0前言
传统的包芯纱都是通过在细纱机上安装有长丝喂人部件完成两种纤维的包覆纺纱过程。我公司生产的棉涤包芯纱是在粗纱工序完成包覆,在细纱机完成纺纱。在粗纱机上包覆,在细纱机上完成包芯纱的纺纱工艺具有国际先进水平。
棉涤包芯纱是在改进的FL-6型粗纱机上,以短纤为芯、以棉纤维为包覆层所纺的包芯纱,因此棉涤短纤包芯纱织物既具有纯棉纤维吸湿、透气性好、不起静电、穿着舒适的优点,又具有纤维强力高、耐磨、挺括、免烫性好的特点,是理想的服装面料。该产品在我公司投产以来,产品一直专供日本市场,深受用户好评,同时又为我公司赢得了较好的经济效益。
短纤包芯纱的生产技术难点是必须保证成纱包覆良好,不允许纤维芯露出纱的表面;成纱表面光滑、疵点少,10万m7级纱疵(乌斯特公报纱疵样照A4+B4+C3+D2)少于2个。其目的是在布面上尽量减少修、织、洗,杜绝造成涤纤维外露而影响布面的染色效果。现将棉涤短纤包芯纱生产过程的技术措施及体会总结如下。
1棉涤短纤包芯纱原料的选择
棉涤短纤包芯纱的主要特点是要体现出棉纤维的特性,因此,短纤维要具有棉纤维的特点,需用特制的1.67 dtex×32 mm短纤维,短纤维比电阻必须在2 x 107Ω•cm以下,含油率在0.4%-0.7%,其目的是要求纤维的静电小,长度要与棉纤维长度接近,便于在粗纱、细纱罗拉握持牵伸中,能较好的控制纤维的变速运动,提高成纱条于均匀度;同时要求棉纤维能有效的包覆纤维,不至于使纤维外漏。
鉴于包芯纱织物是用于高档服装面料的生产,因此,对原棉质量要求较高,尤其是原棉中色花疵点要少,其目的是要包裹好涤纤维,色花疵点少可避免修织布面色花时造成纤维外漏疵点。原棉质量指标:品级129,主体长度为29.4mm,短绒率为12%,成熟度为1.65,细度为1.55dtex,断裂强力为3.8 cN,含杂率为1.6%。
2包覆比例的选择
在粗纱工序完成包覆是生产包芯纱的关键问题,其中包覆效果较为重要,合理的包覆比例是保证包覆效果的关键。如棉涤包芯纱19.5 tex,设芯的比例为x,则棉纤维包覆层厚度h为:
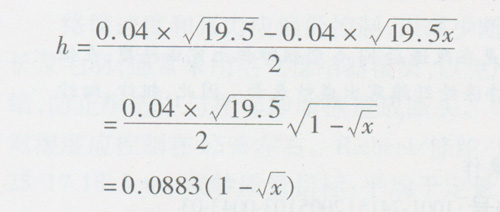
从上式中可以看出,如果x小,纤维占的比例小,则包覆层厚度h就大,棉涤包芯纱包覆效果越好,但是纤维含量少了,棉涤短纤包芯纱织物的抗皱、免烫和保型性好的特点就不够,因此,包覆比例非常重要。不同比例的纱芯直径与包覆层厚度对比见表1。
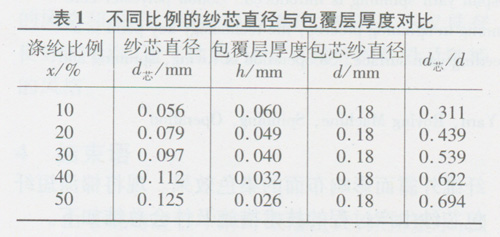
经计算,最适宜的棉涤包芯纱的比例为40%,但是在正常生产中,成纱的截面不可能是规则的圆形,同时纱芯也不会一直在纱的几何中心,因此,包覆层的厚度也不均匀,所以的比例应适当小些。我们选用的比例为30%,棉纤维包覆层比例为70%,这样,既能体现纤维良好的服用性能。穿着中棉纤维在外,不起静电、透气性好、穿着舒适,日本用户采用包芯纱织物制作的服装多用于特种行业和具有防静电要求的工作场合。
3 FL-6型粗纱机的技术改造及操作特点
3.1 FL-6型粗纱机的技术改造
FL-6型粗纱机为四罗拉双胶圈牵伸;德国SKF特制摇架、罗拉和胶辊。与传统粗纱机不同的是一套摇架需握持不同规格的四套喇叭口、集棉器、集束器,分别导人纤维条和棉纤维条,在特制托棉板的托扶下,利用粗纱的加捻作用,使从前罗拉输出的须条、棉须条在托棉板上进行包覆,一套摇架纺出的是两根包覆好的粗纱。粗纱机上纤维须条和棉纤维须条包覆过程见图1。
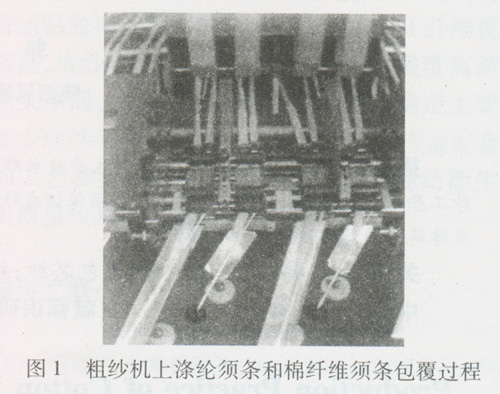
3.2粗纱工序操作要点
要保证良好的包覆质量,不允许纤维显露在成纱的表面。又由于有两根条子进行牵伸后包裹,须条、棉须条缺一不可,所以在粗纱工序与传统粗纱工序的操作有很大的不同。
(1)粗纱机前、机后光电断头自停装置必须灵敏,一根断条后要能及时停车,避免因机后断头造成缺包覆层或者缺纱芯、机前断头后飘头造成的纤维外漏。
(2)托棉板是包芯纱进行包覆的关键部件,从日常生产中发现托棉板高低位置、倾斜角度不适当极易造成包覆不良。为此,值车工巡回时只要发现棉网包覆不良就要立即调节托棉板高低位置、倾斜角度;粗纱机大小修理、翻改品种时托棉板高低位置、倾斜角度都要重新调节,直至每一根粗纱都包覆良好,方能正式生产。调试过程纺出的粗纱都要处理成粗纱头,决不能流入细纱工序。
(3)粗纱张力不适当也容易造成包覆不良,因此,粗纱张力要根据车间温湿度随时调节粗纱机锥轮的起始位置和张力齿轮。
(4)粗纱机后棉条接头不允许条与棉条同时接头,棉条与条在并条工序的落筒设置长度要有差距。粗纱机前接头值车工用手捏住网头开车,即从前罗拉开出约1 m的须条用手搓加捻后引入法兰,把纱头绕在粗纱上,待纱条包覆正常后,在粗纱压掌反向5cm处贴胶布粘住纱尾方可开车。贴胶布纱在细纱工序退绕到贴胶布位置时粗纱断掉,由细纱工序将该粗纱退回粗纱工序,由包芯纱粗纱值车工把接头处包裹不良纱处理干净,再送回细纱工序继续使用。
4细纱工序技术要点
为了保证良好的包覆效果,因此粗纱采用重定量,细纱工艺设计时后区牵伸倍数偏大、前罗拉加压偏大、罗拉握持距介于纯棉产品与涤棉产品之间。由于粗纱定量重,须条对胶辊的磨损大,胶辊极易造成凹心形成条干疵点,因此,胶辊一般采用邵尔A硬度84度的大漆处理胶辊,并且每天必须有专人使用便携式胶辊检定仪对车上胶辊进行检查。
通过工艺试验选用薄弓形W321型钢丝圈,由于该型号钢丝圈圈边外翻,与钢领接触点小,纱线通道光滑通畅,能有效的减少成纱毛羽或因钢领与钢丝圈摩擦造成纤维外露的疵点。
细纱工序操作与传统的细纱操作法有所不同,首先,换粗纱时不能包卷粗纱,必须将粗纱条引入细纱牵伸区纺出须条,用管纱接头,目的还是为了减少纤维的外露。
5络筒工序技术要点
根据用户要求,成纱5mm毛羽的数量必须控制在60根/10 m以内,因此,络筒应采用低速度、轻张力的工艺配置,以降低成纱毛羽增长率。选用№7-Ⅱ型村田自动络筒机生产包芯纱,对设备的要求是纱线通道光滑无毛刺,电子清纱器清除纱疵效率达到90%以上。每周对包芯纱各品种的生产效率、黄色按钮弹出率、打结失误率、断头率、清除纱疵的样品调查三个班次,分析原因,有针对性地向前工序反馈信息,及时采取措施。
自动络筒机生产包芯纱对接头捻结质量要求十分严格,打结时两端纱头一定要充分退捻、然后捻结,结头不能过大,否则容易产生布面白星疵点,影响染色效果。一般要求捻接头长度稍长、接头处稍细,但是捻接头处的捻结强力不能低于原纱的85%。
6 结语
生产棉涤包芯纱的原料质量是保证纺纱顺利的基础,短纤维长度为32 mm,一般国内不生产该规格的短纤维,需特别定制。棉纤维应选用等级较高、色杂少的原棉。棉涤包芯纱生产技术难点是保证成纱包覆良好、避免纤维外露,所以在设备管理,尤其在日常生产管理中对各种有可能产生纤维外露的因素制定预防措施,并认真实施,并加强对措施执行情况的检查。
用户要求成纱7级纱疵数不超过2个/10万m,通过对纱疵类型的分析,A4+B4+C3+D2纱疵主要产生在并条、粗纱工序,因此并条、粗纱工序清洁、吸风装置必须良好。络筒捻结不良容易造成D2纱疵,所以,每天要有专人对络筒每一个锭子的接头捻结质量进行检查。粗纱、细纱工序的操作与传统粗纱、细纱有很大不同,因此,包芯纱的粗纱、细纱值车工要经过专门培训,合格后方能上车。对包芯纱生产的各工序应制定把关措施,责任落实到人,确保包覆不良纱疵流入布面。