成纱棉结是衡量纱线质量的一项重要指标,它不仅影响成纱和织物的外观,而且还影响后加工质量和生产效率。造成纱线棉结的主要因素是原棉性能、清梳工艺及精梳工艺等。随着产品档次不断提高,纱线棉结的危害日益突出。我们通过工艺试验,着重分析精梳工艺、并粗细工艺和络筒工艺参数对成纱棉结的影响,探讨减少成纱棉结的技术措施。
1纺纱试验及分析
1.1原棉性能对成纱棉结的影响
棉纤维成熟度适中,单纤维强力高,天然卷曲适中,纤维弹性、刚性和抱合性好,在清梳加工中不易受到揉搓和纠缠而形成棉结。纤维细度适中,纤维中短绒含量少,纺纱过程中受摩擦不易纠缠,不易粘附在机件上被带入须条后经搓揉而形成棉结。轧工方法对成纱棉结的影响十分明显,锯齿轧花产生的棉结较多,皮辊轧花产生的棉结较少。配棉时要以成熟度适中为主,短绒率差异不超过3.2%,各唛头细度不超过8%,并减少原棉中软籽表皮,尽量少用锯齿棉,严格控制回用的回花比例,合理选择配棉方案对减少棉结十分有利。
1.2清棉工艺对成纱棉结的影响
原棉在清棉工序加工过程中要受到各打手的撕扯、打击和梳理,纤维受到损伤产生短绒,经过搓揉形成棉结。因此,各打手速度要适当偏低掌握,适当缩短打手伸出肋条的长度,一般选择2 mm~4 mm。自动抓棉小车下降速度适当降低,有利于充分开松和除杂。缩小A034型六滚筒开棉机剥棉刀和打手的隔距,减少返花和棉束的反复打击揉搓,保证清棉设备气流畅通、隔距合理、通道光洁,减少棉结的产生。
1.3梳棉工艺对成纱棉结的影响
适当降低刺辊、锡林和道夫速度,提高盖板速度,明显减少短绒率和棉结数量。生条定量偏轻掌握,锡林盖板间隔距偏小控制,有利于加强对纤维的分梳和除杂,减少生条棉结。采用瑞士格拉夫针布,针布锐度高,可加强对纤维的分梳,提高纤维伸直平行度和棉网清晰度,能有效减少生条棉结。锡林道夫间隔距适当偏小,轧辊与道夫间张力牵伸适当降低,可使纤维顺利转移和提高梳理度,明显减少生条棉结数量。
1.4精梳工艺对成纱棉结的影响
1.4.1精梳落棉率
精梳工序排除了大量的短纤维和杂质,纤维伸直度、平行度得到改善,和同号数的普梳纱相比,棉结数量减少。纺T/CJ 67/33 13 tex、CJ11.5tex纱时,我们选择了,六种不同的落棉率,成纱棉结测试结果见表1。
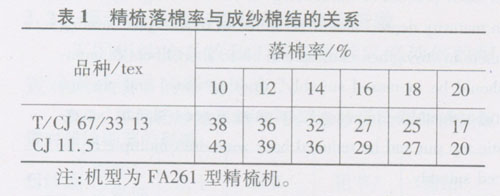
由表1可见,精梳落棉率与成纱棉结数量呈负相关,落棉率提高,排除的短绒含量增加.成纱棉结数量明显下降。
1.4.2精梳机毛刷速度
毛刷圆整度和毛刷速度是精梳纱棉结产生的关键因素。纺CJ14.5 tex纱时,精梳落棉率为18%,精梳机毛刷直径为100 mm,选择800 r/min、1000 r/min和1200 r/min三种毛刷速度,纺成纱后经测试棉结分别为34个/km、26个/km、19个/km。可见,提高毛刷速度能有效清洁锡林表面,排除较多的短绒和杂质,减少成纱棉结。
1.4.3精梳其他工艺
使用瑞士立达E7/6型精梳机,经过工艺试验发现给棉方式、喂棉长度、喂给棉层厚度、顶梳尺度、落棉刻度及搭头刻度等对改善分梳质量、提高棉网均匀度及减少成纱棉结十分重要。纺CJ7.3 tex时,选择18%的落棉率,小卷定量68g/m,给棉长度5.2 mm,顶梳尺度52 mm,纺成纱后,千米棉结由原来的32个/km降为20个/km。
1.5并条工艺对成纱棉结的影响
1.5.1并条速度
成纱棉结随着并条速度的提高而增加,加工C 14.5 tex时,在FA302型并条机上选择两种速度,纺纱后的测试数据表明,适当降低并条速度有利于降低成纱棉结数量,试验结果见表2。
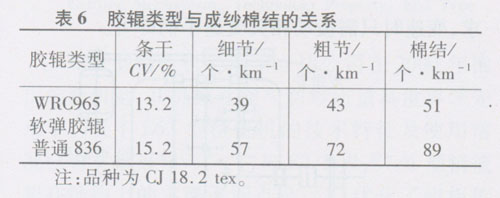
1.5.2并条道数
在配棉、清梳与精梳工艺相同的条件下,并条道数与成纱棉结的关系见表3。
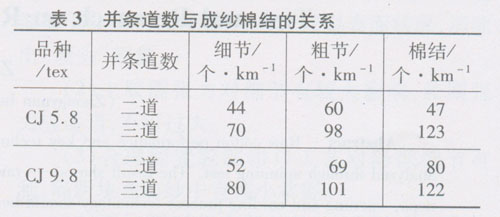
由表3可见,采用二道并条纺细号纱有利于减少成纱棉结和粗细节。因为三道并条造成纤维疲劳后易粘连,经揉搓后形成棉结,并且三道并条使总牵伸倍数增大,导致熟条太熟太烂,增加附加不匀率,从而产生较多的棉结。
1.6粗纱、细纱主要工艺对棉结的影响
1.6.1粗纱回潮率
纺T/C 65/35 13 tex时,分别将粗纱放置在三种相对湿度下48 h,纺纱后分别测试成纱棉结,结果见表4。
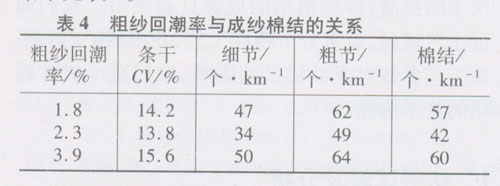
由试验结果可知,粗纱在一定相对湿度下经适当放置可提高粗纱回潮率,对稳定纱线捻回有一定作用,同时粗纱中纤维刚度适当降低,静电积聚下降,减小了纤维在纺纱过程中相互排斥,有利于减少千米棉结和粗细节。但当回潮率过大时,则纤维容易纠缠和粘连,反而导致棉结增加。
1.6.2粗纱定量和捻系数
在T/C 65/35 13 tex品种上进行了粗纱定量和捻系数对成纱棉结的影响试验,结果见表5。
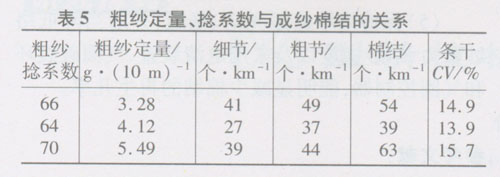
由表5可见,采用适当的捻系数和偏轻的定量,有利于减少棉结。适当大的捻系数可提高细纱牵伸前区须条的紧密度,减少边缘纤维和短绒的散失,有利于增加纤维间的应力和抗弯刚度,减少纤维搓转而形成棉结。适当减轻粗纱定量可减小细纱机总牵伸倍数,有助于减小纤维在牵伸区的移距偏差,能改善条干和纱条光洁度,减少成纱棉结和粗细节。
1.6.3细纱软弹不处理胶辊对棉结的影响
前胶辊采用无锡二橡胶厂生产的不处理胶辊,由于胶辊弹性高,对浮游区纤维运动控制作用加强,延长摩擦力界,缩小加捻三角区,可减小千米棉结产生的概率。不同胶辊纺纱对比试验结果见表6。
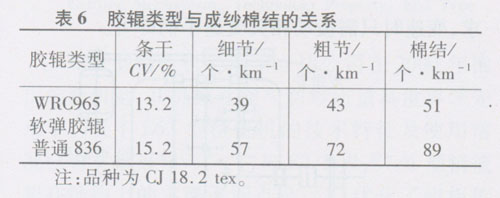
由表6可见,采用WRC965型软弹不处理胶辊可加强对浮游区纤维的控制,防止短纤维扩散而形成棉结。
1.6.4上销形式对棉结的影响
纺CJ 14.5 tex色纱时,我们选择了铁板上销和上销进行纺纱对比。铁板上销纺纱成纱条干CV为15.8%,细节59个/km,粗节242个/km,棉结208个/km,上销纺纱成纱条干CV为14.6%,细节30个/km,粗节184个/km,棉结98个/km。试验结果表明,采用上销能减少成纱棉结。这是因为上销具有高强度、高耐磨性能,抗静电较好,能自动张紧上胶圈,有利于减少胶圈内层和上销表面的滑溜率,对纤维握持增强,控制纤维有效运动,从而改善成纱质量。
1.6.5钳口隔距和集合器
在钳口隔距为2.5 mm条件下纺CJ 14.5 tex纱,有集合器时成纱棉结为41个/km,无集合器时成纱棉结68个/km,纺C 18.2 tex纱有无集合器时的成纱棉结分别为52个/km,73个/km。采用合适的集合器和偏小的钳口隔距,能聚拢短纤维,收缩须条宽度,增加须条的紧密度,使纤维在牵伸区受到控制,防止短纤维的过分扩散和揉搓,使须条在较紧密的状态下加捻,从而减少棉结。
1.6.6细纱后区牵伸工艺
试验证明,适当提高粗纱捻度、减小细纱机后区牵伸倍数、放大细纱后区隔距,三者适当搭配既能加强对牵伸区纤维的约束,提高须条紧密度,又能使须条经后区牵伸后仍留有一定捻回进入主牵伸区,有利于提高前区须条的紧密度,进一步减少纤维扩散,从而减少成纱棉结。
2络筒工序对棉结的影响
2.1 络纱速度
C 18.2 tex纱在Autoconer 338型络筒机不同络纱速度下的质量指标见表7。

从表7可见,随着络纱速度的提高,条干CV值恶化,粗细节和棉结均有所增加,所以适当降低络纱速度,对改善条干和减少千米结节十分有利。
2.2络纱张力
在村田№7-Ⅲ型络筒机上,不同张力刻度值下筒纱质量指标见表8。
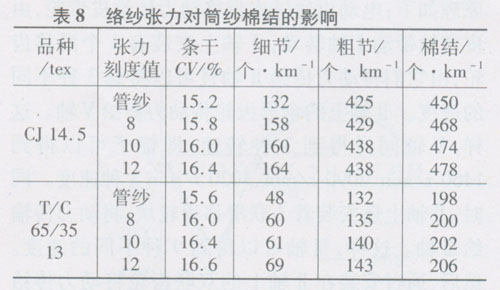
由表8可见,随着络纱张力增加,筒纱条干恶化,棉结数量增加,这是因为张力增大时,纱线与络纱部件碰撞摩擦,使卷入纱体的一部分纤维露出纱体,或将原有的短毛羽搓揉成棉结,或使较小短绒积聚增加,使截面变大,从而使粗细节和棉结增加。
3 结语
(1)棉结产生的主要原因有原棉成熟度差,清梳工艺不合理,纤维梳理效果差,梳理棉网中含有大量未能分梳开的棉结等。
(2)清梳工序未能合理除去杂质,造成梳棉生条中存在大量的有害杂质,使细纱产生棉结。
(3)合理调整牵伸分配工艺参数,提高纤维分离度和平行伸直度,减少棉结的产生。
(4)提高纺纱设备状态水平,保证工艺上车,钢领钢丝圈不磨损,纱线通道光洁,以减少棉结。
(5)保持络纱通道光洁、畅通,并适当降低络纱张力、络纱速度以及采用电清装置、气圈破裂环和气圈控制器,能明显减少棉结的再生几率。