随着市场对纺织品品质要求的不断提高,引进新型自动络筒机已成为众多纺织企业的共识。我公司共引进30台自动络筒机,其中15台为日本村田公司生产的No21C型络筒机。
No21C型络筒机最高卷绕速度可达2000 m/min。配置Bal-Con跟踪式气圈控制器和栅栏式多点握持张力器张力管理系统,接头装置采用通过VOS调节的空气捻接器,清纱装置采用USTERUQC—F型电容式电子清纱器,配备电气式张力渐减装置和Perla-A型毛羽减少装置。以下对我公司应用No21C型络筒机的具体情况作一介绍。
1性能测试
1.1 Perla-A型毛羽减少装置使用效果试验
纱线经过络筒以后毛羽增长较多,其影响因素是多方面的。No21 C型络筒机使用Perla—A型毛羽减少装置的效果见表1。
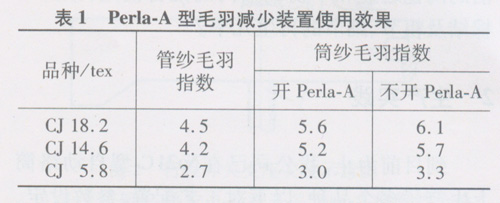
Perla-A型毛羽减少装置是一气流喷嘴,安装在原纱退绕通道张力部件上方,喷嘴喷出的压缩空气形成一个涡流小区域,能将纱线中的游离纤维重新加捻到纱线主体上,因而有效地抑制了毛羽的增长,提高了纱线的外观质量和使用性能。
1.2筒纱断裂强度测试
管纱络制成筒纱以后,由于受络纱速度、络纱张力及性能的影响,纱线强力会有一定程度的损失。No21C型络筒机能够保证在高速络纱的同时有效控制原纱强力的损失,其与№7-Ⅱ型络筒机筒纱断裂强度对比情况见表2。
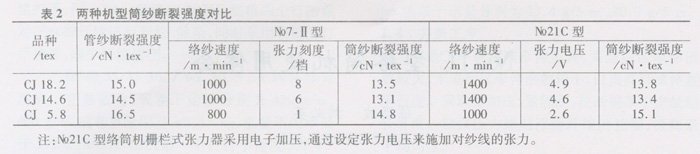
由表2可以看出,No21C型机在较高的络纱速度下,筒纱断裂强度高于№7-Ⅱ型机,这是由于No21C型机采用了垂直退绕纱道、张力管理系统、Bal-Con跟踪式气圈控制器及Pac21智能槽筒卷绕等机构,有效防止了管纱在退绕过程中的张力波动,使络简工序在获得高效率的同时,减少了管纱的强力损失。
1.3筒纱条干指标测试
管纱经络筒加工成筒纱后,不仅毛羽增加、强力损失、条干CV值升高,而且棉结、粗节、细节也有所增加,具体情况见表3。
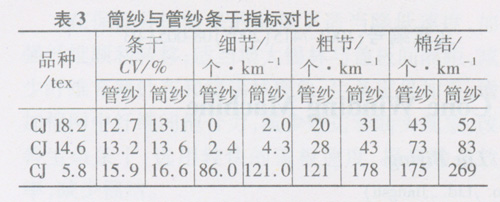
络纱过程中,受卷绕速度及络纱张力影响,管纱在退绕、卷绕过程中,纱线与络纱部件碰撞、摩擦,管纱中部分抱合不紧的短纤维游离出来,或是原本固有的毛羽经高速卷绕揉搓成棉结,从而使粗节、细节和棉结增加,条干CV值增大。
由表3可知,No21C型络筒机上配置的跟踪式气圈控制器有效控制了管纱退绕张力,加之光洁的陶瓷通道和不锈钢槽筒的配合使用,减少了棉结及粗节、细节的再生几率。
2 生产实践
到目前为止,我公司已在No21C型自动络筒上生产了多个品种,以下对工艺配置、参数设定、设备维护方法作一简要介绍。
2.1 工艺配置
从纺纱性能的测试中我们知道,在络纱过程中,随着络纱速度的提高、络纱张力的增加,筒纱较管纱条干恶化、棉结增加、毛羽增多、强力下降,因而,合理的速度与张力配置是十分重要的。表4是同一品种不同工艺配置情况下筒纱质量变化情况。由表4可知:(1)随着速度的增加,筒纱质量下降;(2)在保证筒子成形良好的前提下,选择较高的速度和较低的张力,是保证络纱质量、提高生产效率的有效途径。当卷绕速度为1400 m/min、张力电压为4.7 V时,络纱质量较好,生产效率最高。
2.2参数设定
2.2.1络纱速度
络纱速度要根据管纱的品种和质量而定,32tex以上中粗号纱及9.7 tex以下细号纱,络纱速度在800m/min-1000 m/min范围内较为适宜,中、细号纱的络纱速度在1200 m/min~1500 m/min范围内较为恰当,涤棉品种较纯棉品种速度要适当放低些。
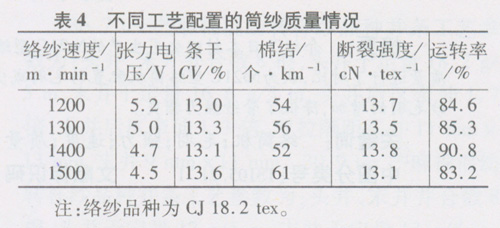
2.2.2张力控制
张力控制要根据管纱的断裂强力来选择合适的张力基准电压,络纱张力应为管纱断裂强力的8%~10%,根据络纱张力设定出相应的张力基准电压。张力初始电压设定为基准电压的150%-180%,接触卷绕电压设定为基准电压的110%-120%;张力下限电压设定在0 V~1 V,剩余纱量比率设定在20%~40%,张力渐减比例设定在20%~40%。
2.2.3捻接时间
根据管纱纱号进行微调,36 tex以上粗号纱设定为0.10 S~0.15 S,7.3 tex以下细号纱设定为0.06 S~O.07 S,中粗号纱设定为0.08 s。
2.2.4扭结阻止器开关延时
减速开始点、扭结阻止器及清洁喷气间隔可根据管纱号数适时打开。切不可不分品种一味地开或关。一般细号纱打开扭结阻止器和减速开始点并关闭清洁喷气间隔,中粗号纱必须打开清洁喷气间隔和减速开始点并关闭扭结阻止器。
3设备维护
(1)做好清扫和揩车清洁工作,车头变频器及车尾输送带的清洁极为重要。
(2)单锭内部积尘过多极易产生单锭动作失误及光电传感器功能失效,从而影响络纱质量和生产效率,应每两月进行一次单锭内部清洁工作。
(3)经常校正筒管与槽筒接触面,防止因筒管与槽筒接触不良造成成形不良,避免槽筒在高速卷绕过程中产生振动,进而导致电源板和驱动板产生故障。
(4)定期做好各部件润滑管理工作,以保证各凸轮部件动作灵活。
综上所述,No21C型络筒机自动化程度高,性能稳定,络纱质量好,生产效率高。在使用过程中,还要不断改进工艺设计,完善操作管理方法和设备维护方法,以充分发挥其效能,提高产品质量。