1.1 氨纶弹力纱线的类型及其特点
目前应用最为广泛的氨纶弹力纱线主要有3种形式:包芯纱、包覆纱和合捻线。3种弹力纱线都是氨纶丝的深加工产品,其不同的加工原理形成了不同的纱线风格。
1.1.1氨纶包芯纱
是以氨纶丝为纱芯,外包一种或几种非弹力的短纤维纺成的纱线。氨纶包芯纱可获得良好的手感与外观,以天然纤维为外包纤维的纱线吸湿性好,可根据产品的用途选择不同的弹性值。氨纶包芯纱与其它弹力纱线相比的显著特点是纱线在拉伸状态下芯丝不外露,因此染色效果好,宜做包括深色在内的各种颜色的产品。与其它类型的弹力纱线相比,包芯纱强力较低,一般单纱强力只相当于同规格外包纤维单独成纱的80%~90%。
1.1.2氨纶包覆纱
是以氨纶丝为芯,无弹性的长丝或短纤维纱线按螺旋形的方式对伸长状态的氨纶丝予以包覆而形成的弹力纱。氨纶包覆纱是在具有空心锭子的专用设备上加工的,全机分为弹力纱芯喂给、拉伸包覆和松弛卷取等3部分。包覆纱与其它弹力纱线的最明显区别之一是芯丝无捻度。包覆纱中氨纶丝与外包层之间的芯鞘关系明显,芯丝与外包层之间的抱合程度明显低于包芯纱和合捻线,因此其弹性高于后两者。包覆纱在张紧状态下有露芯现象,因此不宜做深色产品。包覆纱的手感较包芯纱硬,其强力是外包层长丝或纱线的强力,因此比同规格包芯纱的强力高。包覆纱为松弛卷绕,根据不同的用途其卷取率一般为60%~95%,这一点有别于包芯纱和合捻线,对织造工艺参数的影响较大。
1.1.3氨纶合捻线(又称合股线)
将氨纶边拉伸边与其它无弹性的两根纱并合加捻而成,一般在加装了特殊喂纱装置的环锭捻线机上生产。氨纶丝能与各种纱线或长丝配合生产弹力合捻线,并适合小批量多品种生产,甚至一台捻线机可同时加工几个品种。在张紧状态下,氨纶丝与其它纱之间是互相捻绕的关系,因此纱线在张紧状态下氨纶丝外露,染色时易造成色花色差,不宜做深色产品。氨纶合捻线的强力等于与之配合的非弹力纱线的强力,因此较同规格氨纶包芯纱的强力高。氨纶合捻线中氨纶丝与其它非弹力纱线之间的抱合程度低于氨纶包芯纱,体现为氨纶丝的回缩程度高于包芯纱,因此合捻线的弹性高于包芯纱。
1。2 氨纶包芯纱的纺纱原理
1.2.1环锭纺氨纶包芯纱
氨纶包芯纱可采用环锭纺、转杯纺、赛络纺、涡流纺、静电纺等方法纺制,使用最广泛的是环锭纺,其纺纱原理如图2所示。
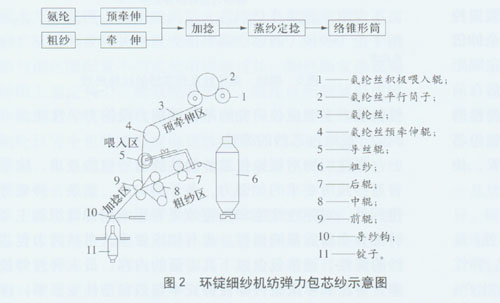
一般棉/氨纶包芯纱以60~80℃、15~20 min进行两次真空汽蒸定形为宜,毛/氨纶包芯纱以80℃、40 min的定形条件为宜。
1.2.2转杯纺氨纶包芯纱
转杯纺纺制氨纶包芯纱的纺纱原理如图3所示,
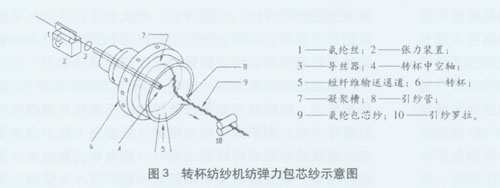
1.2.3赛络纺氨纶包芯纱
在细纱机上加装适当装置后可纺制赛络纺弹性包芯纱。这种纱除了具有赛络纺纱和氨纶包芯纱的优点之外,还可避免包芯纱生产过程中由于工艺缺陷或设备状态不良等造成的露芯、空鞘等特有纱疵。所纺制的纱线芯丝包覆效果好,毛羽少,外表光滑,耐磨性能好,成纱质量高。
赛络纺的纺纱原理如图4所示,
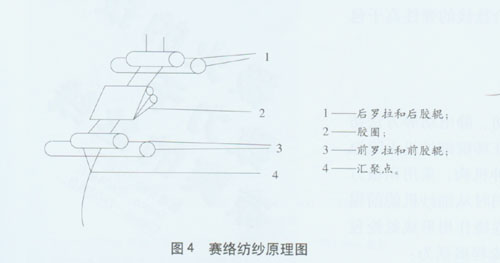
纺制赛络纺包芯纱时,氨纶长丝在芯丝退绕装置控制下,通过与前罗拉的速度差给予芯丝一定的预牵伸倍数,经过导丝轮从前罗拉喂入;两根粗纱通过一定隔距的粗纱喂入器从后罗拉喂入,经一定倍数的牵伸后在前罗拉出口处与氨纶芯丝捻合,从而形成具有一定弹性的赛络纺氨纶包芯纱。在此过程中,前罗拉出口处氨纶芯丝与两根经牵伸过的粗纱捻合时要控制好芯丝位置,使其位于纱芯正中,不致产生露芯和空鞘等纱疵。
1.3氨纶包芯纱的力学性能
氨纶包芯纱的力学性能(包括强力、伸长和弹性)是影响弹力织物的重要基础,分析影响包芯纱强力、弹性的因素,对包芯纱和弹力织物的原料选择、设计、生产,以及理解弹力纱线和织物的变形机理等均有参考意义。
1.3.1氨纶包芯纱的拉伸性能
氨纶包芯纱的拉伸曲线均为上凹曲线(图5),
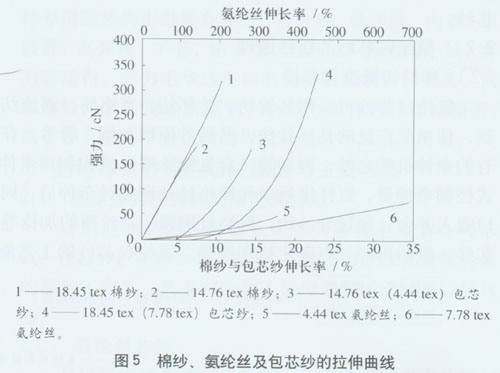
因此,可以把弹力纱的拉伸过程分为两个阶段,即低应力高伸长段和高应力低伸长段。两段的分界点所对应的拉力范围和纺纱张力的大小范围非常一致。要使弹力织物具有较大的伸缩能力,弹力纱在其中所表现出的弹性一定位于低应力段,因此研究比较弹力包芯纱的弹性性能,主要应该研究的是其低应力段的力学性能。
1.3.2氨纶包芯纱的弹性
弹性织物对氨纶包芯纱的性能有一定的要求,除了普通纱线所要求的如强力、条干均匀度、结杂、纱疵等指标外,对弹性性能和包覆效果等影响到弹性织物主要特征和布面质量的指标,也有相应要求。考核弹力包芯纱的弹性,通常包含以下几方面的内容:最大弹性伸长率;多次和单次拉伸弹性伸长率与残留塑性变形率;弹性伸长率的不匀率。
氨纶包芯纱的弹性主要取决于氨纶丝的细度、预牵伸倍数和氨纶丝的含量。氨纶丝越粗其弹性越大,目前氨纶包芯纱生产上应用最多的氨纶丝细度主要有44、77和155 dtex等3种,其它的多用来纺包覆纱。其中44 dtex氨纶丝适纺低弹纱,可织内衣、游泳衣等;77 dtex氨纶丝适纺中弹纱,可织牛仔布、袜子、衬衣等;155 dtex氨纶丝适纺高弹纱,可织腰带、弹性连接部分等。
氨纶丝的预牵伸至关重要,它不仅直接影响弹性,还影响成本。氨纶丝预牵伸倍数过低时不能充分发挥氨纶的潜在弹性,则所需氨纶含量高,成纱强力低,成本增加。而氨纶丝预牵伸倍数过高时,则容易引起断头,使纺纱困难。氨纶丝的预牵伸倍数一般在3~5倍内。不同规格的氨纶丝预牵伸倍数不同,44 dtex氨纶丝预牵伸倍数一般为3~4倍;77 dtex氨纶丝一般为3.5~4.5倍;155 dtex氨纶丝一般为4~5倍。
氨纶丝含量高,则纱的弹性大。但由于氨纶丝比较昂贵,并且氨纶丝含量高会影响成纱强力,所以在保证弹力及织物性能的情况下,必须严格控制其含量以降低成本,并保证成纱强力。根据纱线规格和用途,氨纶丝含量一般控制在3%~15%范围内较好,普通氨纶弹力包芯纱中氨纶丝的含量一般不超过10%。
1.4氨纶包芯纱的包覆效果、特有纱疵和消除措施
1.4.1氨纶包芯纱的包覆效果和特有纱疵
氨纶包芯纱的包覆效果是指它的外包纤维是否均匀、连续地分布在芯丝的周围。如果包覆不匀,尤其是露芯,产品将在染整工序中产生质量疵点。氨纶包芯纱包覆不良产生的特有纱疵主要有空芯、露芯、空鞘、麻花纱和弹性不均匀等。
空芯纱疵的成因主要有以下几个方面:首先,当氨纶丝断头后,外层纤维不断,继续纺纱,挡车工未发现或未及时发现,重新接头后无芯纱没有剔除或剔除不彻底,从而形成较长片段或短片段空芯纱。另外,由于钢领与钢丝圈配置不当或使用周期过长,钢丝圈发热或钢丝圈上磨出利刃,把氨纶丝割断,氨纶丝回缩就形成短片段空芯。特别是包覆效果不良时,外层短纤维不能把氨纶丝完全包住或形成麻花纱的情况下,更易发生这种情况,而日.这种空芯往往是密集地连续出现,整段纱线几乎失去弹性。
露芯和麻花纱是由于外包纤维对芯丝包覆不足所致。主要原因是工艺配置不当,如氨纶丝规格或氨纶丝牵伸倍数选择不当,芯丝含量偏高;氨纶丝与短纤维须条的相对位置不当;导丝器形式设计不合理或导丝器位置安装调节不适当等。另外,纺纱过程中由于各种原因断头,重新接头时如果接头技巧掌握不好,使氨纶丝尾端暴露于纱体之外而形成“裸芯尾巴”。
产生空鞘的原因是由于外包覆的粗纱须条在牵伸部位断头,或者虽然及时补充,但须条吸入到集棉管,而剩下无包覆的芯丝。这一段纱的弹性大于正常包芯纱,这种缺陷在纺制低线密度纱或芯丝较粗时容易发生,因为截面中的纤维根数较少,纤维抱合力减小,牵伸时容易断裂。芯丝含量超过20%~25%时,纱的质量就很差。
弹性不匀是由于氨纶包芯纱是多锭纺制,每个锭位之间的张力、锭速等参数的差异形成牵伸差异,会造成包芯纱之间的弹性差异。同一批弹力纱线中如果采用了不同批号或不同品牌的氨纶丝,或者加工同一批纱线时工艺参数有差异,也容易形成弹力纱之间的弹性不匀。
1.4.2氨纶包芯纱纱疵消除措施
氨纶包芯纱的特有纱疵会使弹力织物产生不良效果,经济损失较大,从提高氨纶包芯纱包覆效果入手,重点控制纺纱断头,在氨纶丝牵伸机构设计合理的条件下,针对不同品牌特性的氨纶丝,优选牵伸工艺,优选外层纤维的加工工艺,选配使用好钢领和钢丝圈,并且注意现场管理和操作方法,氨纶包芯纱的特有纱疵基本能够消除或避免。
1.4.2.1提高氨纶包芯纱包覆效果
提高包覆效果的主要措施如下:首先,合理的导丝器形式和安装方式是确保包覆效果的重要条件,也是实现正常纺纱的重要条件,实践证明一种封闭式的导丝器对改善包芯纱包覆效果、实现正常纺纱非常有效。其次,状态保持良好,使氨纶丝与短纤维须条所处的相对位置正确合理,工艺上控制氯纶含量不宜太高,选择较好品质的外层纤维原料等,是切实可行的措施。另外,各道工序须条或纱线通道保持光洁,避免纤维刮毛起球而产生露芯或断丝。
1.4.2.2减小氨纶丝断头率
1)合理选择氨纶丝预牵伸倍数
首先,不同规格的氨纶丝预牵伸倍数选择范围不同。根据纺纱实践,常用的几种细度氨纶丝一般采用的预牵伸倍数为:4.4 tex,3~4倍;7.7 tex,3.5~4.5倍;15tex,4~5倍。第二,同一规格,但不同品牌,甚至同一品牌,不同批号的氨纶丝,预牵伸倍数的选择也有差异。例如,DuPont公司7.6 tex氨纶丝推荐预牵伸倍数为4.0倍。而日本旭化成株式会社生产的7.6 tex氨纶丝选用3.5倍左右的预牵伸倍数较合适。实际生产中,对每批氨纶丝原料的内在质量指标和适纺性能在投料前最好进行一次测试,取得氨纶丝断头数据后,再选择合理的预牵伸倍数。
2)合理设计氨纶丝牵伸系统
首先,将粗纱托架改为吊锭式,送丝辊下移至粗纱的F前方,送丝辊至前罗拉的距离可控制在500mm以下,大大缩短氨纶丝在牵伸状态下的行进时间,则氨纶丝断头会减少50%左右。其次,在氨纶丝牵伸系统设计中,将变换齿轮设计成2只或3只,则牵伸倍数选择范围较广,且更为准确,有利于选择到较合理的牵伸倍数,使氨纶丝断头降到最低程度。
1.4. 2. 3减小外包纤维断头率
主要有以下几项措施:第一,合理选配外包纤维原料,优化前纺工艺。前纺最好经过精梳处理,最大程度地去除短绒。第二,控制氨纶含量不宜太高。根据纱线规格和用途,一般控制在3%~15%范围内较好。含量过高,外层纤维中空程度偏大,纤维抱合力减弱,既易产生断头,也影响包覆效果,易产生空鞘和露芯纱疵。第三,适当降低车速有利于减少外包纤维断头。
1.4.2.4合理选配钢领和钢丝圈
钢领与钢丝圈的选配或使用不当,易使包芯纱外包纤维起球、剥皮而露芯,进而可将氨纶丝刮断形成空芯纱。氨纶弹力包芯纱的弹性伸长性能对纺纱突变张力具有较好的吸收能力,使细纱断头降低,这对适当放大卷装、选用边偏宽的钢领有利。宽边钢领所对应的钢丝圈通道要大些,钢领寿命也长,对改善成纱毛羽有利。选择钢丝圈形状和重量的依据是氨纶丝线密度、纺纱线密度、钢领直径、边宽和锭速等。一般要注意以下几个问题:第一,钢丝圈的纱线通道应偏大些,截面以瓦楞形和薄弓形为好,不易刮毛包芯纱和刮断氨纶丝。第二,由于含有氨纶丝的缘故,在纺纱中气圈张力增大,钢丝圈质量一般比同号非弹力纱偏重两档,调换周期缩短1/3。
1.4.2.5解决好弹性均匀问题
弹性不匀主要是由每根纱之间牵伸不一致或氨纶丝本身的差异造成的,其解决措施包括以下几方面:第一,氨纶丝送丝辊的加工精度要有保证,每根丝辊之间、每只锭位之间的直径差异要尽可能小,从而保证氨纶丝的送出长度一致。第二,每只锭位之间的张力要一致。张力在一定程度上反映出牵伸状态,在纺纱过程中,特别在断头后应检查一一下氨纶丝的张力是否有差异。第三,锭速要一致。钢丝圈的重量和车速在纺制某品种同一批纱时应保持一致,并且要保证钢领与钢丝圈的良好配合状态。第四,在纺制某批号同一批纱时,氨纶丝原料应该稳定,不要用不同品牌氨纶丝纺制同一批号的包芯纱,牵伸工艺齿轮配置应完全相同,且中途不得随便调整。
2含氨纶纺织品的热定形
含氨纶纺织品在高温下通过控制张力,不仅可以改变织物的尺寸,而且可以消除内应力,使尺寸稳定达到定形的目的。各种氨纶或含氨纶纺织品都需要热定形,从而调节包括纺织品弹性、模量、织物宽度、密度、形状、长度和纤维线密度等特性。
2.1热定形的机理
氨纶和其它热塑性合成纤维一样,在热定形过程中,纤维分子链间作用力将发生拆散和重建。由于其分子链是由软硬两段构成的“区段”结构,在定形过程中,由于温度和应力不同,将发生不同区域的链段取向、重排,直接影响它的伸长、收缩变形,也影响它的弹性、强力和染整加工性能。
在正常状态下,氨纶中的软链段呈无规则卷曲状态,是纤维的连续相,通常占总重量的65%~90%,它们在松弛的纤维中属非取向和非结晶状态;硬链段主要由氨酯脲构成,结构非常紧密,但它们之间存在较多的氢键,特别是由偶数碳原子的二胺作扩链剂的氨纶,理论上每一个二胺链段可生成4个氢键,所以硬链段还存在相互贯穿,两者间不存在明显的相界面。这种结构特征,造成氨纶在热定形时,纤维内部会发生复杂的变化,对温度和张力非常敏感。
当温度高于氨纶的玻璃化转变温度(聚醚型的约为-70~-50℃)时,软链段就可运动,并随着拉伸而伸长和取向。温度越高,张力越大,这个过程也越快。伸长的幅度决定于链段(聚醚或)的长度,当链伸展变直后,趋于平行,并发生结晶,此时纤维明显伸长和变细,刚性和强度增加。当撤去外力时,迅即发生回缩,软链段的结晶趋于消失,大分子链又重新变卷曲,但一般不会立即回到原来状态,需要一定时间才能完全恢复。当在温度和拉力都较低的变形过程中,硬链段未发生大的变化,软链段起初只是处在无序状态,只是在反复拉伸变形过程中,硬链段才逐渐承受负荷,并逐步取向。一般认为,大约从100%的伸长起(根据硬链段种类和链段长度而定),就能发生氨酯脲键的重排。在温度高于100℃时,随着
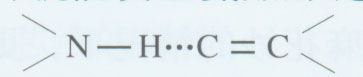
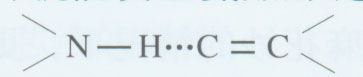
当温度进一步提高时,硬链段的剧烈软化,并出现部分流动,致使所产生的伸长取向破坏,一些受负荷大的硬链段会从硬段区中熔出,这时纤维“模量”低,断裂伸长则高,发生变形,之后在新位置上重新建立结合点,降温后形态被稳定。
热定形的条件随纤维类别、交织物的结构与组成、加热方式的不同而有所变化。通常前定形的目的主要是消除折皱印和稳定门幅,热定形温度应略低,机织物在180℃左右,如果进行一次定形,温度可略高些,在190℃左右。后定形的温度比前定形略高,蒸汽定形的温度最低,水蒸汽对氨纶还有一定的增塑作用,其温度为1 16℃左右。高温水蒸汽对氨纶有损伤作用,不宜采用过热蒸汽定形。定形最高温度一般不超过195℃,定形时间随温度和定形加热方式而不同,通常热空气加热为20~90s,116℃蒸汽定形的时间较长,为5~40min。定形温度过高,时间过长,或多或少会引起聚合物降解。
对氨纶交织物来说,定形好坏在很大程度上决定于交织的其它纤维,同时因为其它纤维大多在纱线外层,含量也较高,所以定形条件视织物结构而异。如果是和热塑性的合成纤维织成交织物,例如锦纶/氨纶针织物,则可在1 80~210℃下短时间定形,可得到成形针织物,或得到防抽丝的长统袜。其它类别的含氨纶纺织品的定形条件也可调整。氨纶及其织物的热定形作用机理图解见图6。
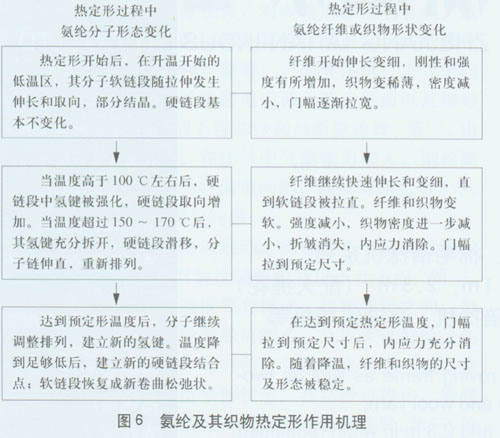
2.2热定形对氨纶及其纺织品性能的影响
氯纶丝热处理之后,其断裂强力、伸长和定负荷伸长均有所下降,其中断裂伸长的下降幅度较小,断裂强力和定负荷伸长的下降幅度较大。温度低时定负荷伸长较大,温度高时定负荷伸长较小。热处理温度对氨纶丝的沸水收缩率,即尺寸稳定性有一定的影响。氨纶丝的牵伸倍数对氨纶丝的性能影响最大,尤其对氨纶丝的弹性、长度稳定性影响较大,在热处理时氨纶丝的牵伸倍数愈大,其弹性下降愈大,长度稳定性愈差。表5列出了定形温度与时间对氨纶丝弹性的影响。
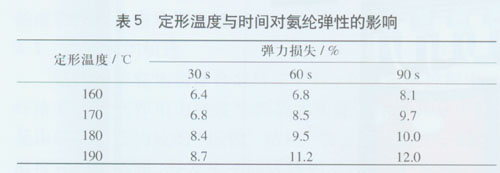
无论是热定形还是其它高温处理,或多或少都会使氨纶的微结构发生变化,而微结构变化又会引起氨纶的性能变化,由此产生3种结果:1)减小氨纶的弹性;2)减小单位面积的氨纶含量;3)减小氨纶的总伸长。从织物来看,会使织物变稀变薄;从纱线来看,单位长度的氨纶含量减小,它的弹性会有所降低。
3氨纶纺织品的染整加工
对弹性纺织品来说,加工时控制弹性和尺寸稳定性特别重要,也是最困难的因素之一。弹性和尺寸稳定性与许多工艺有关,相互又存在矛盾,图7是影响它们的一些加工及相互的关系。
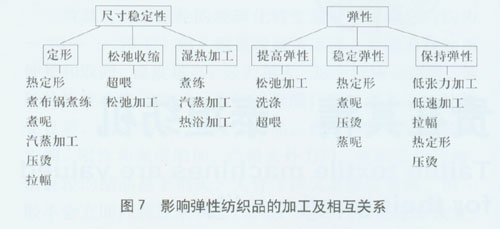
不同含氨纶纺织品有不同的染整加工方式和加工流程,所使用的设备也不同,但共同点是,它们都要经过松弛(收缩)、精练、热定形、染色或印花和后整理加工。
对经编和机织物来说,工艺流程主要有以下几种:1)汽蒸松弛-热定形-精练-染色或印花-后整理-验布-成品;2)水浴精练松弛-烘干-热定形-染色或印花-后整理-验布-成品;3)溶剂精练松弛-热定形-染色或印花-后整理-验布-成品;4)松弛-精练-染色或印花-热定形-后整理-验布-成品;5)溶剂精练松弛-荧光增白或轧染-烘干或热定形-验布-成品。
具体的工艺还有多种,有的还要丝光和二次热定形。而松弛加工有以下4种方法:
1)汽蒸松弛:在连续汽蒸箱或热定形前的附加汽蒸箱中进行(1 O0℃);
2)热水松弛:间歇或连续式,也可在精练、染色设备中松弛(60~90℃);
3)溶剂松弛:在连续式溶剂处理设备中进行(和干洗、精练一起进行);
4)干热松弛:在高温松弛状态进行(较少应用)。
一般推荐氨纶织物热定形温度为190℃左右,通常是在180~195℃下干热处理30~80 s。
正是由于控制弹性和尺寸稳定性特别重要,在氨纶制品的染整加工中应注意以下几方面问题。
1)氨纶的弹性变形中,有相当一部分是缓弹性变形,只有时间足够长才能完全回复。织造下机坯布随时间的延长,有一段时间内幅宽会越来越小,所以坯布下机后要存放足够时间后才能进入下道工序。
2)高温定形之后的弹性织物,由于氨纶特有的延时回缩,尺寸还会变小。为保证尺寸稳定和缩水合格,定形后采用松弛整理。
3)为使高温定形顺利进行,控制温度一定要准确、稳定,定形温度不能超过±2℃。
4)不能用含氯漂白剂,因氯化作用,纤维在损伤过程中会泛黄。
5)氨纶不耐高温或强碱作用,型中的酯基很易水解断裂,氨酯基也同样会遭到水解。因此,含氨纶的棉机织物丝光时要防止氨纶损伤,型的氨纶交织物不能进行丝光,聚醚型的氨纶交织物丝光时应控制烧碱浓度小宜过高(一般控制在l 80 g/L左右),特别要注意的是去碱箱的温度,温度应低。丝光的车速也宜快,尽量减少氨纶损伤。
6)为了使最终成品织物达到所需的稳定尺寸(如门幅),热定形后还何湿热处理工序,因此,热定形必须在前处理的湿加工之前进行。热定形工序设置的原则是:当下机(指织机)坯布门幅小于成品要求时,坯布可以进行热定形;若下机坯布门幅大于成品要求,可先进行湿热处理后再进行热定形,以控制织物的尺寸稳定。在给定的热定形温度和时间下,确定织物热定形的幅宽,热定形的幅宽超过成晶幅宽的10%~15%即可。热定形后,试样在沸水中处理5~10 min,并经松弛烘干。
7)由于在l00℃以上有水存在的条件下会损伤氨纶纤维,因此,过热蒸汽的湿热定形是不可取的。同理,含氨纶的合纤织物,也不宜采用常规的高温高压染色工艺。