紧密纺纱技术的发展经历了理论研究和应用开发的过程,紧密纺纱设备已被多家纺机厂成功研制和推广应用。近年来国内纺机厂商也纷纷致力于紧密纺纱设备的研发,力图研制出具有自主知识产权的创新结构,以推动国内环锭纺纱的技术进步。
紧密纺纱技术的推广应用主要关系到设备研发制造厂、纺纱企业以至纱线的下游应用厂,要研制紧密纺纱设备、开发生产紧密纱线产品,应深入了解紧密纺纱技术的价值及其体现、应用成本、知识产权、紧密纺纱设备选型及其国产化创新等状况与信息。
1 紧密纺纱技术的价值及其体现
1.1纱线的品质
紧密纺纱技术是在纱条加捻前改善纤维分布状况和完善须条结构并使之理想化,是通过附加在环锭纺罗拉牵伸与加捻之间的对须条气动凝聚或集聚装置来实现,能显著改善纱线品质,可以用两个字来概括:洁、强。
1.1.1 洁
纱条光洁——毛羽特别是长毛羽数大幅度减少、毛羽数变异改善;纱条洁净——条干及常发性疵点改善;环境洁净——生产过程中飞花减少、生产环境有效改善;布面洁净——毛羽减少使后续工序疵点增量降低。
1.1.2 强
断裂强度提高、强力变异减小——生产过程断头减少、成品强度增加;断裂伸长增加、强伸变异减小——纱线负荷增强、成品耐磨耐疲劳;断裂功增大——成品强度增加、成品耐磨耐疲劳。
纱线品质在这两方面的改善正是业界所期待的,其直接体现出了紧密纱的价值。在传统的环锭纺纱技术上采用其他技术手段难以达到同样效果。
1.2资源和环保
对紧密纺纱优势的理解可以从更高的一个层次去认识,那就是资源和环保。一般来讲,我们比较容易感觉到毛羽的危害。其实毛羽特别是长毛羽的存在首先是一种浪费,是纤维资源的浪费。那些离开纱条体的纤维端——毛羽,未能被捻人纱体,从而削弱了纱条的整体强度,影响到单纱断裂强度及其相关品质指标。而且还造成后续工序中更多的浪费,可以说下游工序的一些工艺在很大程度上都是针对毛羽多及强度不足而设置的,如上蜡、上浆、烧毛及捻线等,在前纺流程中增加精梳工序在很大程度上也是为了减少毛羽,提高强力,改善外观。各种附加工艺所造成的资源浪费具有不可估量的损失。
紧密纱可以采用较少的捻度并能保证成纱强力,从而减少纺纱的能源消耗,提高产量。紧密纱强力和毛羽得到改善,可以用较低等级长度的原料纺出较好品质的纱线,从而降低原料成本。
所有的资源浪费都是非环保的,因而紧密纱能减少上述各项浪费和损失,这就是环保;其次,紧密纺还能减少断头,提高效率;此外,生产过程中飞花的减少等都是环保效应。
紧密纺纱技术在纱线品质、资源利用、综合能源消耗及环保等方面都体现出了应有的价值。
1.3降本增效
在应用紧密纺纱技术后,纺纱企业能直接体现经济效益的降本增效途径有三个:配棉成本适应性地降低;吨纱用棉量适应性地减少;细纱机单产适应性地提高。
1.3.1配棉成本
当今纺纱原料价格不断攀升,纱线售价中原料成本的比例日益加大。采用紧密纺纱技术后,在保持与普通环锭纱品质略优的情况下,可以适当地降低配棉的等级长度,以降低原料成本,如降低0.5个配棉等级或l mm的配棉长度。
1.3.2吨纱用棉量
吨纱用棉量直接关系到纺纱成本,采用紧密纺纱技术后,可以适应性地减少吨纱用棉量,特别是精梳纱,如通过降低精梳落棉率来减少吨纱用棉量5%~8%,仍可保持适度的纱线品质优势。
1.3.3细纱机单产
由于紧密纱强力、毛羽等指标的实质性改善,在满足下游工序要求的情况下,细纱机单产的提高可以有两种单独或交叉的实施方式,一是保持纱线捻度不变提高锭速;二是保持锭速不变减少纱线捻度。细纱增产的比例最大可达20%左右。
上述三项可单独或交叉实施,根据纺纱企业的原料、纺纱条件和纱线下游应用要求等现状进行优选,适应性地达到降本增效的目的。
采用良好性价比的国产化紧密纺纱设备后,有望仅通过上述降本增效措施,便能消化和抵补全部或大部分紧密纺纱技术的应用成本。
1.4紧密纱的增值应用
紧密纱的价值是靠品质特征通过市场售价体现出来的。紧密纱的下游增值应用已经正在慢慢拓展,将逐渐形成一种特定的需求,这种应用需求同样需要下游企业和下游产品的创新,因而也需要待以时日才能形成规模。
除了紧密纺纱设备或装置的投资成本下降外,紧密纱的增值应用是推动紧密纺纱技术发展最重要的动力。
2紧密纺纱技术的应用成本
2.1设备投资成本
设备投资成本按照在普通环锭纺纱机上附加进口和国产紧密纺纱装置的投资成本进行估算。进口的紧密纺纱装置价格为每锭人民币800元~1000元左右,以中间价格计算为每万锭900万元,国产的紧密纺装置目前的报价在每锭人民币280元~380元左右,以中间价格计算为每万锭330万元。紧密纺纱装置以5年快速折旧计算年折旧费用并适当计人利息费用。
2.2 日常运行成本
紧密纺纱技术的主要运行成本是凝聚吸风电机的能耗费用、凝聚元件的消耗费用及紧密纺纱装置的部件耗材与维护等其他费用。吸风电机的能耗约为万锭70 kw•h,以电价O.55元/kW•h、年工作330天、每天工作24 h计,吸风电机的万锭年能耗费用约为30万元。凝聚元件的消耗费用以网格圈或织物圈单价为5元、使用寿命为6个月计,万锭年消耗费用为10万元。其他费用以年消耗4万元估算。
2.3应用成本示例
表1为几个典型精梳棉纱品种采用国产化紧密纺纱设备后应用成本计算示例表,计算数据仅供参考。

通过表1计算结果可以看到,紧密纺纱的万锭年应用总成本并不是一个小数目,但分摊到吨纱的费用与棉纱市场价之比并不大,这些应用成本必须由纺纱企业降本增效和棉纱的市场售价来抵补。
3紧密纺纱设备的知识产权
3.1知识产权现状
经过十多年的探索和研发,紧密纺纱技术已进人成熟期,凭借着技术优势国际上几家著名纺机厂的产品也已进入收获期。与所有市场前景明朗的新技术、新产品一样,紧密纺纱技术受到业界的看好与追捧,也会遭受抄袭和仿冒。但是具有战略眼光的研发者早已利用起专利制度的武器,构筑起技术垄断的壁垒,在全球一统的市场上经营起独断的技术和产品。
检索中华人民共和国知识产权局的专利文献库,截至2003年12月,有关环锭纺紧密纱技术已授权的专利申请案有五十多件,其中约70%为国外厂商所申请,国外申请中除了马佐里的一件实用新型专利外其余全都为发明专利,国内申请占30%,大部分为实用新型专利。这些申请案中涉及目前已成功推出的凝聚结构型紧密纺纱装置,包括抽吸鼓式、网格圈式、织物圈式和带孔胶圈式等。除此之外,许多尚未推出产品的紧密纺纱凝聚和附加的功能结构也被密集地保护起来。
国内以东华大学为首的申请人获得了十多项有关环锭纺紧密纱纺纱技术的专利权。
分析国内外申请人在我国的紧密纺纱技术专利申请状况,有以下几点值得关注:
(1)国外申请的授权数占授权总数的70%,其中97.5%为发明专利,瑞士立达公司的申请量占国外申请的78%;
(2)国内申请的授权数占授权总数的30%,国内申请的发明专利占国内申请授权专利总数约17%,东华大学的申请量占国内申请的近50%1.
(3)国内申请的起步时间迟于国外约七年。
国内外申请人在我国的紧密纺纱技术专利状况存在较大差异,这种技术研发成果的反差,反映出以下几方面的薄弱环节:技术发展的前瞻意识、技术创新与专利意识、技术研发力量方面、技术信息更新方面等。
3.2专利纠纷的预防
3.2.1 紧密纺纱的技术领域
紧密纺纱技术是在环锭纺罗拉牵伸与加捻之间对纤维须条的气动凝聚或集聚技术,因此按照IPC(International PatentClassifieation)国际专利分类,其分属D大类的纺织、造纸,逐级细分的类别为Dol天然或人造的线或纤维、纺纱\D01H纺纱或加捻\D01 H5牵伸设备或机构\D01H5/72纤维聚导器。
在国外厂商的40件申请案中,除了一件的分类为:B65G15/30,是针对凝聚输送带的,其余都为D0lH纺纱或加捻类,其中DolH5/72纤维聚导器小类有14件,占三分之一强。
在纺纱行业\环锭精纺\须条牵伸\纤维集聚这个狭窄的领域里,积聚了如此多的专利保护,无论对于设备研发生产还是设备购买使用企业来说;都必须认真和谨慎地予以审视。
3.2.2设备研发制造厂
对于设备研发制造厂,在紧密纺纱狭窄的技术领域专利密集保护的情况下,国产化紧密纺纱技术要在不违反新颖性和创造性原则的情况下进行创新和有效的专利保护,在不侵权的情况下实施制造和生产已相当困难。
因此,紧密纺纱技术的研发制造厂应在深入了解国内外现有技术特别是专利技术的基础上,一方面避免重复研发,积极开拓创新,力争自主知识产权;另一方面在借鉴吸收已有技术,推出产品时要把握尺度,避免发生侵权事件。
在进行产品创新并申请和取得实用新型专利权后,仍应在推出产品前进行细致的专利检索。由于中华人民共和国专利法规定对实用新型专利申请不进行实质审查,只设置公告和授权后的宣告无效程序,因此,实用新型专利的法律状态稳定性相对发明专利的差。若不进行专利检索而直接投产,很有可能由于他人抵触申请的存在而造成专利权被宣告无效和成为侵权事件的被告。进行专利检索时应仔细解析专利文献,特别是权利要求书中独立权利要求所保护的特征部分应特别重视。
另外,必须引起重视的是,对于改进型的专利申请,专利权无论是实用新型或发明,如果其改进涉及另一项他人的有效专利技术且实施时必须应用他人专利中独立权利要求所保护的特征部分的,则在未取得他人专利许可的情况下实施该项改进型专利,也同样构成侵权。
发达国家厂商为了在竞争激烈的国际市场上获得并维持竞争的优势,便在具有良好市场前景的目标地域展开激烈的专利攻势,不失时机地申清专利,形成了坚固的专利保护网,以达到垄断当今和未来产品市场和技术市场的目的。这种强势策略的实施,必然会给目标地域的技术市场带来冲击。住电子等高科技领域(如DVD、背投彩电技术等)专利纠纷已有不少实例,在纺织方面也有。因此,在紧密纺纱技术国产化的起步阶段,应该及早注重专利意识,减少日后专利纠纷的发生。
3.2.3设备使用企业
对于购买设备的企业,依照中华人民共和国专利法第一章第十一条:“发明和实用新型专利权被授予后,除本法另有规定的以外,任何单位或者个人未经专利权人许可,都不得实施其专利,即不得为生产经营目的制造、使用、许诺销售、销售、进口其专利产品,或者使用其专利方法以及使用、许诺销售、销售、进口依照该专利方法直接获得的产品”。
因此,如果购买的设备是属于侵权的产品,也同样是违反了专利法。棉纺企业和纺机销售商在选购或经销紧密纺纱设备或装置时,也应考察设备制造厂商的知识产权状况。同时可以在买卖合同中增加如下知识产权条款:“卖方保证买方使用卖方货物不会受到第三方提起的侵犯专利、商标、版权或专有技术的索赔与诉讼,否则卖方应承担买方因此受到的损失。”
4紧密纺纱设备选型
4.1 紧密纺纱设备结构形式及特点
国际上推广应用的紧密纺纱设备或装置主要有4种形式,见表2。
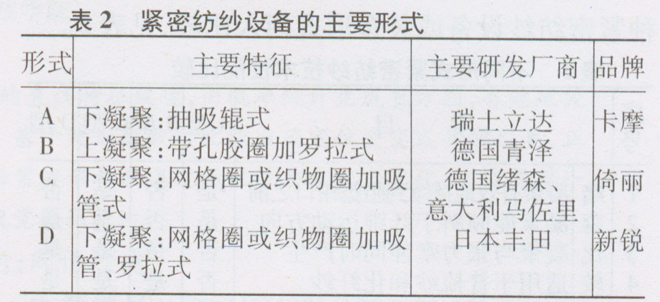
在上海纺机展展出的国产紧密纺纱设备或装置的结构形式为C和D两种。其中C型技术特别适于在国产普通环锭细纱机上加装。在紧密纺纱技术的专利申请中,大部分国内研发厂商也是针对c型或其改进结构进行专利申请。
表2所列国外纺机厂研发的四种紧密纺纱设备或装置,都能获得较好的凝聚和纺纱效果,但在投资成本、运行成本、凝聚效能、品质影响、运行稳定性、维护特性和对原机牵伸的影响等方面各有侧重,这对于设备研发制造厂和使用企业来说有必要进行全面了解。
值得注意的是,当C或D型结构被加装或改装到国产环锭细纱机上时,必须要考虑到其对原有牵伸系统的影响,如前罗拉驱动凝聚部分较大的传动负荷对原机前罗拉扭矩增量和运行稳定性的影响、阻捻胶辊加压对牵伸部分加压的影响、前胶辊传动阻捻胶辊及网格圈所需摩擦驱动力对前胶辊运行稳定性的影响等。必须认识到在国产环锭细纱机上加装或改装与国外厂商在原装机或成套牵伸部件改装存在很大的区别。不适当的加装结构设计有可能造成运行稳定性差和纱线品质的下降。
4.2国产化创新提示
紧密纺纱设备的国产化创新是紧密纱纺纱技术在国内普及的关键一环,其能大幅度降低投资门槛和设备运行费用,使紧密纱的生产成本控制在一个合理的范围内。这样不但高档纱线可以用上紧密纺纱技术,而且一般中档的纱线产品也可以采用紧密纺纱技术。
结合我国国情和细纱机机型现状,创新出一种能附加在应用面较广的FA506型、FA507型等细纱机上的紧密纺纱技术是发展和普及的方向,必须达到制造和运行成本低、凝聚效果好、性能稳定可靠、对原机牵伸影响小和运转操作方便等要求。
在绪森公司提出的6个比较项目的基础上,笔者又附加拟定了7个比较项目,并将表2的四种紧密纺纱设备或装置形式列入比较,见表3。

紧密纺纱技术的国产化研发思路可以参考表3中13个比较项目予以完善,尽量满足多个比较项目的要求,优化运行性能。
5 结束语
紧密纺纱技术是传统环锭纺纱技术的发展和进步,与所有新技术的推广应用一样,紧密纺纱技术的应用也需要一定的时间和过程,需要业界为其发展创造条件。纵观纺织业不平坦的发展历程,可以这样说:生产规模的发展是有限度的,而产品品质的改善是无止境的。