一、纺纱技术的进步
1.现代纺纱普遍高速化。新型精梳机速度均在300钳次/分以上,如经纬股份榆次分公司 的JwTl268A精梳机,358钳次/分;马佐里(东台)纺机有限公司的CM500型,400钳次份;瑞士立达的E62型,350-400钳次/分。并条工艺输出速度在800-1000 m/min,如宝成纺机公司的FA382型,800 m/min;河北太行的FA398型900 m/min;马佐里(东台)公司的UNIMAX(R)型1000 m/mino粗纱机锭翼纺纱速度在1400-1500 r/min,如天津宏大纺机的JwF1418型1500r/min;无锡宏源公司1400 r/min;马佐里(东台)公司的FTID型1200 r/min ,细纱机锭速已达20000-25000 r/min,如上海二纺机的EJMl38JL型22000r/min;经纬股份榆次公司的F1520型25000 r/min;泰坦股份的TFA506型20000 r/min,而在2000年前国内基本不能生产如此高速的。
2.智能化在线检测已是现代纺机的趋势。现代纺机的高速化,人工控制已是力不从心,因此现代纺机上运用了光、电、机、气动、液压等方面新技术,采用高性能工业控制器,进行逻辑控制。对生产过程中的各种工艺参数、运行状态的在线检测、显示、自动控制、自动调节,以保证生产的正常运转和产品质量稳定。采用智能化在线质量控制技术已成为现代纺机的发展趋势。如FA382型并条机采用在线检测输出条的波谱图和粗节图,喂入、输出条的支数图,对匀整工作点自动校正,新型的粗纱机普遍采用计算机控制系统,结合在线检测和其它机电一体新技术组成高精度的随动控制系统,使张力控制,防细节伸长率等难题易于解决。
3.新型纺纱技术不断发展。传统的环锭纺纱在世界上仍占最主要的地位,而新型纺纱技术层出不穷,不断发展,如转杯纺、蜗流喷气纺、摩擦纺等。近几年紧密纺发展迅速,紧密纺纱3mm以上的毛羽减少80%,2mm毛羽减少50%,飞花减少85%,断头减少60%,纺纱质量大大提高,而且在后道可以节约浆料,减少织机停台率,提高针织效率。因而受到纺织企业的青睐。国外多种型号紧密纺装置各有技术特点,但基本原理均采用负压气流来控制纤维、凝聚纤维的,紧密纺装置中都有一个中空表面布满小孔的集聚罗拉,在集聚罗拉上有的用孔密度3000孔/cm2的网格圈;有的用多孔的胶圈;有的不用任何圈,在集聚罗拉上均有一个夹持胶辊或上压辊,采用紧密纺装置后都没有了清洁辊。瑞士立达的com4紧密纺机的中皮圈后无横动。
4.新型纺纱专件和辅助不断涌现。例如气动加压和板簧加压替代弹簧加压,使牵伸加压更稳定;用碳纤尼龙制成的弹性上销,具有对胶圈张力自动调节作用,稳定胶圈的运转和对纤维的控制力,可替代金属上销;用硬质橡胶或工程制成的中胶辊,替代中铁辊,既可消除中铁辊生锈问题,又使中罗拉钳口有更好的弹性握持力;高精度罗拉,表面硬度高,表面镀铬光滑无毛刺,经向跳动小于0.03mm,同心度好,抗弯强度高,无波率达98%,波波幅最大的不超过5mm等,新型的磨胶辊机如瑞士胡伯+森纳集团的贝克磨床,全自动控制,对胶辊的磨削量、磨砺次数、磨砺成品尺寸、表面粗糙度、紫外线照射处理等进行在线检测、自动调节。并且对磨砺前的胶辊外径进行自动检验、自动淘汰。
二、纺纱技术和管理的进步
1.纤维多品种化和纱线花样化。随着市场需要的多样化和纤维制造技术的创新,大量的新型纤维出现,如大豆蛋白纤维、牛奶蛋白纤维、竹纤维、彩色棉、各类聚脂纤维、各种异型纤维以及纳米纤维等等,纺纱不再仅仅是传统的棉、毛、麻、丝、涤等纤维的单纺和二种纤维混纺,而是新型纤维和传统纤维混纺,二种以上纤维混纺。纱线的品种也不仅仅是普梳、精梳还有竹节纱、彩色纱、花式纱、包芯纱等等,促进了纺纱技术的进步。
2.质量考核水平不断提升。纱线质量对布匹质量直至面料质量有着重大影响作用,随着现代纺织面料质量要求的提高,对纺线质量要求也水涨船高。瑞士蔡尔维格乌斯特公司从世界各地采样测试,整理统计值,每隔几年发布乌斯特公报已近五十年,在全世界的纺纱生产和贸易中已被广泛使用,不同期的乌斯特公报反映了纱线质量的提升。
一是纱线质量指标内容的增加。
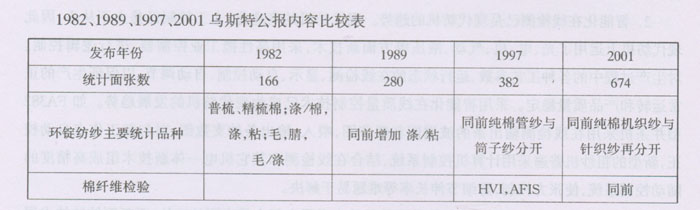
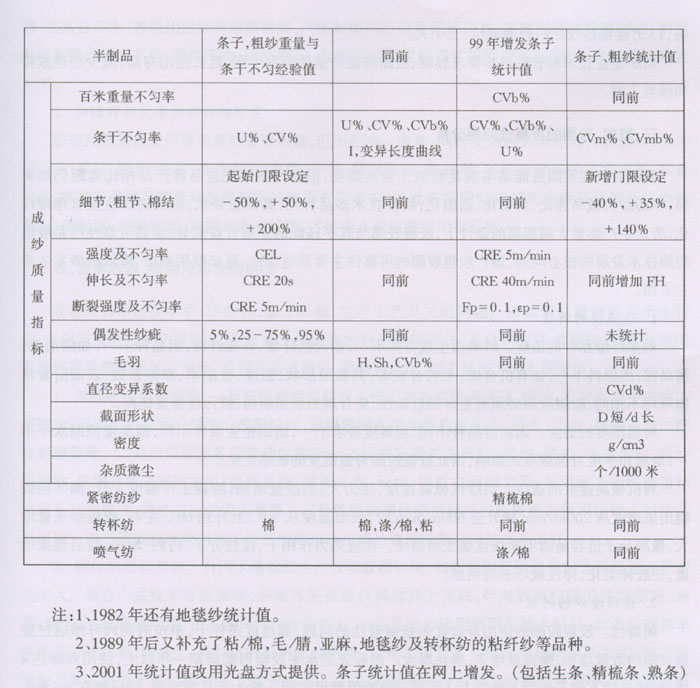
二是具体质量指标如CV%、CVb%、千米细节、千米粗结、千米棉结、重量Cv%,以及断裂强度等经度指标均有明显提高,特别是针织用纱的断裂强度指标,可以说2001出报的95%水平不比97出报的5%水平差。
三是纺织企业的右些客户的特殊质量要求,为对某些纱品种的细节,粗节要考核万米,十万米,而不是千米等。
3.科学管理和劳动生产率提高。纺织企业从上世纪九十年代压锭减员后,提高劳动生产率的途径发生质的变化,从简单的减员挖潜逐步走向采用高新技术,大量使用自动化高速,运用计算机网络管理,革新工艺,改革管理制度,使万锭用工量不断下降,劳动生产率节节上升。以无锡一棉为例:该厂多年来坚持用高新技术进行技术改造,设备自动化程度极大提高,全厂运用计算机联网管理,实现无纸化、信息化、网络化,实施全员学习考核制度,员工素质不断提升。现在万锭用工不足50人,先进车间已达35人,1个女工看30台细纱机,胶辊间全套引进瑞士贝克智能化设备,13万锭细纱仅用一台磨辊机、二个人。
纺织企业技术和管理进步要求胶辊、胶圈降低质量故障发生率,延长使用寿命,减少处理故障和保养工时。
三、胶辊、胶圈的可靠性问题分析
我国的胶辊胶圈虽能基本满足纺织工业的需要,但是与国际先进品牌产品相比差距仍然明显,在纺纱高速化、自动化、新型化,纺纱技术多品种化,高质量要求,以及纺织企业管理现代化,劳动生产率要大幅提高的条件下,胶辊胶圈与其不匹配的矛盾日益突显,提高可靠性已是胶辊胶圈技术发展的核心问题,国产胶辊胶圈的可靠性主要是适应性、延长使用寿命、降低故障发生率三方面。
1.适应性的问题
对多纤维品种的适应。纤维因生成方式不一,如天然纤维、合成纤维;因品种不一,如陆地棉、海岛棉;因原料不一,如有机合成、无机合成等,其截面形状、强度、吸潮率、摩擦系数、表面附着油脂等均不相同,胶辊胶圈必须有更好的抗油性,更合理的表面结构,抗污性能要提高。
对温湿度的适应。因纺纱品种不同,温湿度要求不一;纺织企业条件不同,温湿度控制水平不一;地域和季度对温湿度的影响,因此胶辊胶圈对温湿度的敏感度要小。
对高速度的适应。纺纱高速度,压力大,磨擦量增加,胶辊工作温度上升,如并条胶辊出条速度从200m/min提升至600m/min时,表面温度从30℃上升到60℃左右,胶辊形变量增大,橡胶分子链容易因不断快速蠕变而僵硬。在应热力作用下,橡胶分子“内耗”增加,滞后现象增重,使胶体老化,弹性破坏表现明显。
2.使用寿命的问题
耐磨性。胶辊胶圈的使用寿命首先是耐磨性的问题,高速度条件下,单位时间内纤维通过胶辊胶圈的数量增加,摩擦量增多,磨耗增大。国际先进水平胶辊回磨周期一年以上,使用寿命达4年,胶圈连续不停车使用2年以上。而国产胶辊因磨损中凹一般4个月需回磨,较好的在6-8个月回磨,最好的10个月回磨。胶圈3个月则要清洗,中凹损伤率较大,一般3个周期即9个月就淘汰了。
使用性能稳定。胶辊胶圈随着使用时间延长,其使用性能必然会衰退,可纺性下降,要延长使用寿命必须使性能衰退缓慢,据纺织企业的实践和试验,国产不处理胶辊在连续纺纱6个月后,条干CV%明显上升,而进口胶辊在8个月后才有所上升。
3.降低故障发生率的问题
胶辊胶圈在使用中发生最主要的故障是波、绕花、断头,除去纺织企业里、相关部件及管理问题,胶辊胶圈引发故障的根本原因是制造技术和制造质量。胶辊胶圈生产企业必须在配方和工艺设计上加大力度研究,采用高新材料,解决好抗绕性、抗污性、抗油性、温湿度敏感性、耐热性、耐磨性、使用性能稳定性等问题。胶辊胶圈行业是劳动密集型产业,工序有数十道,主要是人工操作,不稳定因素多而影响质量稳定,因此必须大力研发自动化专用设备,采用高新技术改造,提高自动化、智能化控制和监测程度,严格贯彻执行质量保证体系,实施现代化管理制度,消除胶辊胶圈的硬度不均、弹性不均、回性期长、气泡、杂质、脱层等常发性质量问题,从而降低故障发生率。
4.加强对相关牵伸部件的研究
胶辊胶圈是稳定纺纱质量的重要因素,但不是唯一因素,同时受到相关牵伸部件的制约,如加压元件、罗拉、轴承、铁芯、传动齿轮、上销、下销、横动装置、集棉器、吸棉装置等的技术水平,质量状况,维护保养情况都会对胶辊胶圈的使用产生影响,因此必须同时对相关牵伸部件进行科学选择,合理配置,加强管理,发挥其组合优势,才能提高胶辊胶圈的可靠性。
四、提高胶辊、胶圈可靠性的途径
在橡胶品制造技术中,原材料、加工、生产工艺是关键问题。而胶辊胶圈制造是个小行业,虽然涉及的技术学科较多,但没有专门研究的科研院校单位,基础研究非常薄弱,从行业现况看要提高胶辊胶圈的可靠性,必须在基础研究、原材料选用、加工方面有所突破:
1.基础研究要有突破,一是胶辊胶圈在纺纱工作中的运动机理研究,例如:胶辊运动中弹性恢复机理;运动中的胶圈对纤维的控制机理;胶辊胶圈在牵伸握持时压力、硬度、弹性、摩擦系数的配合机理等等。二是胶辊胶圈各项物理性能指标之间的定量关系研究,例如:硬度、冲击弹性、弹性回复性、压缩变形之间的关系;磨耗系数、摩擦系数、硬度、弹性之间的关系;各项耐老化性能指标之间及其和硬度、弹性指标的关系等等。三是各项物理性能指标与胶辊胶圈的使用性能之间的关系研究。四是胶辊胶圈胶料加工工艺性能指标与成品物理性能之间的关系研究。
2.原材料要有突破。自用丁晴橡胶生产胶辊胶圈以来,我国胶辊胶圈的材料选择总体水平变化不大。要在产品技术有所突破,必须首先在原材料选择上突破,针对胶辊胶圈的性能稳定、耐磨、耐老化、抗缠绕问题,在主体材料和配合剂上,一是要大力选用新型高技术材料,如含有羧基单体的高分子材料;精细化、颗粒化的粉状配合剂等,二是主体材料和配合剂提倡多元并用,如丁腈橡胶与其它高分子材料的并用;防护剂的多元并用;补强剂与分散加工的并用等,来改善胶料的加工性能,提高胶料的物理性。三是重视研究采用新型材料的加工工艺,改革原有工艺,以充分发挥新型材料的作用。
3.加工要有突破。我国胶辊胶圈制造用设备,非标的多,专业化的少,手工操作多,自动控制极少。胶辊胶圈制造操作工序多,上的问题是最主要的因素,手工操作工序越多,制造质量问题发生机率就越大。要解决胶辊胶圈可靠性问题,加工必须要有突破。橡胶的加工制炼、压出成型、硫化应采用数控自动化设备,和在线制造质量监控;尤其是胶辊胶圈的后加工工序的设备,重点是要合并工序,简化作业流程,提高自动化和在线监控的程度,不断提高加工的自动化、数控化、智能化,从而达到减少手工作业质量故障,提高产品质量可靠性,稳定性,提高劳动生产效率的目的。
4.严格而真实地实施IS09001质量体系管理。IS09001是严谨的科学的质量管理体系,这是市场经济中企业生存和发展的内在基本要素,绝不是企业产品宣传推销的手段,必须严格而真实地实施。质量体系中的所有质量要素,必须能得到科学的在线即时控制;每只产品的制造流程必须能达到可逆的全程参数检索;产品制成率不能仅仅满足于百分级、千分级的测定,必须努力向百万分级测定发展等等,只有这样才能促使产品质量稳定提升。
五、结束语
胶辊胶圈的可靠性问题,已是胶辊胶圈技术发展、胶辊胶圈行业为纺织更好服务的瓶颈。胶辊胶圈的技术问题和质量问题,必须放到纺织技术进步,纺纱技术进步,纺织企业管理进步的大环境中去思考和探索,走出具有中国特色、行业特色的技术发展道路,为建设纺织橡胶器材强国作出贡献。