有原料的物理性能、开清棉工艺中打击强度(打手形式、速度隔距、喂人量)及“输送转移”气流的控制。而梳棉工艺中,针布的优选与配套是首先要解决的问题。不同的针布规格(尤其是锡林、盖板、道夫与刺辊)、不同的梳棉产量与筵棉结构、纤维的物理性能,应采用不同的梳理场强度,要做到结杂、短绒兼顾才能取得较好的效果。所谓梳理场强度应当包括速度、隔距、针布规格、喂入量、单产等。
2.2实践经验总结
(1)开清棉流程越长,除杂效率越高,但棉结增长率越高,索丝多。
(2)开清棉打击强度越大开松效果越好,除杂效率高,大杂变小杂的几率越高,纤维损伤大、短绒多、索丝多、棉结增长率高。因此,要十分重视“损伤”,尤其“伤”的问题,它是潜在的短绒与棉结。检测纤维损伤东华大学贺福敏教授介绍用“聚合度”法,聚合度降低10%就表示纤维已受损伤。
(3)开清棉除杂效率与梳棉除杂效率有互补性。
(4)开清棉棉结增长率高、梳棉短绒含量也高。
(5)开清棉能排除短绒也能增加短绒,应尽最大努力做到排除大于增加,即与原棉比为负增长。
(6)金属针布的选用与合理配套,保持针布的锐度、平整度,对解决生条棉结起着重要甚至说是决定性的作用。
(7)在不同筵棉结构与纤维性能、梳棉台时产量及梳棉机针布配置下,应采用不同的梳棉工艺。因此,研究清梳联工艺及后续工艺是纺纱永恒的课题,是纺纱厂的重要日常工作。纺机制造应考虑调整工艺的及时性与方便性,如:速度宜全部采用调速电机;可在外部随机调整尘棒与除尘刀隔距与角度;可模块组合梳棉机前后固定分梳板的整体调换;可随机自动调校盖板与锡林隔距等。
(8)梳棉机产生短绒也排除短绒,产生大于排除。目前清梳联生产短绒比筵棉增长能做到不大于5%左右尚有一定空间。
(9)梳棉梳理过程中产生棉结也排出与分梳开棉结,梳棉棉结去除率可以作到85%以上(对筵棉)。
2.3清梳联基本工艺原则
2003年中国纺织工程学会棉纺织专业委员会在苏州召开的“清梳联、精梳机工艺研讨会”上,将清梳联基本工艺原则归纳为:轻抓、抓小、抓匀、抓全;连续均匀喂给;薄喂柔和开松;气流参数保证;针布合理配套;梳理转移适度;结杂、短绒兼顾。
抓棉机的轻抓、抓小、抓匀、抓全成分是柔和开松、混好、清除、缓和梳理及纤维少损伤、棉结少的基础,直接影响后续工序精、并、粗以及成纱质量,因而,要高度重视纺纱首台机“四抓”的工艺效果。
要发挥往复抓棉机“四抓”的应有效能,必须优选适应不同品种、原料、产量的抓辊、小车往复速度、下降量及刀片尖与压棉肋条工作面的间距等工艺参数。同时纺机厂要严格控制加工精度与装配精度,确保抓棉辊动平衡.刀尖在径向与轴向公差(即刀尖在圆柱面上的差异)及压棉肋条底面在同一面公差等,这是“四抓”的前提,否则最好的工艺也难达到应有的效果。
对于抓棉机的抓轻、抓小、抓匀、抓全“四抓”的理解:
(1)抓轻:就是不希望打手速度太高,太高了刀片对纤维材料的瞬间冲击力较大,易使纤维受损。厦门华纶纺织有限公司的1.7 m机幅抓棉机打手速度由1650 r/min减到1350 r/min,短绒减少1.5%;加宽打手工作长度为2.3 m后,石家庄三棉纺织有限公司将打手速度降至1000 r/min也取得较好的效果。笔者感到尚有降速的空间,打手速度越高,在气流附面层影响下,转移不良易产生索丝、棉结。因此,在满足清梳联总产量的要求下,要轻抓使棉束减小。
(2)抓小:是保证气流除杂或轴流除杂的基础,只有小而松的棉束,杂质才暴露在纤维的表面,大杂才能在上述机台内除掉,减轻后续机台开松除杂负担,防止大杂变小而多,同时也是开清短流程的基础。目前抓取棉束在30 mg-40 mg,相当于A系列清棉机组进入92棉箱的棉束重量水平。
(3)抓匀:是保证后续开松、除杂、混和的基础,要使筵棉结构良好均匀就要求棉束离散程度小。为此需优选抓辊速度、刀尖与肋条底面的间距准确,纺机厂要精确抓棉辊动平衡,刀尖径轴向公差,肋条底平面与肋条精度。如不严控,工艺上车成为空谈,很难抓匀。如要精确到打手下降量0.1 mm的效果,那么上述的公差必须严格控制。
(4)抓全:在最短时间内抓全配棉成分,有利均匀混和。混和均匀这个问题,清梳联的开清棉比传统棉卷梳棉工艺要差一些,需引起注意,多仓混和效率本身有一定限度,但抓棉辊瞬间抓匀、抓小对混和有一定效果,瞬时抓取棉包数越多,混和效果越好。抓棉机排包合理也是抓全的要素,如小单元全成分排包,尽可能使抓棉在最短时间抓全一个成分。
2.4开清棉与梳棉除杂合理分工及开清棉工艺
清梳联除杂应从整个系统考虑,尽可能做到在开清棉除掉的不留给梳棉,应在梳棉除掉的不要求开清棉来承担。清梳联开清棉实现短流程后有三个开清点,即开棉、清棉和梳棉。提出清梳合理分工问题,实质上是这三者间的分工问题。
从杂质的形态来看应分为大杂(棉籽、籽棉、大的不孕籽等)、中杂和小杂,按USTER公司分为投影直径大于500μm的称之为粒杂,投影直径小于500μm的是尘杂。笔者个人看法:粒杂应视为中杂,尘杂应视为小杂。梳棉机应除去的是尘杂。目前因测试手段难于量化,对三者之间很难界定。
大杂硬杂在开清棉的重物除杂装置、轴流开棉机中应尽最大可能除去,做到早落少碎,这是清梳联中开清棉与梳棉分工除杂的关键,也是在后续工艺中做到“薄喂柔和开松”,减少纤维损伤与棉结、短绒增加的基础。
要实现“大杂早落少碎”就必须使往复抓棉机轻抓、抓小、抓匀、抓全,在多仓混棉机棉仓密度稳定的情况下,抓棉机效率在95%以上,实现微小棉束向重力除杂装置、轴流开棉机喂人。研究重力除杂装置气流与除杂板工艺,优化轴流开棉机的工艺,选好打击强度,设计好气流参数(人口、出口、排尘口、排杂口四点),最大限度的除去大杂。目前很难量化除大杂的情况,一般以观察主除杂机齿条辊筒表面嵌籽棉、棉籽情况的多少来审定,同时也要看梳棉机盖板针布卡破籽壳情况,做的好的应没有卡破籽情况。
一般情况轴流开棉机打手速度在500 r/min-700 r/min,尽可能选用较低速度。主除杂机的工艺应视轴流开棉机的除杂效果及喂人品结构来考虑打击强度,尽最大可能降低打击强度,注意纤维的“损伤”、索丝和棉结。如青纺机FA116型主除杂机与原德国赫格特公司MAC型机结构相同,MAC型机原设计锯齿辊筒打手速度2200 r/min,除杂效率很高,达到50%以上,但出现大量索丝、棉结,短绒也猛增。德州棉纺厂生产CJ 14.5 tex纱,将FA116型锯齿辊筒速度设计在320 r/min取得了较好的效果。目前使用FA116型主除杂机,各厂速度一般在500 r/min~700 r/min,根据具体情况来考虑(试验后再确定)。
除杂效率过去是开清棉一个主要指标,传统概念一般原棉含杂在2%以上时,开清棉除杂效率60%以上。除杂效率高打击强度必须大,打手速度高打击冲量大,开松度好,棉束小。除杂效率高,杂质破碎,大杂变小杂的可能性大,同时纤维脱离打手向外转移差,索丝多,棉结、短绒增加。这是开清棉的主要矛盾,要克服单纯追求开清棉除杂效率,提高打击强度的倾向,要“开松、除杂、棉结、短绒”兼顾。开清棉除杂效率不一定要达到60%,筵棉含杂率在0.8%~1%就可以。
实践证明开清棉除杂与梳棉除杂有互补性,即开清高梳棉低,反之亦然。如,同一配棉试验的除杂效率:一种工艺,开清棉68%、梳棉28.8%,总96.8%;另一工艺,开清棉32.1%、梳棉63.9%,总95.6%,而生条棉结杂质与短绒后者均优于前者。故清梳联除杂以清梳结合考核为宜,一般情况下清梳联总除杂效率在96.5%~98.5%。
开清棉棉结增长率在50%~100%,最好在80%以下,棉结增长越多梳棉短绒增加越多,同时也说明纤维在开清棉打击过度,转移差,扭搓情况严重。有资料报道:安徽华茂纺织有限公司用清梳联纺CJ 14.5 tex纱,在开清棉棉结增长率不到35%。开清棉既排短绒又产生短绒,一般应做到筵棉短绒含量与原棉短绒含量不增不减(传统测试方法),最好做到排出大于产生,负增长,这样就可能保持纤维的主体长度不受损伤,又可使大杂粒杂在开清棉中除去不留给梳棉。
2.5 高产梳棉机工艺及生产质量有关问题
开清棉喂入高产梳棉机的筵棉结构与传统棉卷结构有本质区别,在开清棉机组,最后一只打手多采用锯齿辊筒,有的还不止一个,因此棉束质量在10 mg以下。青岛纺织厂生产的FA116型机出口棉束质量在2 mg左右,筵棉开松度好,棉层蓬松、棉束排列结构与方向性不如棉卷结构。在高产梳棉机产量为40 kg/h~50 kg/h,高产梳棉机关键问题一个是针布的优选及合理配套,另一个是高速梳理与工艺配置。
而优选针布配置是高产梳棉机的基础,对梳理质量极为重要。梳理元件(针布)的种类贯穿全机的各个方面,锡林、道夫、盖板、前后固定分梳板、刺辊、刺辊下分梳板,它们与纤维直接接触,进行握持、分梳与自由梳理及剥取转移。因此,高产梳棉机针布优选及合理配套,梳理强度有关参数的设定与筵棉结构、纤维的物理性能相适应,是提高梳棉机生条质量与成纱质量的关键。
2.5.1 针布优选及合理配套
优选针布是以锡林针布为核心,优选出适应于高产优质梳棉机的针布规格及型号,再考虑其他针布的配套。为了改善针布握持分梳的能力,减少梳针分梳时纤维滑脱趋势的增加,在主分梳区内尽量减少浮游纤维,锡林针齿的工作角必须随速度的提高而减小。
(1)在锡林、盖板分梳区中,无论是盖板梳理还是锡林梳理,必须有一方握持纤维,而握持方必须保证纤维不下沉,使其保持在针齿的工作面上,这就必须加大针齿的前角。梳棉机高产后,针齿纤维负荷增加,应设法减轻针布负荷加强梳理度,因而锡林针布针齿总高度随产量的增加而减矮,齿密加密,形成:矮、浅、尖、薄、密、小的特点。
工作角由65°减小至60°,总齿高由2.5/mm减至2 mm,齿深由0.6 mm减至0.4 mm,在梳理过程中使纤维处在针尖,增加与另一个针面(盖板、道夫)的接触长度和作用齿数,有利于分梳、交替和转移,提高梳理效果减少棉结。经实践2030×01550型锡林针布与原2525×01550型锡林针布相比可大幅度减少棉结(其余条件相同)。对比结果见表2。
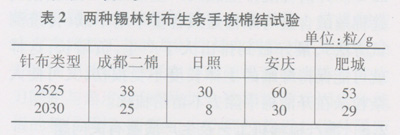
(2)盖板针布肩负着分梳、除杂、混和、均匀的多项任务,齿间必然有纤维充塞,严重的会影响分梳,因此盖板植针密度有一定限度,一般在锡林针布齿密的60%左右,在植针方面采用稀密或渐增排列。每根盖板针布入口(趾部)稀、出口(踵部)密,使喂人纤维受到缓和梳理,同时适当减小纵向密度使之横向加密,横向最小针距约0.5mm,采用曲线布针点轨迹纵向递增,与密集区连续自然,使纤维在受脉冲梳理过程中有利于纤维的伸长,易于排除杂质,降低棉结,多排短绒。盖板踵趾差由0.96 mm减到0.56 mm,实际上减小了锡林盖板之间的平均梳理隔距,有利于梳理作用的发挥。GRAF公司SPACETOP型、无锡纺器JPT型及无锡分梳元件厂的MCH型等,基本上属于上述规格。
(3)道夫针布的作用既有与锡林的梳理,但更主要的是抓取、凝聚作用,能将锡林梳好的单纤维及时转移出来,道夫针齿应具有足够的抓取握持能力,采用深而细的齿型。因此道夫针布的工作角在60度,且有进一步减小的趋势,加大道夫齿高齿深增加齿问容量,有利于纤维向道夫转移和凝聚,并能顺利引导高速气流。但齿深加大后针齿易轧伤。在针齿设计上以鹰嘴的居多,也有的在针齿两侧轧出横纹以增加抓取凝聚能力,齿高近年来有增高的趋势。齿密300齿/(25.4mm)2~970齿/(25.4 mm)2,一般在锡林齿密的2/5~3/5。采用这种齿条与锡林匹配提高了转移率,改善了棉网质量,特别是棉结明显减少。
(4)刺辊,纺纯棉时齿条工作角度增至80度~85度、纺涤棉化纤时90度,便于分梳转移,纵向齿距随角度加大而减小,大多4.5齿/(25.4mm)2~6齿/(25.4 mm)2,采用上述齿条的有槽刺辊,可适当降速,以减少对纤维的损伤和有效分梳抓取纤维束及其转移。自锁齿条则采用横向加密,齿高由5.9 mm降至5.0 mm,有继续向矮发展的趋势。有的文章指出高产梳棉机前后车肚大量减少,采用矮齿大工作角齿条后,落棉率、除杂效率、排除短绒的能力有可能提高外,还因齿密变化可适当降低梳棉机唯一握持打击的刺辊速度,对纤维转移、减少棉结与纤维损伤、减少短绒有利。刺辊齿条规格对生条质量与成纱质量有显著的影响,选用高度低、前角较小的齿条在同样条件下,除杂效率高,纤维损伤小而对进人工作区内分梳质量有利。高度低、前角小向锡林转移顺利,减少返花、减少棉结。
目前刺辊齿条规格型号较少,在针布配套工作上,只重视锡林、盖板、道夫的配套对刺辊有所忽视,建议针布厂应生产不同规格的齿条供棉纺厂选用,以其优化组合配套,而且刺辊针布制造质量差异较大,远不如锡林、道夫的重视程度。
(5)固定分梳板:刺辊下分梳板,对刺辊所握持纤维的另一端进行托持梳理,要求在梳理过程中释放能力强,自洁能力强,不塞花、不挂花,在刺辊分梳后尚有少量纤维束未被松解。在后罩板处加装固定分梳板,使纤维进人锡林~盖板工作区之前,进行一次预梳,使进入锡林~盖板工作区内的纤维束变小,纤维排列方向得以改善。纤维束变小而松散可以缓解脉冲梳理力的增加,减小在锡林~盖板工作区内分梳负荷与分梳过程中纤维损伤。前后固定盖板各三根,后固定盖板齿密60齿/(25.4 mm)2~182齿/(25.4 mm)2,目前一般应用的是80齿/(25.4 mm)2~120齿/(25.4mm)2~160齿/(25.4 mm)2(从后到前)。前固定盖板因此处锡林分梳区的纤维单根化较好,齿面纤维负荷小,梳理力不大,主要发挥补充梳理作用,应保持一定的齿密,一般在240齿/(25.4mm)2~800齿/(25.4 mm)2,纺细号纱采用400齿/(25.4 mm)2、纺中号纱应在350齿/(25.4mm)2以下。
在后固定盖板分梳过程中杂质有撕碎的可能,因而在固定盖板组合中加装除尘刀及吸风装置即棉网清洁器以便排除尘杂,加大棉网清洁器吸力及适当缩小尘刀与锡林的距离,对排除小杂、短绒有利。
各固定盖板的齿条针布应具有自洁能力,既不充塞杂质和纤维、短绒,又应保持针面的清洁,还应具有握持分梳纤维的能力。
各种针布应保持较好的锐度与光洁平整,并应根据产量与质量情况确定更换标准和周期,对梳理质量差的分梳元件应及时更换。
七种元件配套应考虑:
(1)加工纤维的性质,纤维长度、成熟度、单纤维强力、摩擦性能;
(2)梳棉机产量,生条定量,喂人筵棉结构,锡林速度范围;
(3)纺纱质量要求;
(4)刺辊、锡林、道夫、盖板间各规格参数相互影响。
应逐渐加深梳理作用的顺序,齿密设计的选择应:刺辊<刺辊下分梳板<后固定盖板<回转盖板<前固定盖板<锡林。其中应以锡林为中心,目前各厂选择情况:产量在40 kg/台•h~50kg/台•h,生条定量在19.5 g/5 m~25g/5 m,在正常配棉条件下,锡林360 r/min~430 r/min,刺辊在600 r/min-800 r/min,清梳联高产梳棉机大多选用进口针布,锡林为2030×01550型,道夫为4030(B)01980型、02080型。