随着集约化大农业的发展,以人工种植管理棉花逐步被化所代替。采棉机的问世,可缓解人工采摘棉花劳动力紧张的矛盾,但是采摘棉花属一次性采摘,棉花等级不分,高等级棉和低等级棉采摘后自然混合,大大影响了纺纱性能,同时加大了生产成本。
1 机采棉与人工采棉的物理指标比较
机采棉与人工采棉的物理指标比较见表1。
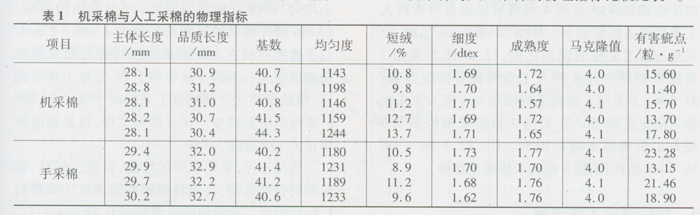
从表1试验数据可知,机采棉与人工采棉都是二级棉,其细度接近,但机采棉的主体长度短,而短绒率和有害疵点高。机采棉与人工采棉的主要有害疵点分别是带纤维籽屑和棉结,机采棉带纤维籽屑多,人工采棉的索丝比机采棉多。
2纺纱试验
在确定纺纱方案时,考虑到原棉的实际情况,针对生产不同品种和纺纱规格。其配棉有不同的要求。精梳纱比普梳纱的配棉等级要高,有害疵点要少;涡流纺纱用棉要求纤维长度长,整齐度要好,有害疵点要少;转杯纱全部采用低等级机采棉。各品种的配棉和要求:CJ 18.2 tex针织或直接出口纱,产品定位为高档产品.配棉等级为2.5级;C 18.2 tex针织或直接出口纱,产品定位为中档产品,配棉等级为3.0级;涡流纺18.2 tex针织或直接出口纱,产品定位为中高档产品,配棉等级为3.0;OE 22.4 tex~OE 36.4 tex针织纱,产品定位为低档产品,配棉等级为3.5级,全部采用机采棉。各品种采用搭条的方式进行混纺。为了了解机采棉对成纱质量的影响情况和成纱质量状况,有些品种采用多种比例,而转杯纺采用纯机采棉进行试纺。
各品种的混纺比例和棉条搭配根数:CJ 18.2tex品种,机采棉与人工采棉的混和比例,12.5/87.5采用1根机采棉棉条与7根人工采棉棉条搭配混和;25/75采用2根机采棉棉条与6根人工采棉棉条搭配混和;37.5/62.5采用3根机采棉棉条与5根人工采棉棉条搭配混和; 50/50采用4根机采棉棉条与4根人工采棉棉条搭配混和。C 18.2 tex品种,100%纯纺采用8根机采棉棉条纺纱;机采棉与人工采棉的混和比例,37.5/62.5采用2根机采棉棉条与6根人工采棉棉条搭配混和;50/50采用4根机采棉棉条与4根人工采棉棉条搭配混和。MVS C 18.2 tex品种,机采棉与人工采棉的混和比例,12.5/87.5采用1根机采棉棉条与5根人工采棉棉条搭配混和;37.5/62.5采用2根机采棉棉条与4根人工采棉棉条搭配混和;50/50采用3根机采棉棉条与3根人工采棉棉条搭配混和。OE 22.4 tex-OE36.4 tex品种,采用8根机采棉棉条纺纱。
3纺纱试验工艺流程
(1) CJ 18.2 tex

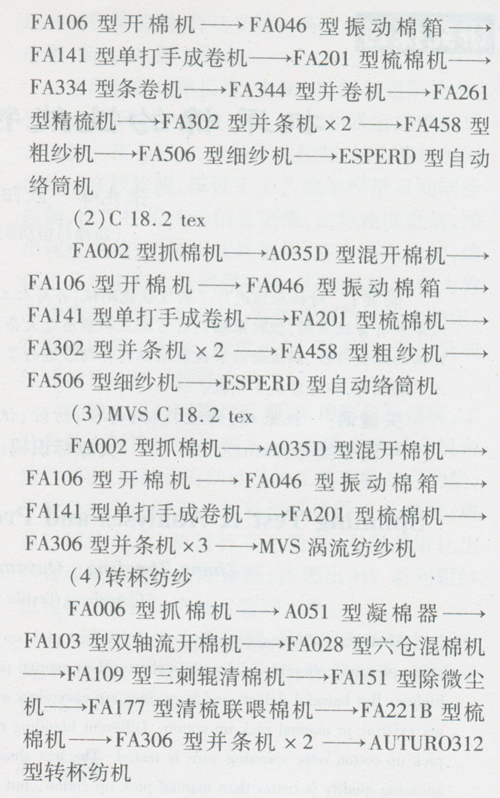
4各工序纺纱工艺参数及技术措施
各工序纺纱主要工艺参数见表2。
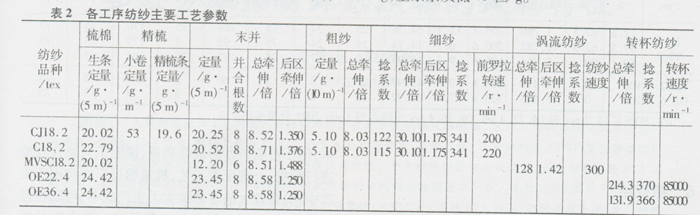
机采棉在开清棉工序采取勤抓薄喂,少打多梳的工艺原则。FA002型抓棉机打手伸出肋条距离由0±1 mm调整到-2 mm,使所抓取的棉束细小均匀,确保原棉充分混和,减少棉结的形成。FA106型开棉机的隔距均匀放大1 mm~2 mm,打手速度控制在480 r/min左右,保证机采棉棉杂和短绒充分下落。从棉网上看,采取上述措施后,棉结杂质比全部用人工采棉时下降了27粒/g,索丝也明显减少。在开清棉工序,机采棉落棉率比人工采棉高3.8%.
梳棉工序,采用较轻的定量,以减少锡林、盖板间的针面负荷,将锡林刺辊的线速度比调整到1.8,给棉板与刺辊的隔距调整到0.48 mm左右,加长刺辊与给棉板间的打击长度,以减少纤维的损伤,有利于棉结杂质和短绒的下落。梳棉工序机采棉与人工采棉相比落棉率高6%,除杂效率高9%,制成率低11%,生条含短绒率高2%,生条棉结低0.008粒/g,生条杂质低0.283粒/g。纺转杯纱时FA221B型梳棉机机采棉与人工采棉相比,落棉率高7%,除杂率高6.2%,制成率低5.4%,生条短绒率高3%,生条棉结高0.008粒/g,生条杂质低40粒/g。
精梳工序,机采棉与人工采棉相比,落棉率高8%。精梳条棉结粒数高9.6粒/g,杂质粒数低8.2粒/g,落棉率眼差不超过2%。
由于机采棉落棉高,梳棉机的牵伸倍数由93倍降到87.5倍。为了控制精梳定量,将顶梳刺人深度由+0.5 mm提高到+1.0 mm,牵伸倍数由原来的10.5倍降为9.6倍,加强对纤维的强分梳,在转杯纺清梳联生产线,FA221B型梳棉机落棉率比人工采棉同工艺时高7%,通过自匀调整控制棉条定量。
并条工序,为确保棉条质量,减少棉结,对牵伸倍数做了调整,头并后区牵伸倍数改为1.7倍~1.8倍,转杯纺纱和MVS涡流纺纱,通过自匀调整来控制棉条定量。
CJ 18.2 tex品种,机采棉与人工采棉的混和比例,12.5/87.5、25/75、37.5/62.5、50/50并条后熟条萨氏条干分别为6.5%、10.05%、7.92%、7.89%, C 18.2 tex品种,机采棉与人工采棉的混和比例,37.5/62.5、50/50并条后熟条萨氏条干分别为12.24%、11.24%。C 18.2 tex涡流纺纱,机采棉与人工采棉的混和比例,12.5/87.5、37.5/62.5、50/50并条后熟条萨氏条干分别为11.33%、10.25%、9.94%。转杯纱两个品种纯机采棉棉条萨氏条干为12.46%。
粗纱工序,CJ 18.2 tex和C 18.2 tex均采用较大的捻系数,捻系数控制在122,防止粗纱退绕时发生脱断和意外伸长,有利于成纱条干。纺CJ18.2 tex时,机采棉与人工采棉的混和比例,12.5/87.5、25/75、37.5/62.5、50/50的粗纱萨氏条干分别为13.57%、12.74%、12.78%、11.87%。纺C 18.2 tex时,机采棉与人工采棉的混和比例,37.5/62.5、50/50的粗纱萨氏条干分别为14.75%、15.38%。
细纱,涡流纺和转杯纺工序所采用的工艺与人工采棉相同。
5成纱质量测试
环锭纺纱质量检测结果见表3,涡流纺与转杯纺成纱质量检测结果见表4。
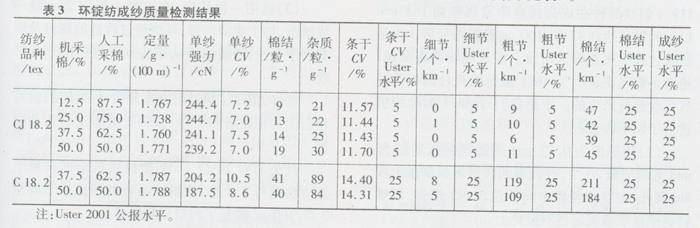
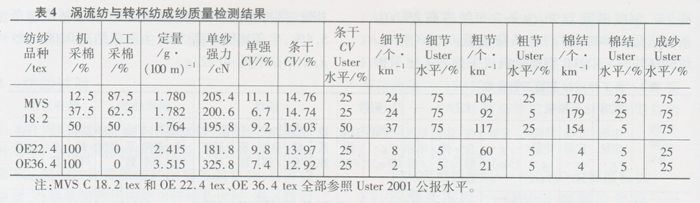
6 结束结
从成纱质量情况来看,机采棉与人工采棉,不同混纺比例均能达到较好的质量。从CJ 18.2 tex和C 18.2 tex质量情况来看,两者搭配对半时,成纱的棉结、细节、粗节更好些,比全部采用人工采棉要稍好,搭配机采棉比例越高,质量越好。从OE 22.4 tex、OE 36.4 tex产品的质量结果可知,全部采用机采棉,除条干外,粗节、细节和棉结质量情况都很好,超过用人工采棉时的质量指标。而在纺MVS18.2 tex产品时,其质量情况与手采棉相同,因MVS涡流纺设备对原棉主体长度要求较高。机采棉的有害疵点含杂是大杂,易于清除,对纺纱非常有利,是人工采棉所不具备的,只是在生产过程中,落棉率比全部采用人工采棉时高。其制成率比人工采棉低0.15%,加大了生产成本,但不影响纺纱的最终质量,说明了只要合理地进行配棉,合理配置工艺,机采棉可广泛应用于生产中,只是较大的落棉加大了生产成本,可以在经废棉处理后,用于转杯纺纺粗号纱。更合理的纺纱生产将在今后进一步探讨。