关键词: 染色棉纤维;配色;纺纱;成纱;质量
近年来,将棉纤维染色再纺纱,即染色棉纺纱(或称色纺纱)在我国得到了迅速的发展。棉色纺纱多用于针织物,类似于毛纺厂纺花色纱的方法而得到的不同格调的色彩。由于色纺纱是由两种或两种以上经染色后显现不同颜色的纤维混纺而成,因此,其织物改变了简单的单一纯色,艳丽美观、层次清晰,还可形成均匀分布的“ 麻点”,这些都是普通染整工艺所不能达到的。另外,色纺纱灵活性大,只要根据需求采取不同的混色比例就可以得到不同深度的颜色,克服了彩色棉颜色较为单一的缺点。因此,色纺纱具有其他产品所不能比拟的优点。
1 染色棉纤维的配色
1.1 色纤维性能的比较色纤维是棉纤维经过煮练、染色工艺后获得的。在这一过程中,纤维在外界的作用下相互扭结,并产生了一定的损伤,致使各种性能较原纤维都有所改变。几种色纤维的性能比较见表 1。
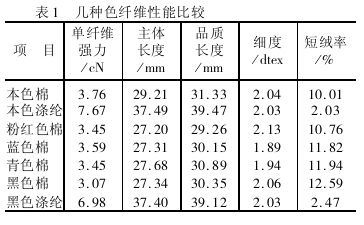
从表 1 可以看出,与本色纤维相比,色纤维强力有所下降,长度变短,短绒率随之增加。其中,黑色棉纤维强力最低,短绒率最高,强力损失为18.35% 。 而 青 色 棉、粉 红 色 棉 强 力 损 失 为8.24% ,蓝色棉强力损失为 4.52% 。黑色较本色强力亦有一定的损失。
1.2 色纤维的配色棉色纺纱是由多种色纤维进行配色而成,颜色多种多样,可根据不同的比例搭配出深浅不一的颜色。但是,由于色纤维性能的下降,色纤维混和比例越大,混和棉纤维的总体强力、长度等各项性能就越差。因此,在配色中考虑颜色的同时,还应注意不同色纤维的混用比例,混用比例最好不要超过 50% ,以保证成纱质量。下面以六种不同混色比例进行分析。六种混色比例分别是:青棉 /白棉 25/75,黑棉 /白棉 50/50,黑棉 /白棉 25/75,黑涤 /白棉 20/80,粉红棉 /白棉 20/80,蓝棉 /红棉 /白棉 10/10/80。
2 染色棉纤维纺纱工艺流程与技术措施
2.1 纺纱工艺
各种色纤维按比例配色后,在开清棉工序混和开松后进行纺纱,工艺流程如下:
开清棉→梳棉→一并→二并→三并→粗纱→细纱
2.2 工艺技术措施
(1)开清棉工序。为了减少混纺后纤维长度的变化,在开清棉时选用的打手形式为刀片打手。刀片打手对纤维的作用力较弱,可以减少打手对纤维的损伤。混棉时尽量混匀,尽量减少棉束的反滚,以免增加棉结。
(2)梳棉工序。由于色纤维在染色时产生扭结,开松时纤维容易受损伤,短绒和棉结相应增加。如果采用纺本色纱的工艺,则会产生很多棉结,几乎是本色棉的三倍之多。因此,应采取相应的措施予以控制。采用“ 紧隔距、强梳理”的工艺,针齿能深深刺入纤维束中,使纤维束能够得到很好的分梳,还能减少锡林与盖板之间的浮游纤维,避免纤维搓成棉结,可有效地减少棉结。在梳棉机隔距较小的情况下适当减少喂入定量,不至于使纤维受损伤,以减少短绒率的增加。由于色纤维强力低,刺辊速度适当调低,可减少纤维损伤,提高成纱强力。由于色纤维的长度较短,减少锡林与道夫隔距可使锡林上的纤维同道夫上的纤维充分接触而提高道夫转移率,使棉结减少。梳棉前后纤维单强比较见表 2。
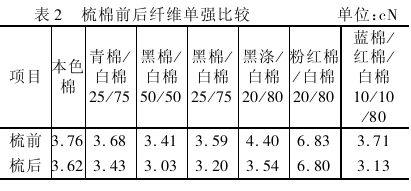
从表2 可以看出,各种纤维梳理后强力均有所下降。其中,黑涤 /白棉 20/80 强力损失最大,为 19.55% 。本色棉强力损失为 3.72% 。除粉红棉 /白棉 20/80 外,其他各混色纤维强力损失均高于本色棉很多。可见,纤维的损伤主要发生在开清棉与梳棉阶段。因此,在清梳工序应尽量提高梳理质量,避免纤维过多损伤,保证工序的成纱质量。
(3)并条工序。生条经并合和牵伸后可提高长片段的均匀度和纤维在棉条中的伸直度、分离度及平行度。并条一般采取 2 根 ! 6 根并合,最多次数不超过 4 次,以免条子过烂。由于色纤维强力低,经梳棉工序后长度有所下降,应使并条隔距较纺本色棉纤维时小一些,以防止条干恶化,改善不匀。当混比超过 50% 时,应采用纺工艺,以减少纤维缠罗拉现象。
(4)粗纱工序。牵伸隔距偏紧掌握,适当增大粗纱张力。
(5)细纱工序。应采用“ 低锭速、紧隔距”的工艺,适当增大捻度,以提高细纱强力和改善成纱条干,减少毛羽和断头。C 14.6 tex 棉色纺纱质量水平见表 3。
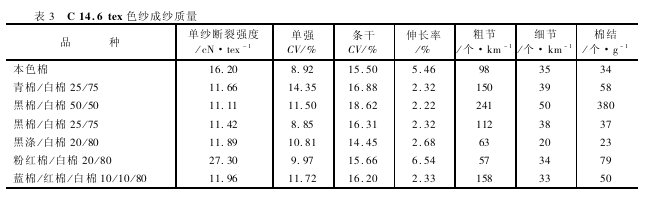
由表 3 可知,染色棉纤维较本色棉纤维的强力低,对成纱强力有较大影响,色纺纱中染色纤维比例越大,其成纱强力就越低,原因是棉纤维经染色后,纤维强力有一定损失(10% 左右),且纤维经开清和梳棉后也有损伤,纤维的主体长度有所下降,其成纱强力就有所下降。所以在原料选配时应尽量提高其品质长度,选用短绒率低、纤维单强高的棉纤维,以提高色纺纱的各项性能指标。在梳棉工序,提高梳理质量,避免纤维过多损伤,以减少短绒的增加。在细纱工序适当增加捻度,以提高成纱强力。
各品种棉色纺纱条干 CV 值均比本色棉纱的CV 值大。这是因为混色纤维的长度较本色棉的长度短,短绒率高,成纱条干不如本色棉。但各品种色纺纱的条干 CV 值相差不大。故在实际生产中,色纺纱的成纱质量可达到本色棉的成纱质量要求。
色纺纱的棉结较多,这是由于染色棉纤维经过染色后表面棉蜡已熔化,加上染料分子的渗透,纤维发涩、弹性差、易扭结在一起,纤维单强较低,所以在纺纱过程中非常容易产生棉结。混用色纤维比例越高,成纱中棉结越多。在实践中,为了尽可能减少棉结,清棉工序应采用多松少打,逐步松解来控制落棉。梳棉工序应把握适当速度,色纺时速度宜低,以减少揉搓,增强分梳,并及时清理各纺纱通道,保证纺纱的正常进行。
3 棉色纺纱纤维的混用比例
由于色纤维长度短,经梳棉工序后纤维又有一定的损伤,因此,混入色纤维半制品的主体长度较本色纯棉半制品的主体长度短,短绒率高。其中黑色棉与本色棉混和比例为 50/50 时,半制品的主体长度最短,短绒率也最高。短绒率较高的色纤维与本色棉混纺时,纤维在各工序得到半制品的主体长度较短,其强力也较低。因此进行纺纱时,要注意色纤维中短绒率的含量,防止半制品中短绒率过高而降低成纱质量。色纤维含量的多少对半制品纤维的长度有一定的影响。色纤维含量少,则半制品的主体长度长,短绒率低。当然,这也与混用纤维长度有关。另外,色纤维含量的多少主要对强力有影响,含量越多,半制品强力越低。因此,在实际生产中,要想保证成纱强力,色纤维的混用比例最好不要超过 50% 。
4 结束语
(1)棉纤维经过煮练、染色后,纤维强力有所损失,单纤维强力约为本色棉的 90% ,纤维表面发涩、弹性差、易扭结在一起。故色纤维较本色棉纤维长度短,强力低,短绒率高,成纱条干 CV 值不如本色棉。
(2)由于染色棉纤维的强力低,对纱线强力影响大,加上色纤维长度短,滑脱长度也短,故色纤维的成纱强力较低。
(3)混用色纤维的比例越高,成纱强力越低,相同比例不同品种的色纱,色纤维强力越低,成纱强力也越低。
(4)为确保混纺比和批与批之间不出现色差,混色方法以条混为佳。
(5)在试验中,发现纤维损失、棉结产生主要是在梳棉工序。在实际生产中,开松工序应采用多松少打、低速轻打、适当落棉的工艺;并、粗、细工序应采用牵伸隔距偏紧,适当增大粗纱张力的工艺;细纱工序应采用低锭速、紧隔距、较大捻度的工艺,以提高成纱条干水平。对于条干要求高的产品,可选用精梳工艺。