一、FA326型并条机的主要技术参数:
l、眼数:2
2、速度:最高600米份
3、适纺纤维长度:22~76mm
4、喂人型式:高架顺向积极喂入
5、牵伸型式:三上三下压力棒加导向上罗拉曲线牵伸
6、总牵伸倍数:5.6~9.7倍
7、加压型式:摇架弹簧加压
8、罗拉直径/mm:上罗拉:34,34,30,34
下罗拉:45,35,35
9、换筒型式:后进前出链条推杆式
10、自调匀整型式:开环式自调匀整
二、FA326并条机的主要结构特点:
l、传动方式:大量采用齿形带传动,传动更加平稳,噪音低,牵伸系统采用圆弧齿形带传动,承
受载荷能力强,传动平稳无间隙,有利于提高牵伸质量。
2、主电机采用变频调速,调整方便,控制系统采用PLC控制,整机自动化程度高。
3、牵伸机构:采用三上三下压力棒加导向上罗拉曲线牵伸型式,棉网先经后区预牵伸,然后进入主牵伸区内,压力棒在主牵伸区内起加强控制慢速纤维的作用,从而有利于提高牵伸质量。
4、导条喂入采用高架式积极顺向喂人,车头眼、车尾眼分别由平皮带分别单独传动各导条罗拉,棉条经由导条罗拉积极喂入,借助分条器将棉条在导条罗拉上排列成行,导条部分装有三组光电自停检测头,这种导条结构操作方便,可有效地减少意外牵伸,不积飞花,有利于提高棉条质量。
5、自动换筒:单独电机带动链条推出满筒同时喂人空筒,大大降低了工人的劳动强度
6、吸风系统采用独立的吸棉箱,且位于主机外部中心线上,可以任意调节风量的大小,并且可使左右两眼的吸风效果一致,对减少纱疵等大有好处。
7、配备洛阳第六一三所生产的BY[)型短片段自调匀整装置,采用全部检测、全部匀整的方式,可有效地控制短片段不匀。
三、工艺配置:纺制JCl4.5
l、配棉情况

2、工艺流程
FA009自动抓棉机-FAl05A2单轴流开棉机-FA029多仓混棉机-FAl79喂棉箱-FAll6主除杂机-FAl78A喂棉箱-FA23l梳棉机(带FT024匀整器)-FA306预并-E32条并卷-E62精梳机-FA326并条机(带自调匀整)-FA425粗纱机-FA506细纱机
3、工艺调试
由于带有自调匀整装置,我们采用一道并条8根并合。电机采用变频调速,最高速度可达600m/min,在精梳生产中,考虑到前后配台供应问题及成纱质量要求,我们选用300m/min的速度。对影响质量的主要工艺参数罗拉握持距、后区牵伸倍数、压力棒高低位置进行了正交试验,试验结果如下:
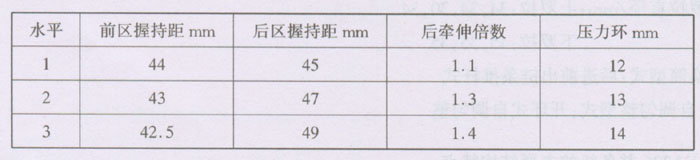
经试验,最终工艺确定为:前区握持距为42.5mm,后区握持距为47turn,后牵伸倍数为1.3倍,压力环为Φ13mm。
四、BYD型自调匀整装置的匀整设置
BYD型自调匀整装置是一种适合于高速并条机的开环式短片段自调匀整装置,它采用全部检测、全部匀整的方式,两眼独立进行控制,能够匀整喂人条中1.5~2cm以上长度的片段不匀,具有完善的系统自检测功能和棉条生产在线功能,能够在线显示多项工艺、质量、产量等数据,并能够根据用户设定的质量极限发出报警,自动停车。
在BYD短片段自调匀整装置中,对各种参数的设定和检测传感器、死区长度以及放大倍数的标定非常重要,它们的准确与否直接关系到匀整作用对棉条重量偏差进行补偿的延时同步性和准确性,是BYD型装置匀整效果好坏的关键。
1、工艺参数设置:
BYD必须在并条机工艺设计正确并且准确输入到BYD系统的情况下才能发挥作用,不恰当的工艺设置将导致出条质量的严重恶化,经试验主要工艺参数设置如下:预牵伸倍数1.3,预牵伸握持距47mm,主牵伸握持距42.5mm,
2、合理设定死区长度:死区长度是并条机喂入检测机构钳口到可调牵伸区内纤维变速点之间的距离,直接影响从凹凸罗拉传感器检测到棉条信号与伺服电机动作之间的时间差,是BYD最重要的系统参数之一,它直接影响生产棉条的条干CV%和重不匀指标。确定死区长度应做棉条试验,根据棉条的跳跃曲线确定死区长度。因死区长度与后区牵伸倍数、中后罗拉中心距及原棉长度有关,因此每次变换品种或调整工艺都需要对双眼的死区长度进行仔细调整。
3、合理选择放大倍数:放大倍数影响检测量与匀整量的比例关系,是BYD的另一个重要参数,它直接影响生产棉条的重量偏差和重量不匀率,它与喂人条的弹性及凹凸罗拉的加压等因素有关,在每次变换品种或调整工艺时都需要对双眼的放大倍数进行仔细调整。
4、选择适当的凹凸罗拉,凹凸罗拉是影响匀整效果的最重要的因素之一,因为凹凸罗拉的厚薄直接影响到位移传感器的位移变化量,从而影响匀整系统的正常工作,当喂人定量增大时,应选择较厚的凹凸罗拉,反之,应采用较薄的凹凸罗拉,相应集棉器和清洁棉铲也要随着变化。另外在生产过程中,必须始终保持其精确性及表面清洁,经常性的清除其表面及检测面的积尘与棉腊,保证其运行状态良好。
5、自调匀整的设定不能一劳永逸,工艺必须围绕着自调匀整不断优化改善,才能发挥其最有效的作用。在下面情况下应适当调整匀整系统(除系统损坏正常调整外)
(1)棉条支数变化时(2)原料变化时(3)输出速度变化时(4)改变牵伸倍数时(5)凹凸罗拉变化时(6)长时间没有开车时。
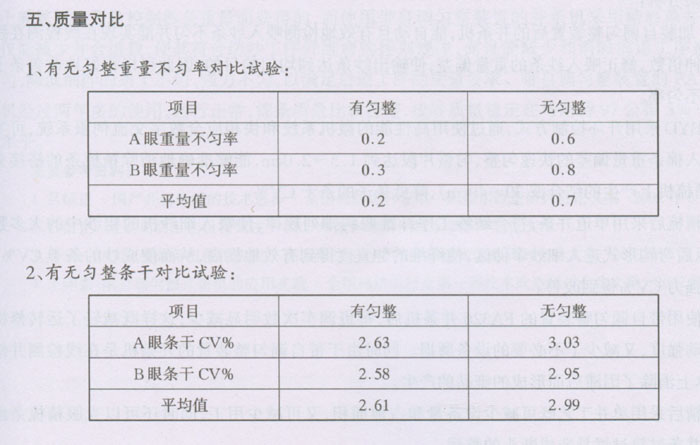
3、FA326一道与FA306两道成纱质量对比
试验条件:喂入条子相同,粗纱、细纱采用同台同锭,FA326带BYD自调匀整为单道并合FA206为两道并合,试验结果见下表:试验品种为JCl4.5

结果分析:
1、加装自调匀整装置后的并条机,能自动且有效地检测喂人纱条不匀并能实现在线检测在线调节牵伸倍数,修正喂人纱条的重量偏差,使输出纱条达到均匀的目的,因此可以很好地改善条子的重量不匀率。
2、EYD采用开环控制方式,通过使用高性能的微机系统和快相应全数字交流伺服系统,可实现对喂人棉条重量偏差的快速匀整,匀整片段达到1.5~2.0cm,能够准确地消除精梳条的搭接头(匀整精梳机上产生的结合波30-40cm),降低条子的条干CV%。
3、精梳后采用单道并条,符合纺纱工序纤维弯钩排列规律,使喂人细纱机的粗纱中的大多数纤维,以后弯钩形式进入细纱牵伸区,使纤维的伸直度得到有效地提高,从而使成纱的条干CV%、强力及强力CV%得到改善。
4、使用带自调匀整装置的FA326并条机后,每班调车次数明显减少,这样既减轻了运转修机工的劳动强度,又减少了不必要的设备磨损。同时由于带自调匀整装置的并条机是在线检测并修补,基本上消除了因滞后而形成的疵品的产生。
5、精后采用单并工艺既可减少设备量和占地面积,又可减少用工,同时还可以克服精梳条经过两道并条过熟过烂易造成断头的弊病。
六、使用管理:
1、在使用过程中,应注意保证齿形带张力松紧适当,若齿形带过松会产生跳齿现象,从而产生粗细节棉条,影响布面质量,若过紧,会使齿形带产生位移,从而引起运转不良。同时齿形带要保持清洁,不要沾上油污,齿形带轮与张力轮要保持平齐,否则会对条干产生不良影响,严重的会产生波。
2、定期更换差速齿轮箱内油液。
3、为了保证匀整质量,BYD一般需要每两周进行一次简单标定,每3个月进行一次全面标定。
4、自调匀整装置可以进行微量调节,但不宜过大,以免影响纺纱质量,当喂人条重偏差超过5%范围时,一般应调整前道工序工艺,也可调整本道工序工艺。
5、日常生产过程中应注意检测棉条质量,当出条重量偏差不大于0.5%时一般不要进行调整,必须调整时一次调整量也不可过大。
6、凹凸罗拉是影响匀整效果的最重要的因素,应定期检查凹凸罗拉径向跳动以及端面的磨损情况,同时必须始终保持其表面清洁,经常性的清除其表面及检测面的积尘与棉腊,保证其运行状态良好。
7、位移传感器至少每月检查一次,主要检查其探测头是否运动灵活,是否有卡死现象,弹簧是否能起作用,径向松动是否太大。
8、该设备机电一体化程度高,工艺技术、电气维修人员的业务水平要相应提高,才能使设备发挥最大潜能。
七、结语
传统的并条机只是通过并合和牵伸来提高纤维的“三度”,其棉条重量不匀率是依靠在并条机上频繁更换牙轮控制熟条重量而获得的,而使用带自调匀整装置的并条机采用精后单并工艺,不仅能减少并合道数,使其符合纺纱工序纤维弯钩排列规律,而且能减少和消除前道工序造成的不匀,降低细纱的条干不匀、强力不匀,以满足后道工序的质量要求。带自调匀整装置的FA326并条机经过两年多的使用,运行正常,棉条质量比较稳定,成纱质量稳定在乌斯特97公报5%~25%的水平。
更多并粗会议论文请点击进入>>>