为此,我们针对并条工序的特点,作了一些工艺的对比研究,并对并条工艺作了一定的改进,使产品质量有了很大的改善。具体措施有:
一、改变头并的并合数
选择合适的工艺道数,保持足够的并合数,对于改善纤维伸直平行度和提高混合均匀效果十分重要,在传统纺织工艺中,将普梳产品的并条工艺道数设计为2道,采用8×8的并合数,由于并合技术和牵伸技术是一对矛盾,如此多的并合数,虽对改善棉条的重不匀有效,却加重了牵伸的负担,使棉条中纤维疲劳、熟烂,易生棉结,同时亦增加了附加不匀率,我们尝试着将并合数由原来的8×8改为6×8,通过试验,我们发现,把头并的并合数由8根改为6根以后,头并的棉结有了大幅度的下降,细纱成纱水平也有了很大的提高,其试验结果见表l
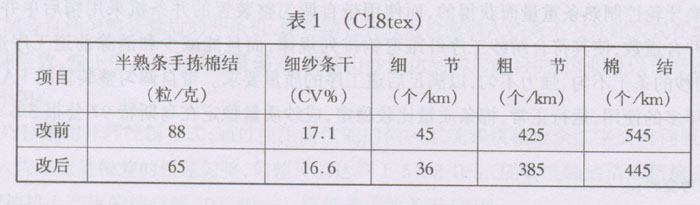
二、调整后区牵伸倍数
并条机的后区是提高棉条内纤维伸直度和分离度的关键部位,其中头并后区对条子的内部结构影响尤为明显,头并喂人的梳棉生条纤维排列比较紊乱,内在结构较差,前弯钩纤维占很大比重,由于前弯钩纤维在牵伸过程中容易形成棉结,加之近来原棉中短纤维含量较高,造成条干基础差,粗细节也较多,为了进一步改善纤维之间的伸直度、平行度、分离度,减少棉结的生成,提高条干水平,我们在头并8改6的基础上,适当加大了头道并条的后区牵伸倍数,将头并后区牵伸倍数由1.475调整为1.720。
末道并条除了要改善棉条中纤维的伸直度、分离度,还要使熟条条干控制在一定的水平内,我们将末道后区牵伸倍数调整为1.025倍的弹性牵伸。
工艺调整前后对比试验表明,头并后区采用纤维定向度工艺,头并采用少并合小牵伸倍数办法,即6并6倍牵伸办法后,棉结数量增加很少,成纱质量水平却有了很大提高,试验结果见表2
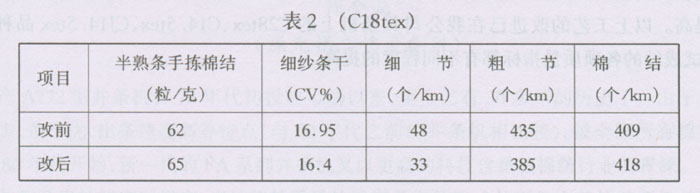
三、调整牵伸罗拉隔距
正确配置罗拉握持距对提高棉条质量。改善棉条内纤维排列状态至关重要,纤维长度及整齐度是决定罗拉握持距的主要因素,握持距过大会使条干恶化,成纱强力下降,过小则牵伸效率较弱,形成粗节和纱疵,甚至出现出“硬头”现象。由于梳棉出来的生条中的棉纤维排列紊乱,前弯钩纤维居多(占70%),为了提高棉条中纤维的分离度、伸直平行度,尽量多的消除棉纤维的前弯钩,减少棉结,我们尝试适当增长后区牵伸隔距,通过试验,我们将头并握持距由41×44 改为41×46 ,二并为了有效控制纤维,改善条干水平,隔距由41×46 改为40×46 。通过试验对比,半制品及成纱质量均有所提高,试验结果见表3
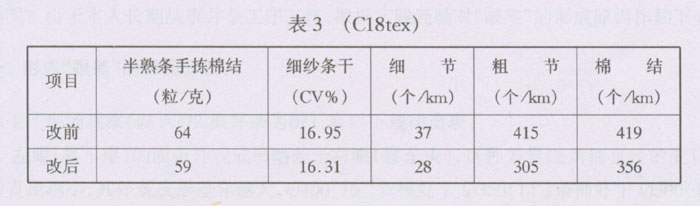
经过对并条工艺的调整改进,在细纱工艺不变的情况下:通过几个月的成纱取样测试,证明细纱成纱条干CV值,细节、粗节、棉结等几项质量指标有了明显的提高。调整工艺前后试验数据见表4
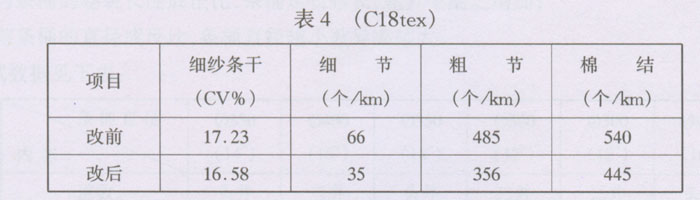
四、结语
通过以上数据的分析,我们发现:并条工序作用很大,只要选择了合适的工艺,使棉条中棉纤维的伸直度、平行度、分离度得到较好的改善,在其他条件不变的情况下,同样将会使成纱质量水平得到提高。以上工艺的改进已在我公司并条机上的C28tex、C14.5tex、CJl4.5tex品种推广应用,经测试成纱的各项质量指标都有不同程度的提高。
更多并粗会议论文请点击进入>>>