关键词:竹/涤包芯纱;设计思路;工艺研究;技术措施
随着经济的发展和社会的进步,人们对衣着提出了更多、更高的要求。尤其是中青年消费群体更加注重个性化、高档化和时尚化,崇尚与追求舒适、健康以及自我体现。在服装面料方面,不仅注重其外观效果,而且对服用性能、保健性能等均有较高要求。为了满足与引导人们的消费需求,我们设计生产了竹/涤包芯衬衫织物和针织用股线。本文着重讨论该类产晶的开发思路、原料选配特点及纺纱工艺技术。
1 产品设计思路
经过充分的市场调研、预测,我们确定开发研制竹/涤包芯产品。在产品规格设计方面力争达到品种风格的协调统一。
1.1 竹纤维的特性
传统的植物粘胶纤维在生产中多采用针叶树木和棉短绒为原料,随着木材的大量砍伐和棉纤维增长速度的放缓,植物粘胶纤维原材料出现缺乏,而竹子是分布广泛的速生植物,资源丰富。竹浆纤维是采用无污染的竹子制成浆粕喷丝而成。竹浆纤维作为一种新型纤维素纤维,跟常规棉、木浆纤维相比,有许多独有的特点:手感柔软、天然抗菌、吸湿放湿更快、透气性能优良,具有优良的着色性、反弹性、悬垂性。竹纤维内部分布着大大小小的空隙,可以迅速吸收和排放水分,其吸放湿性、透气性居各种纤维之首。炎热的夏季穿上用竹纤维面料制作的服装,使人顿感清凉、爽快,所以被业内专家称为"会呼吸的面料"。竹纤维还有一个更加可贵的特点,就是她自身具有抗菌性和防臭性能,其抗菌率达到71%。用竹纤维作外包纤维能使服装面料满足人们追求高档、健康、舒适的消费心理。
1.2 竹纤维的性能分析
竹纤维大分子聚合度和结晶度较低,纤维断裂主要表现为大分子间的滑落。因此,纤维强度低,伸长度大,柔软,吸湿能力强。纤维吸湿后,水分子进入纤维内部的无定型区,减弱了大分子间的结合力,使分子间在外力作用下容易伸直和发生相对滑移,表现为吸湿后强力下降明显,伸长率有所增加。
1.3 竹纤维与其他纤维素纤维物理性能比较(见表1)
表1 竹纤维与其他纤维素纤维物理性能比较
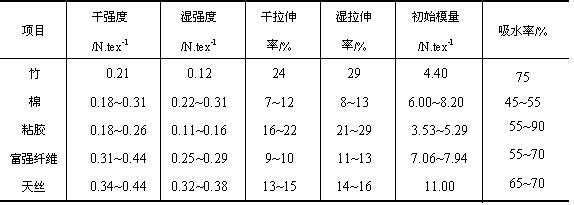
竹/涤包芯纱的外包纤维选用新一代"绿色纤维"--竹浆纤维。竹/涤包芯纱的芯丝选用30dtex、50dtexFDY长丝。由子FDY丝条光滑、柔软,而且具有较高强力,作为芯丝即不会破坏竹纤维柔软滑顺、贴身服用舒适的风格,又能够在织物中起到增强作用,克服了竹纤维强力较低、保型性较差的弱点,同时还可以改善面料的尺寸稳定性,使服装永久保型,不用熨烫。
外包纤维与芯丝含量的选择,我们在满足织物保型性要求和保证长丝能完全包覆在纱条中心不裸露的前提下,经过多次实验选定芯丝含量在20%-35%之间效果较好。
2 纺纱品种、原料检测及工艺流程
2.1 纺纱品种
竹/T(33dtex) 14.8 tex机织用单纱
竹/T(56 dtex) (18.4 X2) tex针织用股线
2.2原料检测数据
竹纤维质量情况见表2。
从纤维检测结果看,我们所用竹纤维细度较粗,干、湿态断裂强度均较低,并含有一定纤维疵点。
2.3 纺纱主要工艺流程

3 主要技术难点及工艺技术措施
通过纺纱我们认为竹纤维的可纺性能与粘胶基本相同。但纤维细度比较粗,达到1.95 dtex,造成单纱的外包纤维根数减少,单纤断裂干湿强度均较低。为了提高竹/涤包芯纱质量水平,我们在纺纱各工序采取了如下措施。
3.1 清花、梳棉工序
清花采用薄喂入、轻打多梳、少落的工艺原则。为了保证圆盘抓棉机运转处子较高水平,打手每次下降3mm,小车刀片伸出肋条3mm,做到勤抓少抓,使纤维充分开松,适当放慢各部打手转速。棉卷定量不宜过低,否则容易产生破洞。我们设计的棉卷干重是425g/m。
梳棉采用轻打多梳、尽量减少纤维损伤、适当增加落棉、多排除纤维疵点的工艺原则。
3.2 并条工序
并条工序以提高纤维平行伸直度、改善条干均匀度、降低重量不匀为重点。并条采用三道并合6根喂入,顺牵伸工艺路线。适当加大头、二并的后区牵伸倍数,以减少棉结、粗节;加大耒并前区牵伸倍数,以提高纤维伸直平行度。
3.3 粗纱工序
粗纱的重点在于提高条干均匀度。结合细纱工艺方案确定合理的粗纱工艺,适当调整粗纱张力。通过对比实验,优选了牵伸区主要工艺参数。粗纱捻系数的合理选择非常重要。由于竹纤维较粗纤维间抱合力相对较小,故粗纱捻系数应偏大掌握才能保证粗纱在退绕过程中没有意外伸长。我们将粗纱捻系数确定为80。
3.4 细纱工序
细纱是包芯纱生产的关键工序,为了纺好包芯纱我们重点解决了以下四个关键技术难题。
3.4.1 细纱机粗纱架改造
目前大多数厂家生产的FDY卷装都比较大,一般一个丝筒重量在5 kg左右,直径在300mm左右。在纺制包芯纱时,细纱每一个锭子要对应一个长丝筒子,把400多个丝筒都摆放到细纱机上难度很大。我们经过多种改造方案对比,最终选定一种比较简单可行的机架改造方法,使长丝筒子均匀摆放在粗纱架上方,挡车工操作方便,同时对机架本身基本无大的改造。在纺纱过程中DY采用被动退绕方式。包芯纱纺纱过程简图见图1。
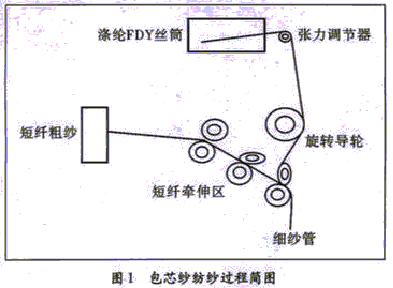
FDY丝条很光滑,丝与 丝之间附着力极差,在被动退绕过程中长丝易脱圈,致使退绕张力忽大忽小极难控制。为了减少脱圈造成的张力波动,我们将长丝引出方式改为沿筒子外圆的切线方向拉出,并使长丝经过张力器进入张力调节区。丝条张力大小由张力器控制,张力过小影响包覆质量,张力过大长丝进入前罗拉时易出现打顿现象,而短纤须条是以恒定的速度从前罗拉输出,在长丝停顿瞬间,短纤须条就会屈曲,造成纱条表面形成类似"棉结"的疵点。所以张力器张力大小应适中,锭与锭之间张力应均匀才能保证成纱质量。经过反复调整张力器张力,我们摸索出一套比较成熟的调整方法,能确保长丝退绕顺畅、张力适中。
3.4.3 竹/T包芯纱的包覆效果
包芯纱的包覆效果对成纱质量、后工序加工难度、织物外观影响非常大。影响包覆效果的纱疵主要有包覆不良纱、空心纱和裸丝三种情况。所谓包覆不良就是指外包短纤没有均匀包覆住芯丝,芯丝断断续续露出纱条表面。为了解决包覆不良问题我们把粗纱横动装置停掉,使短纤须条输出位置基本恒定,并在前皮辊上方加装了旋转导丝轮,导丝轮的出丝口位置应对准牵伸须条中部,这样就能保证外包短纤均匀地将长丝包覆于中心。导丝轮位置调好以后应固定,以免走动。另外通过对比实验我们认为涤长丝在一定张力下喂入前皮辊可使短纤包覆较为牢固。至于空芯纱疵和裸丝纱疵主要是由于粗纱或长丝断头没有及时发现,造成缺项喂入而形成。所以挡车工在操作时应加强巡回,认真查看,发现问题及时解决。同时前纺车间应尽量提高粗纱质量,减少粗纱断头。细纱挡车工在摆放长丝筒子过程中应轻拿轻放,不要使长丝外层和端面刮伤或脱圈。
另外粗纱定量对包覆效果也有一定影响,因为粗纱经过卷装以后其截面是椭圆型而不是圆形。在进入细纱牵伸区时粗纱条不断翻转,其椭圆截面不断改变角度,这就造成进入前罗拉的纤维须条不能保持恒定的幅宽,须条与芯丝的相对位置也会发生不断变化,必定会影响包覆效果。为了改善这一现象,我们对粗纱定量与包覆效果的关系做了对比试验。试验发现粗纱定量过轻,其牵伸须条幅宽及相对位置变化就越明显,粗纱定量略重其牵伸须条幅宽和相对位置变化就平稳一些。经过对成纱质量测试我们得出结论:粗纱定量对包芯纱条干均匀度、包覆效果有一定影响,粗纱定量应适宜,不宜过轻。
3.4.4 细纱捻系数选择
我们首先考虑包芯纱捻系数与成纱强力的关系。按照常用的捻系数,包芯纱的强力大干短纤纱的强力。如果继续提高捻系数,短纤做成的皮纱强力变化曲线会逐步提高,但涤长丝强力变化曲线将逐步降低。故在一定捻系数变化范围内竹/涤包芯纱强力与捻系数关系不大。所以我们在考虑捻系数选择时,把改善包芯纱耐磨性和避免成纱扭结两项因素放在首位,捻系数对成纱强力的影响仅作为参考。
由于包芯纱芯丝比较光滑,单纱在后工序与机件磨擦过程中,外包短纤易剥落,造成裸丝纱疵。提高包芯纱捻系数可以使短纤与芯丝紧密抱合,对改善包芯纱的耐磨性有利。但是长丝具有较强的抗扭性,如果捻度偏大,包芯纱在后工序加工过程中就容易扭结形成小辫子。故包芯纱捻系数应慎重选择。我们在兼顾各方面因素的基础上,将竹/涤包芯纱捻系数选定为350左右。单纱质量见表3。
表3单纱质量
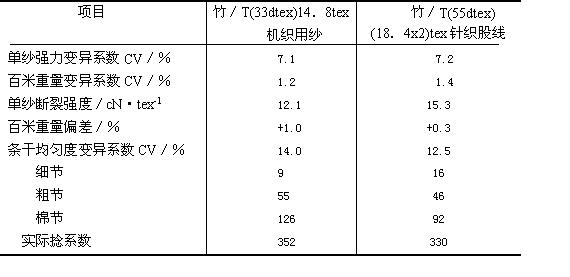
捻线在1391型捻线机上生产。为了降低成本,竹/涤包芯纱未经蒸纱定型直接上捻线机。由于单纱在捻线机筒子架上退绕过程中没有张力控制器,单纱极易形成小辫子。为了解决此间题,我们在单纱筒子上加装了张力控制膜。张力控制膜的作用是增加单纱在筒子表面的附着力,使其在退绕时不会出现滑脱现象,从而杜绝了小辫子形成的机会。张力膜的作用还可以随着筒子直径的减小而自动控制张力。
4 结语
竹纤维作为一种全新的纤维素纤维,以其独特的性能:手感柔软、天然抗菌、优异的吸湿放湿和透气性能等引起了纺织产品设计者的关注,受到了广大消费者的青睐。竹/涤包芯纱的研制实践,证明了我们的设计思路完全正确,工艺技术成熟,各工序生产稳定,产品质量一直保持在较高的水平。
竹/涤包芯纱的研制成功为纺织品市场增添了一朵绚丽的奇葩,同时也为企业带来了可观的经济效益。