1. 试验结果与分析
1.1 原料性能与选配
天竹纤维:选用河北省吉藁化纤厂生产的竹纤维,细度1.65dtex,长度38mm,干强4.41cN/dtex湿强3.9cN/tex,干伸长19.8%,含油率0.35%,质量比电阻1g ρ m为8.8,超长纤维率和倍长纤维率为0%。
染色棉纤维:本色棉经过染色加工后,长度变短,均匀度变差,短绒率升高,单纤强力变化等特点,此外,还存在弹性变差,天然卷曲和抱合力变差,包间与批间色差大,且有杂色现象。为提高色纱质量,应选择较好的原棉进行染色。其性能见表1所示。
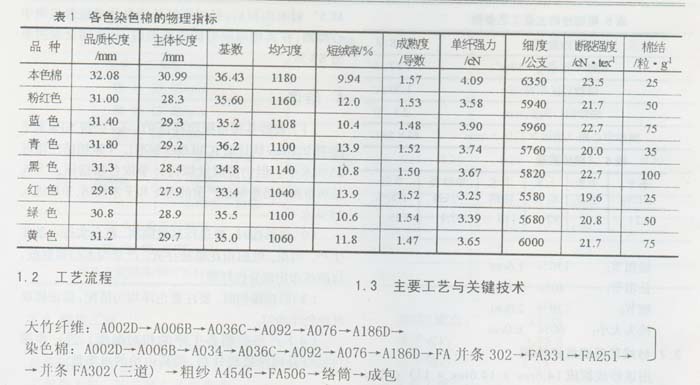
1.3.1纺纱前预处理预混合方法
在天竹纤维上喷洒0.75%抗静电剂,以减少静电,以便后道工序顺利进行。要严格控制染色棉的回潮率,因为同潮率大小会影响色棉的色相,过高的回潮率会增加清钢T序的开松除杂难度。因为清棉混棉不易控制混纺比,色棉与天竹纤维混合采用并条混合方法.
1.3.2各主要工序工艺参数
1.3.2.1清花工序
天竹纤维长度长,整齐度好,含杂较小,较蓬松,似抱合力差,容易开松,故打击速度不能太高,并适当缩小尘棒问隔距,适当增加打手与尘棒间隔距,避免伤纤维和增加短绒率,天竹纤维呈天然中空的横截面,回潮率与粘胶接近,为避免粘卷,应采用加入粗纱和采川凹凸罗拉,温湿度是影响天竹纤维卷子内在质量的一个关键因素,因此清花车间温度选择27℃~33℃,相对湿度50%~55%,其工艺参数为:卷子定量385g/m~395g/m,A036C打手速度425 r/min,成卷机打手速度865r/min,棉卷罗拉速度11.5r/min,A036C打手与给棉罗拉隔距11 mm,梳针打手速度495r/min.打手与剥棉罗拉隔距2.5mm,A092 角钉帘速度50m/min,卷重量不匀率1.2%以下.仲长率1.35%以下.
染色棉以开清混合为主,多松少打、多混少落、多包抓取、多包混合、打梳结合、早落少碎,为防止过分损伤纤维而增加短绒,要求在开清棉的第一阶段以扯松和自由打松为主,第二阶段以较粗的握持打松为主,而最后阶段则以较细密的握持打松为主。各部件打手速度降低19%左右,流程不经过A036B,以减少一个打击点,严格发排包同执行,并做好回花的回用工作,A076C型成卷机的综合打手采用梳针式,减少棉块(束)的反复滚动,防止纤维纠缠成团。排包时要与其它纤维隔开,防止异性纤维混入。A002D型抓棉机要少抓、勤抓、少打击,以提高混合均匀性,A006B打手速度420r/min,A036C打手速度485r/min,A092打手速度420r/min,A076综合打手 速度800r/min,这样能允分发挥棉箱的混合均匀作用,主要工艺参数为:卷重量380g/min-395g/min,伸长率1.4%以下,重量不匀率1.25%以内.
1.3_2_2梳棉工序
天竹纤维整齐度好,抱合力小,梳棉机采用“轻定量、低速度、中隔距、小张力”的工艺原则,为更好地梳理和除杂,针布要保持四锋一准,以提高棉网清晰度和减少成纱棉结。采用中隔距板能减少纤维损伤,而且还能有利于分梳,增加纤维在锡林盖板间分梳和转移,减少纤维在两针面间漂浮和搓揉,从而减少棉结和纱疵。采用较小的棉网张力,降低棉网易落网的现象适当降低各部梳理速度,刺辊速度适当降低,而锡林刺辊间速比适当提高,以保证纤维顺利转移,梳棉工艺参数为:生条定量18.0g/5m~18.6g/5m,刺辊速度815r/min.锡林速度330r/min,道大速度21.5r/min,盖板速度84mm/min,锡林-盖板间距0.25mm,0.23mm,0.20mm,0.20mm,0.23mm,锡林-道大隔距0.13mm。
染色棉强力低,为避免损伤纤维,应适当降低各部速度。因染色棉的成熟度低,生条定量应偏轻控制,可减轻针面负荷,改善梳理效果,对棉束进行细致松解,并减小纤维间搓转,防止新棉结增加,出尘刀采用高小角度,以增加多排杂质的效果。采用瑞士格拉大针布,加强纤维的分梳,以提高纤维的伸直平行度。其工艺参数为:定量20g/15m-21.32g/5m,锡林速度:305r/min,刺辊速度800r/min,盖板速度198~218mm/min,锡林-刺辊隔距0.16mm,给棉板一刺辊隔距0.16mm,锡林-道大隔距0.10mm,道大速度18.5r/min~19.5r/min,锡林-盖板隔距(mm)为0.23,0.20,0.18,0.18,0.20。
1.3.2.3精梳工序
因染色棉均匀度差、短绒率高、成熟度差异大、单纤强力大、棉结多等特点,并且生条中含有大量的短绒和杂质,且纤维的伸直平行度较差,所以必须进行精梳加工,以排除短绒和减少棉结杂质,提高纤维整齐度,平行伸直度和分离度,降低条干不匀率,以提高成纱质量,采用整体锡林和定量偏轻的小卷;同时要保持锡林和顶梳针齿锋利,增大落棉隔距,减少色棉纤维的反复梳搓,减少棉结数鼋,精梳落棉率控制在18%~22%之间.
1.3.2.4并条工序
纱条的混合比例是否准确是保证色纺纱色差和质量的关键。要合理选择搭配根数和搭配位置,缩小台间于眼间的色泽差异,确保熟条色泽均匀稳定;采用顺牵伸工艺配置,以改善纤维的仲直平行度,使有色棉分布均匀,混比正确;色棉纤维硬脆,易断裂,一般将色棉条排在中间,以减少色棉纤维的损伤;纺色纺纱要适当降低并条机速度,以减少棉结,并条工序要以提高纤维的伸直平行度,改善条子内部结构为重点;并条机采用压力棒牵伸和顺牵伸,以改善熟条条干,降低纤维移距偏差和减少意外牵伸,在牵伸过程中,要保持牵伸区摩擦力界的强度和稳定性,以加强对纤维运动的有效控制。囚纤维抱合力差,喇叭口径适当放小.能约束条子,提高熟条条干.降低重量不匀率,车速适当降低,避免缠绕罗拉胶辊,其工艺参数见表2。

1.3.2.5粗纱与细纱工序
粗纱工序按“低速度、大粘度、大轴向卷绕密度、小集合器和钳口隔距”的工艺原则。发挥主牵伸区的主导作用,有利于控制浮游纤维,因为纤维间抱合力小,粗纱在细纱机上易产生意外伸长,所以粗纱定长不宜过大;适当降低锭速,稳定粗纱张力,能提高纤维的伸直平行度,减少意外牵仲和发毛粗纱,提高粗纱条干水平。粗纱根据染色棉性能和天竹纤维的特点,将后区隔距适当缩小,可保证纤维在后区允分仲商,并减少纤维损伤。适当增大粗纱捻度,轴向和径向卷绕密度,对改善粗纱质量和提高细纱综合质量极为重要。其优化工艺参数为:粗纱定量4.2g/10m~4.6g/10m,后区牵伸倍数1.25倍~1.32倍,捻系数80~88,锭速500r/min~550r/min,前罗拉速度142r/min~160r/min,轴向卷绕密度3.327圈/cm~3.375圈/cm,隔距22 x 28mm,加压量为26×15×18kg/双锭,钳口隔距3.0mm~4.0mm,中区集合器6×4mm-8×6mm,前区集合器8mm~10mm,萨氏条干不匀率15.8以下,粗纱重量不匀率在0.7%以下。
细纱工序采用弹簧摇架加压、软弹不处理胶辊、内外花纹胶圈、气圈控制环、国产上销、小孔径镀瓷导纱钩和渗硫钢领钢丝圈,后区牵伸倍数偏小掌握,集中前区牵伸,以加强纤维在牵伸过程中的有效控制,采用新型锭带,及时检查锭带张力和锭速,尽量减小锭速差异,降低捻度不匀率,以提高单纱强力和降低单强CV值,细纱捻度偏大控制,以保持须条间的紧密度,增加纤维间的抱合力,提高成纱质量其工艺参数:捻系数350~375,锭速12500r/min~13500r/min,钳口隔距2.5mm~3.0mm,隔距18.5×29mm,前罗拉速度160r/min-165r/min,平均成纱条干CV值为14.8%,百米重量偏差平均值为+0.2%-+0.3%,重量不匀率在0.8%以下。
2 成纱质量情况(见表3)
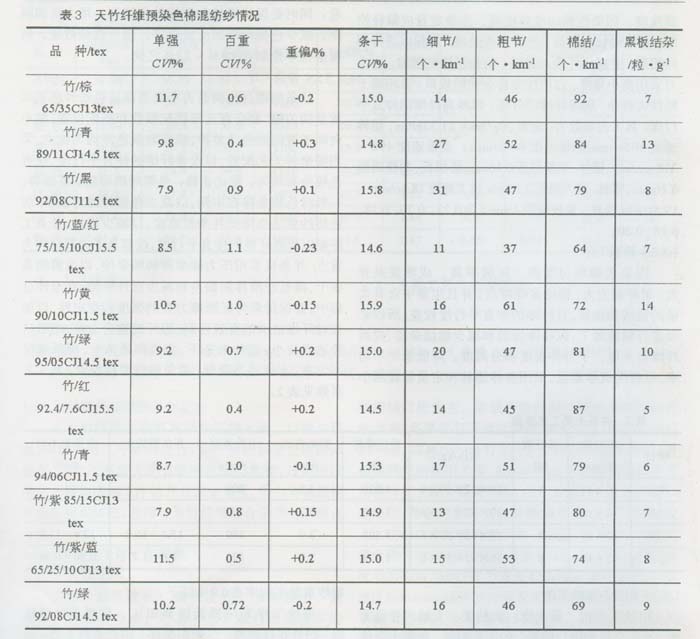
染色棉纤维强力低,弹性差,棉结多,成熟度和长度差异大,减少棉结和短绒是提高色纱质量的基础。在色纱加工中,保证天竹纤维与染色棉纤维混合均匀,能明显提高色纺纱强力。要保证混纺比准确和色泽均匀,混色方法以条混为佳。因色纺纱生产的主要问题是色差问题,因此清花工序要以开松混合为主,应多松少打、多混早落,尽量使色棉均匀混合,减少棉结和色点的产生机率;梳棉是影响成纱棉结杂质的关键工序,优化梳棉能提高生条质量;并条采用一混二并法能保证色泽稳定和均匀,容易控制混纺比。利用天竹纤维与染色棉加工的针织纱,可根据需要灵活搭配,色泽凋整方便,品种繁多,色泽丰富,风格独特;用其加工的针织物,色泽和谐牢固,织物表面能呈现出自然均匀活泼等优点,且悬垂性佳,手感柔软,穿着凉爽舒适,光泽亮丽,具有较好的天然抗菌功效,特别是吸湿性及透气性居各类面料之首,是夏季针织面料和贴身纺织品的首选面料,竹纤维与染色棉纤维产品开发种类繁多,市场前景十分看好。