山羊绒是名贵的纺织原料,我国有资源优势,且品质较好。羊绒产品如羊绒衫、羊绒大衣呢等均受到国内外消费者的喜爱。但其纺纱方法主要限于粗梳毛纺系统,在精纺领域较为少见。我们利用国产毛、棉设备结合,在机器和工艺技术上做了研究和改进,纺制出了条干均匀毛羽较少的羊绒纱,可以用于机织和针织。
2羊绒的纤维性质
羊绒性质与羊毛类似,但长度较短,其长度与棉纤维接近。经多次试纺表明,平均长度24mm以上的羊绒可以在棉纺设备上正常纺纱。
和棉纤维相比,羊绒纤维具有长度差异大、表面光滑、抱合力小、比重小、有不规则卷曲及静电现象严重等特性。羊绒纤维平均长度接近棉纤维,但整齐度差,平均直径在13.4~16.5μm,不匀率15%左右,断面接近圆形,纤维表面鳞片数平均100μm6~7个,鳞片呈倾斜覆盖,紧贴毛干,边缘整齐,无顺逆向不一致感觉,手感滑糯,具有所谓“羊绒感”。羊绒比重为1.27g/cm3,比较蓬松,保暖性能好,羊绒单纤维强度较低,所以梳理时要防止对羊绒的损伤。羊绒的不规则卷曲比羊毛要少的多,约3~4个/cm。另外,羊绒属高电阻动物纤维,摩擦后极易产生静电,所以羊绒纺纱时,各道工序速度宜小掌握,但同时羊绒与羊毛回潮率相同,吸湿速度比羊毛快,吸湿后静电现象改善。
本次采用的羊绒原料为优级白无毛绒,直径为15.1μm,平均长度38mm,断裂强度1.40cN/dtex,伸长率40%,静电摩擦效应19.36%。
3 羊绒纺纱
3.1羊绒的加油给湿预处理
山羊绒和羊毛一样必须借助油剂,使表面状态起变化,才能纺纱。油剂可改善羊绒纤维间和羊绒与机件之间的摩擦性能,消除静电,增加纤维的集束性。但上油给水要适宜,过多则绒网下沉,易缠针布并造成针布生锈;不足则不能达到充分梳理,纤维损伤大,落绒多。因此,在加油给湿之前必须测试出原有的羊绒含油率和回潮率,再根据要求的羊绒含油率和回潮率,采用不同的油水比加于羊绒中,要求羊绒的上油率达到1.5%左右,回潮率20%以上,加油给湿要注意其均匀性,加油加湿后的羊绒要用薄膜盖好,存放24小时后再使用,使乳化油剂的微小颗粒及水分,均匀扩散于纤维表面。
3.2羊绒纤维的混合
羊绒纺纱多为散纤维染色的混色纺纱,且混纺产品较多,后道工序缩绒要求绒面起绒均匀。由于在和毛机上和毛的次数较多,混合作用充分,梳毛机上的梳理是纤维处于自由状态下的转移与梳理,混合作用也比较充分,这是棉纺的混合梳理设备所难以达到的,用混条来补充也难以达到,因此纤维混合阶段采用毛纺设备。
3.3工艺流程(以机器型号表示)
羊绒(加油给湿)-毛纺和毛机(B261)-毛精纺梳毛机(B272,条筒)-A272F-A272F-A272F-A454E-FA502-1332D-并捻(后加工)
3.4各工序主要工艺参数及技术措施
3.4.1 和毛加油
混料成分应达到均匀一致。在和毛机上要定时定量地喂毛,并要均匀地铺放在喂毛帘上;为了减少纤维的损伤,混料要有适当的开松度,在和毛机上加工羊绒时,应采用较小的锡林速度,适当放大隔距和减少工作辊对数,以减少纤维损伤;加油设备要油压稳定,喷油应成雾状,以保证混料的加油均匀;另外,还必须根据原料不同和车问温湿度的变化,严格掌握加油量及加油后的回潮率,以利于梳理工作顺利进行。
3.4.2精纺梳毛
梳毛机的工艺是否合理,对发挥梳毛机的梳理作用和提高梳毛机的产质量,都具有十分密切的关系。因羊绒纤维细而短,所以梳毛机应采用较小的隔距,以加强梳理作用,并能达到降低毛粒含量的目的。B272型梳毛机上六只工作辊的隔距,应与混料的松解程度相适应,其隔距一般为靠后的几个相差较大,越向前差距逐渐减小。锡林与道夫之间的隔距,应小于最前一只工作辊与锡林之间的隔距,以利于充分梳理纤维,并可促使更多的纤维由锡林向道夫转移。在同一锡林上可以采用统一大小(取O.42mm);毛刷与前后滚筒之间为剥取和被剥取作用,取0.13mm;斩刀和道夫之间的隔距取0.3mm;毛条定量为15g/m。
对毛条的质量要求主要有:首先,毛网要清晰,纤维分布均匀,没有破洞和云斑,要尽量减少纤维在长度上的损伤;其次,对毛网上的毛粒有一定限制,每克中的毛粒数要求不超过28只;毛条重量不匀4%左右,萨氏条干不匀率20%以内。
3.4.3并条
并条工序采用“二大二小”顺牵伸工艺原则。提高纤维的伸直度和平行度,适当放大隔距,加重压力,提高牵伸质量。头并采用6根喂入并合,二并和三并采用8根喂入并合,加强牵伸元件检查,提高熟条质量,熟条萨氏条干控制在15%以内,重量不匀率小于0.9%,具体工艺配置见表1。
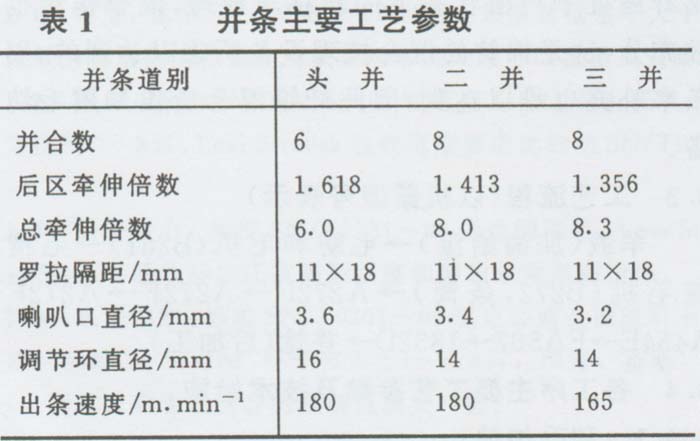
3.4.4粗纱
粗纱采用“重加压、小张力牵伸、较大粗纱捻系数”的工艺原则。由于羊绒抱合力较差,故宜采用小张力牵伸,适当加大粗纱捻系数,防止意外伸长,适当加重罗拉压力,尽可能拉断部分超长纤维,防止出硬头,确保牵伸质量。主要工艺:粗纱定量4.3g/10m,捻系数68,前罗拉速度180r/min,罗拉口隔距块6.0mm。
3.4.5 细纱
细纱采用“重加压、较大后区牵伸、适当罗拉隔距”的工艺原则。首先应选用合适的钢丝圈型号;其次,因粗纱捻度较大,为顺利退捻,后区牵伸隔距应略大;第三,选用适当的钳口隔距(建议选用3.0mm的钳口隔距块),摇架加压为18daN/双锭×12daN/双锭×14daN/双锭,钳口隔距不适当,加压不足易出硬头;第四,选用不处理软弹性胶辊,增加对纤维的握持力,以改善成纱条干。
3.4.6 后加工
在络筒方面应保持常规做法,羊绒衫对纱的要求是无结头或少结头纱,减少纱疵及粗细节。在络筒机上使用电子清纱器去除部分纱疵。
另外,为了保持纱线张力均匀采用单独并纱,而且并纱根数不限于2根,如果采用倍捻机1次捻筒不仅成形好,而且可以减少纱线结头。
4成纱质量
经以上改进,实际生产过程比较顺利,所得羊绒手感柔中有挺,弹性好,纱线强度高,其纱线物理指标见表2。
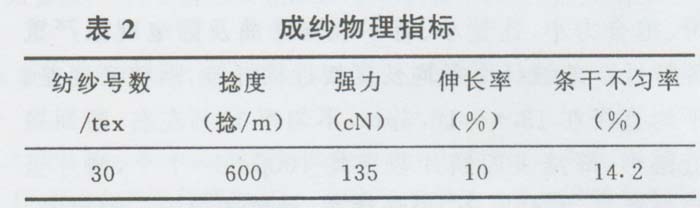
5 结语
5.1 改变传统的粗梳毛纺工艺,选用国产毛、棉纺有关设备,组成毛、棉设备混合羊绒纺纱生产线,有利于降低设备投资和生产成本,从根本上降低纺纱生产费用。
5.2各工序选用合适的纺纱专用器材,加之与合理的工艺相配置,才能确保成纱条干质量,以满足羊绒制品的服用性能。
5.3在正常羊绒纺纱过程中,车间湿度应偏大控制为宜,前纺80%,后纺75%。