1、原料配置
依据手感目测、原棉检测指标、单唛试纺、不同配棉方案进行优选纤维强力高、结杂少、纤维成熟度好、可纺性能好的原料。
2、工艺流程
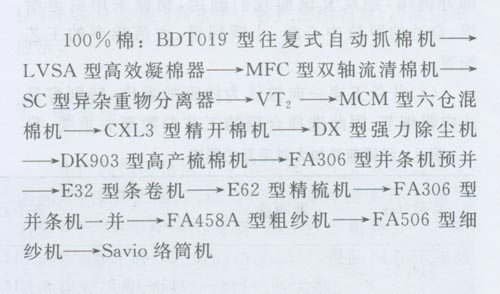
3工艺配置及技术措施
3.1 清梳联
清梳联工序的关键是寻找短绒和棉结的平衡点,而刺辊速度、锡林速度、锡林刺辊线速比是我们研究的关键点,刺辊速度降低对短绒增长有利,锡林刺辊线速比的提高对棉结有利。这是由于锡林刺辊线速比低时,纤维从刺辊向锡林转移困难,纤维随刺辊回转,一方面轧煞锡林,另一方面也易导致纤维在刺辊表面搓转成棉结,而且低速率也易造成纤维在锡林后罩板气流高压区形成塞且进入该区棉层较厚,也易导致纤维进入盖板工作区时有打滚现象而增加棉结。因此我们通过试验,最终我们确定刺辊速度为1800 r/min、锡林刺辊线速比为2.14:1,如表1。
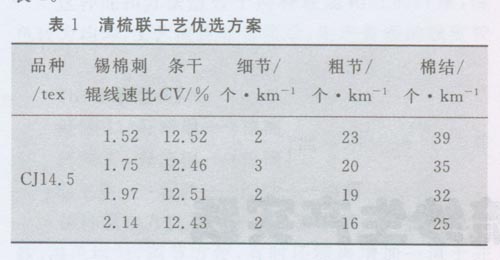
另外,为加强纤维分梳,锡林、盖板隔距适当紧些,道夫速度适当低些,选择较小的锡林道夫的转移系数,从而达减少棉结的目的。
3.2精并粗
(1)精梳工序是提高成纱质量最关键的一道工序,在此纤维得到充分的梳理,去除大部分短纤维和部分棉结,经反复试验我们确定,精梳采用后退给棉、合适的罗拉中心距、小喂棉量、大落棉率的工艺配置。
(2)并条工序一向被认为纱疵的温床,特别容易造成粗细节,因此选择合理的工艺参数至关重要,我们通过大量的正交试验确定合适的罗拉隔距、合理的牵伸分配。
(3)粗纱工序半制品质量的好坏直接影响细纱最终质量,要特别注意对粗纱伸长率和条干的控制,这不仅要有合理的工艺,而且设备的状况,关键纺纱器件的选用都要求很高。在工艺上,我们采用小后区牵伸,较大后区隔距,在后区减小牵伸力,以减少纱疵的产生,在前区使纤维尽可能前移,减小前区的移距偏差,使纤维集中变速,有利于改善条干。另外还必须选择一个合适的粗纱捻系数,既防止粗纱产生意外牵伸,又不加大细纱后区的牵伸力。
3.3 细纱
(1)采用新型钢领、钢丝圈。
钢领、钢丝圈在使用过程中存在磨合期、稳定期与衰退期。钢领、钢丝圈使用寿命加长,则稳定期相应加长,对减少和稳定成纱毛羽十分有利。此次开纺高档色织用纱我们选用了进口钢丝圈,取得了良好的效果如表2。
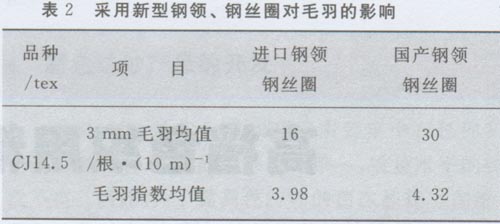
(2)采用细纱变频调速技术。
锭子恒速转动时,一落纱过程中小纱张力大,大纱次之,中纱最小,断头规律、毛羽变化规律也是这样,因此采用变频调速技术,使大、小纱阶段锭速适当降低,中纱适当提高,不仅可以平衡一落纱中张力和断头分布,也有利于不同纱段毛羽差异。
(3)胶辊前冲加大、采用集合器均对减少成纱毛羽有显著效果,见表3、表4。


3.4气捻
络筒工序采用较小的络纱张力、低速度,并保持络纱通道畅通和良好状态,能够降低筒纱毛羽的增长。
4 设备保证
(1)建立设备管理制度,加强设备检查,保证设备状态良好。
(2)各工段针对精梳纱的高标准展开特色工作。
(3)加强保全保养管理。
(4)落实保障体系,切实为运转服务。
5 操作管理
(1)规范清洁方法。
(2)规范运输方法。
(3)正确使用细纱吹吸,防止吹吸产生副作用。
(4)稳定车间气流,防止飞花附着引起断头和纱疵的产生。
6 温湿控制
温湿控制将越来被纺织企业的车间生产所重视,也将温湿控制列入质量控制必不可少的组成部分,我们也不例外。各道工序对温湿度的要求又不尽相同,现就各道生产实践对温湿度的要求谈谈我们的体会。
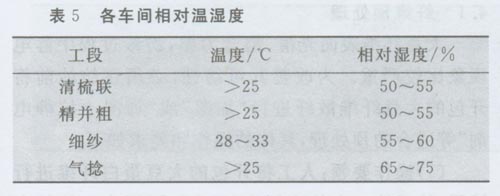
清梳联工序要求相对湿度低一些,如相对湿度偏高,生条结杂大幅增加。精并粗工序,如湿度过低会产生胶辊吸花,产生粗细节;湿度过高造成罗拉、胶辊裹花,产生大量纱疵。细纱车间,温湿度影响纤维的刚性、导电性,因而对成纱毛羽有影响。相对湿度大一些,纤维较柔软,易于被捻入纱体中。相对湿度太低,易产生静电,使毛羽增加。络筒车间因纱线与机件摩擦产生的静电导致纱线毛羽大幅增加,采用较大的湿度以减少静电,从而减少毛羽的增加。经实践证明各间相对温湿度控制如表5所示。
7 成纱质量
CJ14.5筒纱质量指标如表6所示。
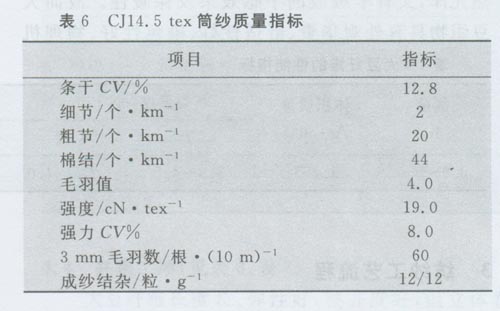
从检测数据来看,CJ14.5 tex成纱条干水平达Uster 2001公报5%水平。客户使用满意,产品供不应求。
8 结束语
生产高档的精梳用纱是体现一个企业综合水平的标尺,它要求工艺、设备、操作管理诸多环节通力合作,任何一个环节的薄弱,都生产不出符合客户要求的纱,另外选择合适的纺纱器材、提高现有纺纱器材的保养质量,也是纺纱成功的关键。