纯苎麻产品因具有吸湿散热快、布身挺爽透气、抗菌防腐等特点,倍受消费者的青睐。近年来,苎麻产品越来越趋向高档化,纯苎麻大提花制成的床单、台布以及苎麻装饰布的需求量也越来越大。但纯苎麻产品生产难度较大,苎麻纱浆纱技术仍不够成熟。虽然近年来人们也在纯苎麻浆纱技术上进行过大量的探索,但对有关纯苎麻浆纱工艺路线、浆料配方等关键技术仍处于探索之中。为此,笔者结合某厂生产的28/28 275.5/220160纯苎麻布,就纯苎麻纱浆纱技术作些探讨,供广大同仁参考。
1 苎麻的上浆工艺要求
苎麻上浆的目的并不在于增强,而在于既要贴伏其长而硬的毛羽,又要设法使浆纱柔韧耐磨。若不充分将其毛羽贴伏,这些长毛羽在上机织造时,极易在停经片处造成大量的麻纤维堆积,尤其是靠近综丝前面两排停经片极易堆积麻纤维和其吸附的浆料而使纱线纠缠结团,导致织造时大量断头,布面吊经疵点严重。如果虽将其浆纱毛羽贴伏,但浆纱硬挺则极易造成停经片无法及时下落,而使断纱横在梭口间导致引纬运动不稳,因此既要充分贴伏毛羽,又要使浆纱柔韧耐磨是浆纱必须解决的关键问题。
2苎麻纱浆纱工艺路线的确定
2.1高浓度,中粘度
由于苎麻纱毛羽长而多、长而硬,没有足够的上浆率要充分贴伏这些长达几厘米的长毛羽是不可能的。要达到高的上浆率则必须采用浓度较高的浆液,同时纱体上的浆液要有足够大的粘附力来粘附已经在其身上的毛羽,使其在外力失去后不因纤维的刚性而重新抬起,要做到这一点就必须采用重加压的浆纱工艺。在重加压的工艺条件下,要实现高的上浆率,没有足够的浆液浓度是不行的,故浆液浓度一般宜选择在10%左右。为提高浆液的浸透性,浆液的粘度也必须适中。
2.2双浸浆。重浸透
由于苎麻本身不仅刚性大,而且纤维表面光滑,纤维之间抱合力差,1 cm以上的毛羽,受拉力时极易从纱身中将整根纤维拉出,因此必须有足够的浆液浸透将纤维固结起来,而要达到这一目的,在有较高浆液浓度的情况下,采用双浸双压的工艺配置,显然是必要的。曾用单浸、双浸进行过对比试验,采用单浸双压的工艺配置比采用双浸双压的工艺配置,其被覆要多些,浆纱干分绞时坏纱多,特别是坏边现象相对严重,织造时不仅断头率高,而且在停经片处也较易积聚苎麻纤维及其吸附的浆料。具体情况见表1。
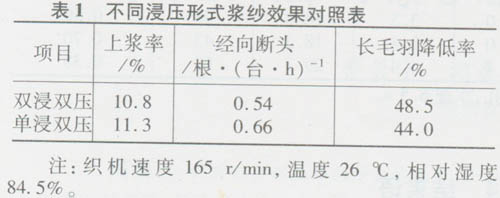
2.3重加压。贴伏毛羽
纯苎麻纱上浆时,必须采用重加压的工艺配置,因为苎麻纤维不仅粗,而且刚性也大,要在挤压区使毛羽粘附,必须有足够的压力才有利于毛羽贴向纱身,同时重加压能挤掉纱线中更多的水分,压浆力越大,在挤压区压去的水分就越多,出挤压区的经纱上的浆液浓度就越高,其粘附值就越大,其浆液粘附力就越大,越有利于吸牢已贴在纱身上的毛羽。因此,要贴伏浆纱毛羽,保证良好的浆纱效果,前后两个压浆辊均需采用较大的压力,特别是靠近烘房的后压浆辊压力不能小,采用双浸双压、重加压的工艺配置,其毛羽贴伏的效果和织造效果均要好于单浸双压、先重压后轻压的工艺配置。
2.4大张力,低回潮
由于苎麻纱纤维刚性大,上浆后刚性更大,如采用小张力工艺配置,理论上有利于减少苎麻纱的弹力损失,但实际上采用小张力不仅浆纱卷绕时无法将纱线卷紧,织轴卷绕密度很小,影响织造生产,而且在浆纱干分绞时,极易造成纱线断头。因此,笔者认为苎麻浆纱在湿区张力可偏大掌握,而卷绕张力必须要大。
众所周知,苎麻纤维的湿强要高于干强的20%~30%,从这个意义上讲,苎麻纱的烘出回潮率可大些。但烘出回潮率大,浆膜的撕裂强度就大,在采用PVA为主的混合浆料时,在上浆率较大的情况下,则干分绞时的坏纱现象严重,因此回潮率要偏小掌握,以控制在4%左右为宜。
2.5高上浆,后上油
生产28/28 275.5/220 160苎麻大提花布时,上浆率低于11.5%,浆纱长毛羽贴伏不够,容易出现停经片处麻纤维的堆积缠绕,而上浆率低于10.5%,则极易出现停经片处麻纤维缠绕起团,影响正常织造。
高上浆率只要浆料的配方得当,织布车问有较高的相对湿度(80%以上),即使上浆率达15%也能取得较好的织造效果。某厂实践也表明,上浆率达14.5%其织造效果要好于12%。个人认为既使产品的经纬密不够大,上浆率也宜偏高掌握。但必须明确指出的是上浆率达到12%~14%时,织布车间必须特别重视车间温湿度的管理,温度最好要保持在25℃以上,相对湿度控制在84%~88%之间。因此,采用以PVA为主的混合浆料时,上浆率宜控制在12%~14%之间,但高上浆必须有织布车间的高湿度(80%以上)来作保证,如空调条件不好,则上浆率宜适当降低,以控制在11%左右为好。
为了提高纯苎麻的耐磨性,采用后上油工艺十分必要。采用后上蜡与后上油工艺,同样能起到降低浆纱表面摩擦因数,提高浆纱的平滑性,降低织造断头的作用。但浆纱后上蜡存在印染退浆时蜡不易全部褪尽,极易出现染色不匀不易上色等问题。而后上油对后整理无不良影响,且上油量既使偏大,也不会造成因油在停经片处堆积而吸附纤维的现象。目前浆纱后上油技术已经成熟,其优越性也已在实践中得以显露,完全可以用“后上油”来取代后上蜡。用SA-100高效平滑剂(不需加热)和蜡、水按1:1:1混合加热,在十多个品种上进行大面积“后上油”推广试验,试验表明这种方法其织造效果较为理想。
3苎麻纱浆料的选配
从以上理论分析可以发现,要达到既贴伏浆纱毛羽,又要使浆纱耐磨耐屈曲的目的,不难得出苎麻浆纱的首选浆料应当为PVA,但从贴伏毛羽、保持弹性以及粘着性能上看,丙烯酸类浆料也是一种较为理想的选择。现将有代表性的配方及浆纱效果列表2、表3如下。


由表3可见,方案4浆纱效果最为理想。现将有关浆料的选用情况、浆纱效果和织造效果作一简要分析。
方案1PVA用量较低,_卜浆率小,虽上浆率达8%,浆纱较为柔软,干、湿分绞均较顺利,织轴卷绕密度也适中,浆纱手感也较为平滑,但浆纱长毛羽并没有多大降低,开口严重不清,织造断头率高,织造过程中停经片处堆积麻纤维缠绕起团现象十分严重。
方案2增加了PVA的用量,适当降低了CMS的用量,并用了25 kg性能优良、含固量30%的KD318取代20 kg甲酯,增加了1 kg甘油作吸湿剂用。由于完全醇解PVA内聚力高,干分绞时劈纱断头现象严重,不仅在卷绕时织轴难以卷紧,而且干分绞坏纱现象更为严重。由表3可见,浆纱上浆率有了明显的提高,浆纱长毛羽有了较大幅度的降低,但部分机台停经片处仍有少量的麻纤维积聚成团。
方案3为进一步贴伏浆纱毛羽,将KD318用量增加5 kg,新增用粘着力、成膜性较好的AD浆料10 kg,浆纱生产时虽然干分绞较为顺利,但由于丙烯酸类浆料具有吸湿再粘性,在织布车间相对湿度达到80%左右时,在织机停经片处较易粘附浆料,粘附麻纤维,其浆纱长毛羽贴伏,织造效果不及方案2。
方案4中PVA-1799用量较方案2降低了一半,增用了15 kg具有很强粘着性,而分子量、内聚力又相对较低的PVA-205MB(部分醇解PVA),同时也适度降低了KD318的用量,并且为了防止上浆率提高后浆纱脆硬,纺织润滑剂用量也增加了5 kg,同时甘油用量也增加了1 kg,取得了较为理想的浆纱效果。不仅浆纱时分绞顺利,而且浆纱上浆率、浆纱长毛羽贴伏率大大提高,杜绝了织造时停经片处积聚麻纤维的现象,而且浆纱手感润滑,织造断头率较低,.但必须指出此方案对织布车间的要求更高,如车间相对湿度偏低,则织造断头会大幅度上升。
4 结束语
(1)苎麻纱浆纱宜采用“高浓度,中粘度,双浸浆,重浸透,重加压,贴伏毛羽,大张力,低回潮,高上浆,后上油”的工艺路线,但采用这一工艺路线,织布车间相对湿度必须保证在80%以上,否则织造效果不够理想。
(2)纯苎麻浆纱配方应“以PVA为主,淀粉+DDF复合催化剂或变性淀粉及丙烯类浆料为辅”,但PVA-1799的用量不宜过高,否则分纱困难,上浆率也难以提高,宜选用分子量较低的PVA(如PVA-205MB)。
(3)新型丙烯酸类浆料如KD318、AD等浆料虽然粘着力、成膜性均好,但由于丙烯酸类浆料具有吸湿再粘性,而纯苎麻产品织造时相对湿度要控制在84%~88%最为适宜,因此丙烯酸类浆料用量不宜过高。
(4)在采用高上浆率的条件下,为了提高浆纱的柔韧性,其配方中的油剂用量宜高些,同时吸湿剂也宜多些。