一 缆型纺机理
在纺纱工程细纱工序中,一般都是一根粗纱经牵伸成为一股细纱,缆型纺和传统纺纱不同,当经牵伸后的须条在出细纱机前箝口时,有一个分割轮将其分割成若干股纤维束,那些纤维束在纺纱张力的作用下进入分割轮的分割槽内并在的纺纱加捻力的作用下,围绕自身的捻心回转,从而具有一定的捻度(纤维束加捻);随着纱线的卷绕运动,这些带有一定的捻度的纤维束又向下移动,离开分割轮后汇交于一点再围绕整根纱线的捻心作回转运动(纱线加捻),两次加捻最后形成一种具有特殊的、不同于传统纱线结构的新型纱线——缆型纺纱。(参见图一)
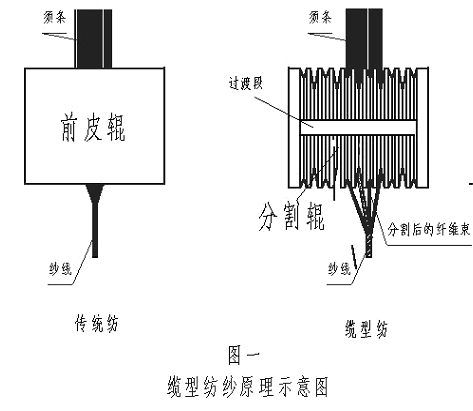
比较缆型纺和sirospun(赛络纺)可以发现:
sirospun只是两股纤维束汇交而成的纱线,而缆型纺纱是由两股以上的纤维束汇交而成;;sirospun中每一个纤维束是由一股粗纱牵伸而成,两股纤维束之间是互不干涉的,而缆型纺的纤维束是由同一须条分割而成,这些纤维束的组成是在不断的变化着,纤维束之间会互相牵涉。
根据纱线加捻理论可知缆型纱由于纱线中有带有一定捻度的纤束的存在,纱线的捻心将处于各纤维束的几何中心。在捻度相同的条件下,缆型纺纱中处于捻心的纤维数量要少于传统单纱中纤维数量(图二),

须条分束成若干股纤维束后,每一股纤维束在纺纱加捻力的作用下围绕自身的捻心回转,在纤维束汇后后又围绕纱线的捻心回转,这就相当两次加捻,纱线之间的纤维抱合显然要比传统单纱来得紧密,而且每一股纤维束在接近汇交点的时候,其外露的纤维头端很有可能被相邻的回转着的其他纤维束所捕捉,这样纤维头端外露的可能又相应地减少,而且纱线中纤维的抱合更为紧密。
缆型纺的关键是分束,但分束的方法和形式具体地说分割槽的宽度、深度、形状直接关系到纺纱支数及纱线的质量,而分割轮的直径、材料、结构则涉及原料长度要求操作简便与否使用寿命等问题。缆型纺装置采用了进行特殊处理的高强度耐摩擦的材料作为分割轮的基材并在设计中充分考虑了国内毛纺行业使用的原料情况以及常见的纺纱支等因素,并创造性地在分割轮上设置了过渡段。
所谓过渡段是指在分割轮上有两条深度与分割槽底部相当的光滑圆弧槽。随着纺纱运动分割轮在不停的转动,和分割轮接触的须条遇到分割槽时被分割成纤维束后进入分割槽,纤维须条遇到过渡段时就重新并合在一起——须条不是始终处于被分束的状态,经过一段时间的分束后须条有一个重新汇聚时段,就象人们梳理头发,遇到梳不通时须将梳子退出一样,过渡段的设置减少了纤维被强行拉断的机会。
过渡段的另一个作用就是重新分束。纤维须条在处于过渡段时,纤维汇聚在一起,此时整个纤维须条将随着皮棍的转动会产生水平向的游移,原来在某个分割槽位置的纤维随着游移可能会进入另外一根槽的位置,当分割槽再度将须条纤维分割成纤维束时,会出现一根纤维的头端在这根槽内,而纤维的尾端在另一根槽内的情况。这样增加了纤维的转移,使纤维和纤维之间纤维束与纤维束之间有着更比传统单纱更为复杂的结构,纤维间抱合更为紧密,从而提高了纱线的耐摩擦性能。
缆型纺纱的结构电镜照片如下(图三):

图三中可以明显看出缆型纺纱中有纤维束存在(由于纱线在拍电镜时,须切片,纱线在外力的作用下会发生形变,但依然可以看见缆型纺纺纱中有不同形状和大小的纤维束存在。图片所以有大小,为的是两照片放大倍数一致)。
二 缆型纺纱的特性
缆型纱特殊的结构赋予纱线的特殊性能,表一,表二是同工艺条件下缆型纱和传统纱的性能及毛羽对比。
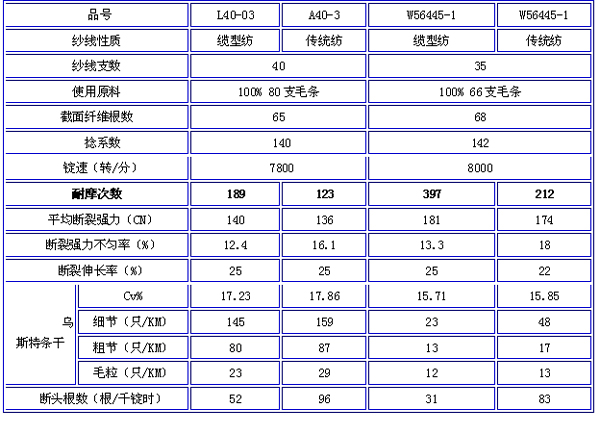
表二 缆型纺纱和传统单纱物理指标对比
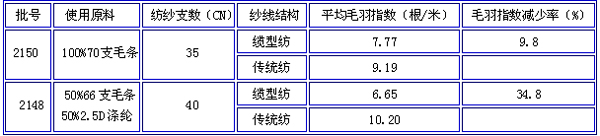
以上两个对比,可以知道缆型纱在强力伸长条干等方面接近或优于传统纱,但缆型纱的耐摩擦次数要比传统纱提高50%~133%,毛羽要比传统纱少9.8%~34.8%,纺纱断头率在锭速8000rpm时要比同工艺的传统的单纱减少50%。很显然,毛羽少,耐摩擦性能好是缆型纱的特点,而这两个特点体现在织造中,那就是织造效率高,可织造纱线支数高。
五 缆型纺纺纱的工艺
1 原料的选择
1)原料的细度 作为单纱织造纤维的截面根数应该在65根左右。试验证明当原料变细,纤维根数增加时,缆型纱的CV%值、细节、断裂伸长率各项质量性能指标虽然都有所提高,但耐摩擦性能却明显下降。这是由于羊毛纤维细度越细,单纤维的强度就越小。
因此缆型纺原料选择时,必须同时虑及纱线条干质量和纱线的耐摩擦性能,在条干的品质指标符合要求时,尽可能选用粗的原料,这不仅可以降低原料成本,而且还可以提高缆性纱的耐摩擦性能。
2 ) 原料长度 在原料细度决定的情况下,所用的原料越长,缆型纺纱的各项指标越好。
在原料细度决定的情况下,要求原料的长度长这就意味着原料中的短纤维含量要低。
2 捻度的选择
捻度的选择应根据原料的可纺性能和产品的要求来决定,但缆型纺的捻度选择有其特殊性。缆型纺需要分束,捻度太小,虽然有分束的现象存在,但每一股纤维束的捻度不大,纤维抱合不紧,耐摩擦性能不明显,而捻度太大,强大的加捻力将阻止了纤维的分束,纱线也就没有缆型结构。因此缆型纺不适宜纺强捻纱。进一步研究缆型纺的捻度,可以发现当捻度逐渐增加时单纱的耐摩擦性能不断增加,缆型纺的耐摩擦性能也不断增加,但捻度超过某一值之后单纱的耐摩擦性能继续增加,而缆型纺的耐摩擦性能却逐渐降低。
缆型纺也有个临界捻度。缆型纺临界捻度也是是随纺纱支数和原料的变化而变化的,纺35支全毛纱纱时,其临界捻系数一般在150左右。探讨缆型纺临界捻度,还可以发现当捻度达到临界点时,缆型纺纱不但耐摩擦性能最好,而且纱线的其他物理指标的综合性能也最好
总而言之,缆型纺除了要对原料进行选择和注意缆型纺临界捻度这两个要求以外其他纺纱工艺参数还是遵循传统的纺纱的工艺要求。
3 织造效率和织物性能 表七是缆型纺纱和传统单纱织造效率对照表。
实践证明缆型纺纱的织造效率一般要比同品种的传统单经单纬提高15%左右。对各种缆型纺面料进行服用性能的试验比较,数据表明缆型纺面料的抗起球,透气性和弹性角要优于同类传统单纱产品。
五 结语
缆型纺是一种新型的纺纱技术,缆型纱的特殊结构决定了它毛羽少和耐摩擦这两个特点。在原料及捻度选择合理的条件下缆型纱的物理性能及织造效率明显优于传统的单纱。缆型纺面料的抗起球能力、弹性、透气性都明显优于传统的同品种单经单纬产品。
缆型纺作为一种新型技术,不但可以提高单纱织造效率,还可以应用缆型纱的特性生产新一代的产品,例如抗起毛起球针织绒,双经单纬等。就如同双组分纺纱一样,关键在于用好这一种新型技术。