1.0 1998年以前我司生产精梳纯棉纱存在的主要问题
1.1因当时我公司设备全部为80年代国产设备,无自调匀整装置,故一直按传统的精梳后二道并条的工艺流程生产,不敢采用国内外已较普遍的精梳后单并工艺路线。
1.2生产工艺技术及管理措施也沿用普通品种的做法,无法克服精梳棉条烂、毛、抱合力差的弊病,生产出的精梳纯棉纱表面毛羽多、条干均匀度欠佳、锭差大,与市场上同类品种相比不仅无优势甚至更差,客户不喜欢用,无法形成稳定的批量生产能力,更不可能象我司其他品种一样以高于别厂同类纱的价格销售。
2.0工艺设备优选试验
为了不断提升精梳纯棉纱的质量水平,自1998年以来我公司多次组织技术质量人员进行质量策划,针对精梳后的并合道数、粗纱定量、细纱罗拉隔距、清钢联、高效能精梳机、带自调匀整并条机、FA506细纱机等不同工艺条件、不同设备性能进行反复对比试验,以确定最佳生产工艺参数、工艺路线及设备配置。各项试验方案及结果见表1~表6。
2.1精梳后一道并与二道并的工艺试验(见表一)
(1)试纺过程中我们发现,精梳后一道并合的条子较光洁、较有抱合力,在粗纱导条辊上不易被拉断。
(2)从表1可看出,三种工艺条件下纺制的CJ18.2 tex纱相比,精梳后采用一道并合、粗纱定量4.6g/10m时条干CV%、细节、棉结均好于其他二种。尤其是经过络筒后,细节指标差异更加明显,精梳后一道并合的细节比精梳后二道并合少36%,与管纱的细节相比,前者增加1.25倍,后者增加1.8倍。从黑板条干看,一道并合的条干清晰、毛羽短而少,二道并合的板面模糊、毛羽长而多。从纱的表面结构看,筒子纱增加的细节是由于络筒通道刮毛引起。由此我们得到结论一:精梳后一道并合的筒子纱毛羽、细节等质量指标明显好于精梳后二道并的筒子纱。
(3)从表1还可以看出,不同粗纱定量(4.3g/10m与4.6g/10m)纺制CJ18.2 tex纱时,定量重的重量不匀率低,对CJ14.2 tex纱影响不明显。结合我司以往降低成纱重量不匀率试验的经验,我们得到结论二:同种粗纱用于纺制CJ14.6 tex、CJ18.2 tex纱时,粗纱定量宜选择4.6g/10m左右。
(4)从表1不同细纱罗拉隔距的试验结果看,后区隔距比以往使用的放大2mm,没有对各项质量指标产生不良影响,而重量不匀率却能达到较好的水平。而放大细纱后区隔距,能为粗纱大捻度、细纱后区张力牵伸小的针织纱工艺配置创造条件。由此我们得到结论三:实施粗纱大捻度、细纱后区大隔距、细纱后区小牵伸的工艺配置,能充分发挥前区胶圈握持牵伸的优势及减小后区牵伸力,提高成纱的条干水平。
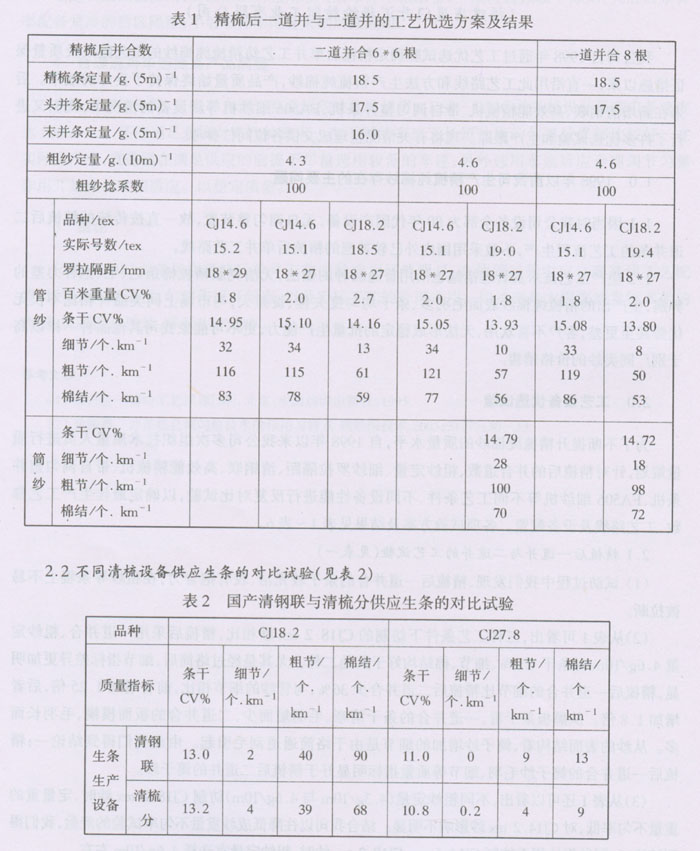
从表2可以看出,清钢联生条供应比清梳分生条供应所纺CJ18.2 tex、CJ27.8tex纱,成纱千米棉结增加30%多,千米细节减少50%多。
2.3不同精梳机供应的对比试验(见表3)
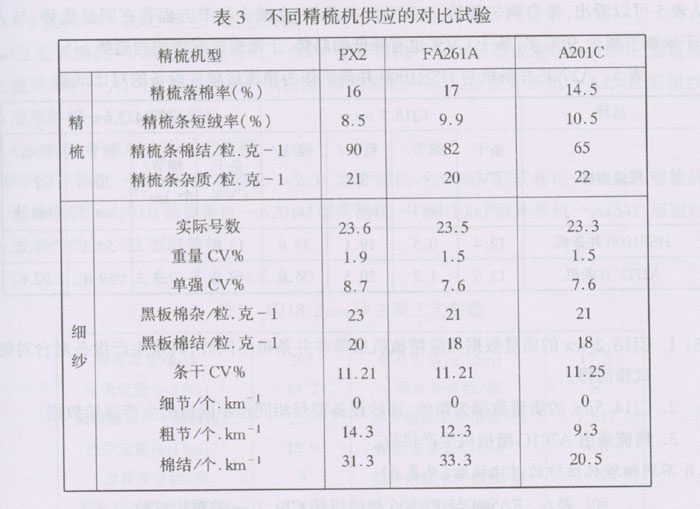
从表3可以看出,PX2、FA26lA高效能精梳机与A201C精梳机相比,所纺成纱的千米棉结增加50%多,千米粗节增加30%多,精梳条棉结增加30%多。
2.4不同清梳、精梳设备配套纺CJ18.2 tex的质量对比
在表2、表3试验的基础上,我们又跟踪了清梳分供A201C精梳机与清钢联供FA261A精梳机的纺纱生产质量情况(见表4)

从表4结果看,清钢联供FA261A精梳机配套生产的CJ18.2 tex与清梳分供A201C精梳机配套相比,其成纱的千米棉结增加86%,千米粗节增加27%,千米细节减少22%,条干CV%稍好。
从表2、表3、表4的试验或生产结果,我们得到以下结论。结论四:清钢联设备由于其自调匀整及多仓混棉的作用,在减少成纱细节方面存在明显优势,但由于高速带来了生条短绒、生条棉结的增加,从而使成纱棉结大量增加。结论五:PX2、FA261A等高效能精梳机在提高产量方面确实跃进了一大步,比A201C增加60%以上的产量,但由于其高速及国内机配件质量、加工精度的有限,不可避免的带来了一些负面作用,精梳条棉结、成纱千米棉结、成纱千米粗节均大幅度地增加。结论六:国产清钢联与国产高效能精梳机组合生产时,其成纱各项指标成叠加趋势,与普通清梳分设备与A201C的组合生产相比,千米棉结增加了80%多,千米细节的优势却被弱化。我们认为这种设备组合不宜用于生产32S以上中高支精梳纯棉纱。-
2.5不同并条机当精梳后单并设备的对比试验(见表5)
从表5可以看出,带自调匀整的HSR1000并条机,在减少细节方面存在明显优势,与A272F、相比,千米细节减少50%多,条干CV%也有降低的趋势,千米棉结有增加的趋势。
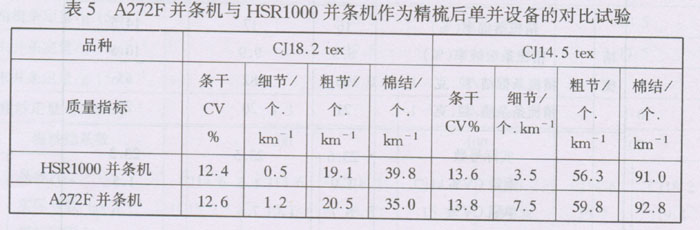
2.6不同细纱机纺纱的对比试验(见表6)

备注:上表数据为细绒棉、精梳后A272F单并工艺生产
从表6可以看出,相同粗纱在FA506细纱机纺比在FA504细纱机纺C39.7tex,存在显著优势,条干CV%降低1个百分点,千米细节减少56%,千米粗节减少37%,千米棉结减少17%。尤其是从生产现场看,细纱断头得到明显好转,管纱毛羽得到明显改善。经分析,我们认为产生这种结果的主要原因是,我司FA504.细纱机使用年限已较久,设备整体质量及一致性较差,难以胜任纺CJ9.7tex这样的高支纱。这个试验同时也表明,国产新一代的FA506细纱机其纺纱质量提高了一个档次,不作任何特殊改进、改造,就能用细绒棉正常生产CJ9.7 tex、CJ8.3tex等高支纱。
3.0生产工艺技术
3.1生产工艺流程
在上述生产试验的基础上,我司结合公司不同时期的设备配置,及时调整与精梳后单并工艺配套的设备组合,不断优化和提高纺精梳纯棉32S以上中高支纱的产品质量。
3.1.1 1998年-2000年生产工艺流程
A002型抓棉机-A006B型混棉机-A034型开棉机-A076E型成卷机-A186F、型梳棉机-A272F型并条机-A191B型条卷机-A201C型精梳机-A272F型并条机-A454E型粗纱机-FA504型细纱机-1332型络筒机
3.1.2 2000年-2002年生产工艺流程
A002型抓棉机-A006B型混棉机-A034型开棉机-A076E型成卷机-A186F型梳棉机-FA311型并条机-A19lB型条卷机-A201C型精梳机-A272F型并条机-A454E型粗纱机-FA506型细纱机-1332型络筒机
3.1.3 2003年以后生产工艺流程
A002型抓棉机-A006B型混棉机-A034型开棉机-A076E型成卷机-A186F型梳棉机-FA311型并条机-A191B型卷条机-A20lC型精梳机-ISR1000型并条机-A4.54E型粗纱机-FA506型细纱机-1332型络筒机
3.2 C118.2tex纱主要工艺参数(见表7)
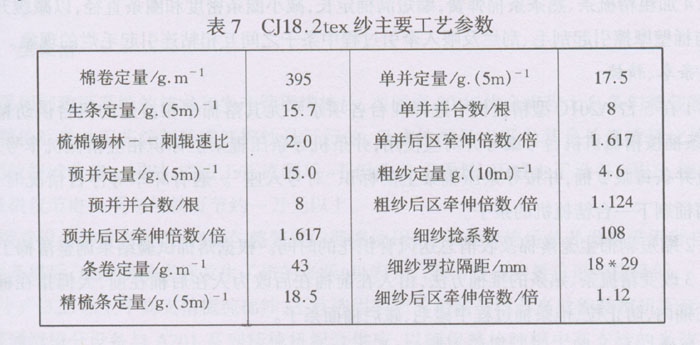
4.0质量保证措施
4.1开清棉
根据同盘棉包盘中生产的棉卷重量不匀率一般较稳定的特点,将同盘棉包生产的棉卷分成两种,盘中生产的供纺精梳纯棉,盘顶盘底或人为调节过供棉量生产的棉卷供纺精梳涤棉混纺纱。单程安装自调匀整装置后,基本上不需采取此项措施。
4.2梳棉
选择针布状态完好、后车肚及斩刀落棉率相近的梳棉机供纺精梳纯棉纱,并根据落棉试验结果动态调整各机的落棉率。为克服机台间客观存在的差异,对预并施行对眼定台搭配供应,具体做法为:生条桶按梳棉机机台号编号并对应使用,预并条机导条辊上标识相应梳棉机车号,每台梳棉机供应预并每眼二桶并按导条压辊架上的标识“对号入座”。遇有坏车等停台情况时,二眼同时更换二桶候补梳棉机的条子。
4.3预并、精梳后单并
4.3.1左右两个牵伸区的同档胶辊使用同档直径,并使两眼的加压一致,以达到较为统一的牵伸效果,减小眼差,并要求交接班时进行检查,以防操作过程中被调换。
4.3.2合理配置导条罗拉一给棉罗拉、给棉罗拉一后罗拉、集速罗拉一圈条压辊间的张力牵伸,减小意外牵伸,使牵伸差异率控制在1%以下。上机时,逐道反复试验比较,确定了比较合理的张力牵伸配置工艺(见表8).
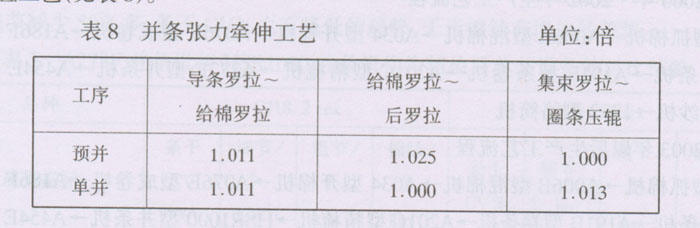
4.3.3选用生漆胶辊或已使用过的RC型胶辊,减缓胶辊吸花现象。
4.3.4加粗精梳条、熟条条桶弹簧,缩短满桶定长,减小圈条密度和圈条直径,以减缓升降过程中条子与桶壁摩擦引起刮毛、刮烂及喂入牵引过程中条子之间互相粘连引起毛烂的现象。
4.4条卷、精梳
4.4.1在5台A201C型精梳机中选择4台各项水平尤其落棉率相接近的机台供纺精梳纯棉纱,精梳条桶按精梳机机台号编号并对应使用,并条机导条压辊架上标识相应精梳机车号,每台精梳机供应并条每眼2桶,并按导条压辊架上的标识“对号入座”。遇有坏车等停台情况时,两眼同时更换两桶剩下一台精梳机的条子。
4.4.2缩短剥棉尘笼落棉及收清总送风管积花的时间。根据落棉试验结果调整落棉工艺。
4.4.3改变精梳条、熟条的推桶方法,由人在前桶在后改为人在后桶在前,大拇指在桶外改为大拇指在桶内,防止拉、推条桶过程中碰毛、碰烂桶面条子。
4.5粗纱
合理配置导条辊间的速比及速度,使喂人条平缓松弛地进入后罗拉,减小导条区的意外牵伸。优选卷绕工艺,减小大、中、小纱间的伸长率差异,使伸长率差异控制在±1%以内。前胶辊使用同档直径的生漆胶辊,逐锭调节统一摇架加压,减小锭与锭之间条干、牵伸效率的差异。选用光洁的锭翼,防止刮毛刮烂纱条。减小上条高度,上条高度由普通品种的30cm一40。m改为上10层以下,以避免取条时碰毛条子。
4.6细纱
逐锭调节统一摇架加压,减小锭与锭之间条干、牵伸效率的差异。消除歪锭子、歪导纱钩、歪隔纱板等通道不正现象;合理配置钢丝圈重量,使气圈上不碰筒管头、下不碰隔纱板,防止成形卷绕过程中纱被刮毛、碰毛。前胶辊使用不处理软胶辊,后区采用张力牵伸,以提高成纱的整体条干水平。配置较低的锭速及罗拉速度,减缓毛羽的产生。
除采取上述措施以外,各工序安排素质好、责任心强的挡车工负责挡车。积极开展防疵捉疵工作,真正做到不合格的产品不流入下道工序,下道工序为上道工序把关。增加检验试验频率,及时发现和纠正重量异常情况,生条重量、精梳条重量、梳棉落棉、精梳落棉由每半月试验一次增加为每星期试验一次;熟条重量由每班试验三次增加为每班试验五次。制定内部质量控制指标,对直接影响重量不匀率的指标进行较为严格的控制,如各工序的牵伸差异率、落棉率、棉卷重量不匀率等均按加严的指标进行控制。
采取以上技术管理及设备措施后,收到了明显效果,自1998年以来,我司精梳纯棉系列品种在市场上形成了一定的优势,占有了一席之地,精梳设备能力也由原来的2套增加到了4套。现以CJ18.2 tex纱为例,其成纱主要质量指标见表9。
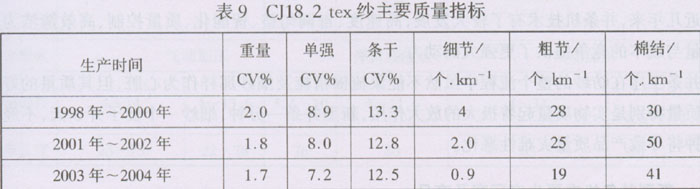
5.0结束语
(1)采用细致而系统的技术和生产管理措施后,在国产80年代全流程无自条匀整装置的设备上,使用精梳后单并工艺纺制精梳纯棉纱是可行的,且成纱质量水平尤其是外观质量比传统双并工艺得到较好的改善。同时,缩短工艺流程后,不但改善了质量,还减少了设备、用工、能耗,少用一道并条机仅节电一项每年就可节约一万元以上。
(2)随着设备的更新改造,自调匀整装置的普遍使用,尤其是精梳后单并设备采用带自调匀整装置的并条机后,成纱质量指标发生了质的飞跃(见表九),而对管理的要求可相应降低。
(3)生产32S以上中高支精梳纯棉纱,不宜选用国产清钢联与国产高效能精梳机配套供应,适宜选用普通清梳分设备与A201系列精梳机配套供应,以确保精梳纯棉中高支纱的光洁度、均匀性。
(补充说明:由于文中数据采集的时间较长,而工厂不同年份、不同时期所使用的原料、生产条件等存在较大程度的不同,文中同表所列数据间具有可比性(表九除外),不同表间的数据不具备完全可比性。)