驼绒具有细、柔、轻、滑、保暖性强等优良特性,可用以生产绒面丰满、手感柔软、穿着舒适的高档产品。但由于其可纺性较差,目前主要用于粗纺生产,且品种单调,质量档次也较低。因此,提高驼绒的可纺性,以期应用于精纺或半精纺生产工艺,从而生产出性能优异、品质高贵、风格独特的驼绒新产品。这对缓解目前毛纺原料紧张状况,拓宽驼绒的使用范围,增加其产品的附加值,都具有十分重要的意义。
2驼绒与70支澳毛理化性能的测试及结果
通过各种仪器对驼绒和70支澳毛的理化性能进行测试,结果如表1所示。
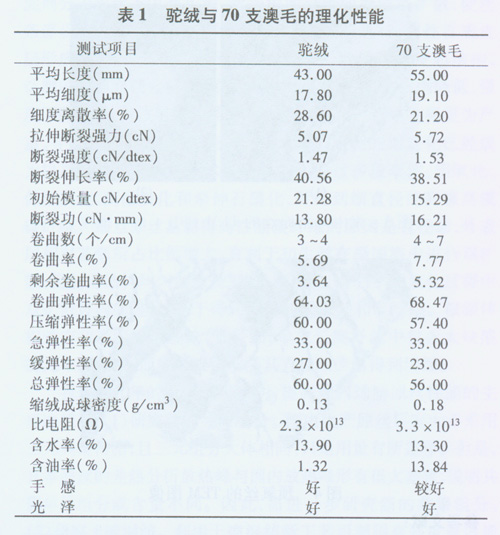
3驼绒可纺性影响因素的分析
3.1细度
纤维细,在相同的纱截面中纤维根数多,纱条均匀,手感柔软,纱中纤维与纤维之间的总接触面积大,拉断纱线时滑脱纤维比例小,纱的强度高。但纤维太细,加工中纤维容易扭结形成毛粒。对毛纤维来说,细度是决定可纺性的主要因素。由表1中可知,驼绒与70支澳毛细度接近,因此,从细度这一因素分析,它们的可纺性应该是接近的。
3.2长度
纤维长度对纱线质量和成纱过程的影响因纤维种类而异。短纤维含量对纱线强度和条干均匀度的影响更大。从表1中可知,驼绒平均长度低于70支澳毛,因此,从长度这一因素分析,驼绒的可纺性能稍低于70支澳毛。
3.3强度
纤维强度是决定纱线强度的最本质的因素,也是决定纺纱难易程度的重要因素。在其他条件相同时,纤维强度越高,成纱强度也越高,同时纺纱过程也越顺利。由表1可知,驼绒的断裂强力和断裂强度均小于70支澳毛,所以,这出.是影响驼绒可纺性能的因素之一。
3.4初始模量
纤维的初始模量是度量纤维材料在弹性范围内受力作用时变形大小的因素之一。一般来说,初始模量愈大,纤维材料的刚性愈高,在使用过程中变形愈小,纤维的柔顺性愈差。从表1可知,驼绒的初始模量高于70支澳毛,说明驼绒较70支澳毛刚硬,在纺纱过程中,表现为纤维的抱合力较小,加工不易等特点。它是驼绒可纺性能低于70支澳毛的主要因素之一。
3.5卷曲
适当的卷曲数和卷曲形态能改善纤维之间的抱合性能,使纤维成纱顺利,成纱质量好。另外,纤维的卷曲对织物风格、手感和弹性等都有影响。由表1中可知,驼绒的卷曲数、卷曲率和卷曲弹性率均小于70支澳毛,同时,卷曲形态又多呈空间立体卷曲,因此,纺纱时抱合力较70支澳毛小,成条成网困难,这也是影响驼绒可纺性能的主要因素之一。
3.6摩擦性能
摩擦性能可用纤维与纤维、纤维与纺纱机件的动、静摩擦因数表示。生产实践证明,适当的摩擦因数能提高纤维的可纺性能。摩擦因数太大,加工中容易产生静电,造成条子发毛,纱线毛羽增加,卷装成形不良,纤维缠绕机件,纱线断头增加而影响正常纺纱;摩擦因数太小,纤维抱合力小,须条容易拉断,影响纺纱工艺过程。纤维的摩擦因数与纤维分子结构、截面形状、表面粗糙程度和表面附着物有关。由电镜观察,驼绒表面鳞片边缘圆钝、光滑,因而摩擦因数较小,不利于纤维间的抱合,这也是其可纺性能不如70支澳毛的因素之一。
3.7缩绒性能
毛纤维集合体或毛织物在皂洗或其他类似水溶液中受到反复挤压揉搓,纤维问相互缠绕、毡并,纤维间的间隙变小,并渐趋紧密,不能再恢复分散原状,这一特性称为毡缩性。这一特性用于毛织物的整理中,称为缩绒性。影响因素有毛纤维的定向摩擦效应、弹性、鳞片形状、鳞片密度、纤维卷曲和纤维细度等。可见,毛纤维的缩绒性是纤维各项性能指标的综合反映,在一定程度上也反应出纤维可纺性能的高低。从表1可知,驼绒缩绒性不如70支澳毛,反映出其可纺性能不如70支澳毛。
3.8弹性
由表1可知,驼绒的伸长弹性率和压缩弹性率均高于70支澳毛,伸长弹性率高易造成纤维在纺纱梳理时回缩而形成弯钩纤维,使纤维有效长度变短,从而使纤维抱合力下降。压缩弹性高易造成纤维集合体之间间隙过大,不利于纤维之间的抱合。以上两种因素都不同程度地影响驼绒的可纺性能。影响驼绒可纺性能的因素很多,其中有些因素是不可改变的,有些因素通过改性处理可加以改善,这就为驼绒的改性处理,提高驼绒的可纺性能提供了理论依据。
通过分析,我们认为驼绒纺纱性能之所以较差,主要原因在于驼绒纤维之问的抱合力较小,主要表现在以下几点:
(1)驼绒纤维的卷曲数较少,同时呈空问螺旋不规则弯曲。
(2)驼绒纤维的表面鳞片边缘圆钝,且间距较大。
(3)驼绒纤维初始模量较高,表现为刚度较高,柔顺性较差。
4实验部分
4.1实验设计
本实验采用正交设计,以NaHSO3为处理剂,选择时间、浓度、温度三个主要影响因素,每个因素取三个水平(见表2)。
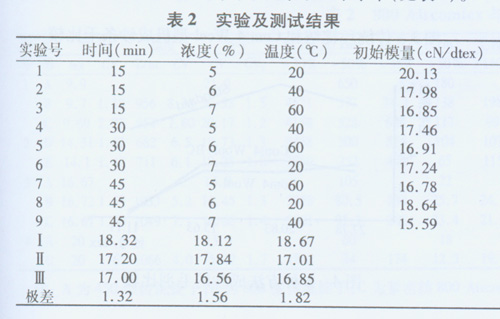
4.2实验材料、药品及仪器
材料为内蒙古分梳驼绒;药品为NaHSO3、氨水等;仪器为恒温水浴锅、分析天平等。
4.3试验工艺流程
分梳驼绒-润湿-脱水-改性-中和-水洗-脱水-干燥-改性驼绒
4.4实验结果与讨论
由表2可知,各工艺条件对驼绒改性影响依次为:温度>浓度>时间。以各因素的实际水平为横坐标,平均初始模量为纵坐标,作图1。由图1可知,初始模量随时间延长而降低。时间为15~30min时,初始模量的极差为1.12,时间为30—45min时,极差为0.20,说明30min以内初始模量降低较大;超过30min,初始模量降低较小,故选时间为30min。随浓度的增大,初始模量降低。浓度为5%-6%时,初始模量的极差为0.28,浓度为6%-7%时,极差为1.28,说明低浓度时,初始模量降低较小,高浓度时初始模量降低较大,故取浓度为7%。初始模量随温度的升高而降低。温度为20—40℃时初始模量的极差为1.66,温度为40~60℃时初始模量的极差为0.16,说明40℃以内,初始模量降低较大,温度超过40℃,初始模量降低较小,故取温度为40℃。
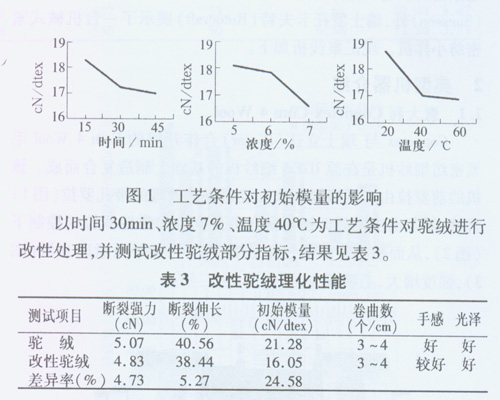
由表3可知改性后驼绒的初始模量下降幅度较大,强力下降4.73%,不影响其正常纺纱所需的强力,手感、光泽与原驼绒变化不大,说明改性驼绒没有丧失其原有的高贵感。
5结论
5.1通过化学处理,可不同程度地降低驼绒的初始模量,提高驼绒的抱合力和可纺性。
5.2 以NaHSO3为处理剂,在不影响驼绒纤维正常纺纱的前提下,较佳的处理方案为时间30min、浓度7%、温度40℃。