转杯纺纱是新型纺纱中技术较成熟、应用面较广的一种,特别是近十年来发展尤为迅速。早期的转杯纱通常是粗号棉纱,而近来转杯纱产品向中细号纱和花式纱方向发展,以期能够进入针织和装饰应用领域。
转杯纺纺制竹节纱的研究开发最早是在欧美等国家进行。期间有一些专利和论文发表,但至今也只有瑞士Amsler-Iro Zurich公司推出的纺制竹节纱的GOE装置才算是真正走向了市场,但是价格昂贵,且不能与国产机器配套。国内的研究工作始于80年代末,东华大学(原中国纺织大学)最早进行了探索,并持续了10多年,取得了一定的进展。另外,一些厂家也进行了积极的探索。从所纺制的花式纱来看,大致有竹节纱、包芯纱、多组分纱等等,其中尤以竹节纱为主。
我们的目标是研制出能够与国产转杯纺纱设备配套,纺出独具特色的转杯竹节纱的装置,并对转杯纺纺制竹节纱的机理及工艺进行研究。
1基本原理
一般来讲,竹节纱可以通过在生产过程中改变牵伸倍数或增添附加纤维来纺制。分析转杯纺纱工艺流程,可以有四种基本方案来改变牵伸倍数或添加附加纤维,从而实现纺制转杯竹节纱:①改变喂给罗拉速度;②改变引纱罗拉速度;③同时改变喂给罗拉和引纱罗拉速度;④在输送通道或分梳辊的适当位置添置附加喂入纤维机构。四种方案中:方案①是通过改变喂人量来改变牵伸倍数;方案②是改变输出速度,会出现纱线捻度变化,强力不均匀等问题,影响纱线质量;方案③是前面两者的结合,理论上应该比较好,但需要有方案①和②的实践基础;方案④需要添置附加喂人机构,比较复杂,目前也不易研究开发。因此,我们选用方案①来实现纺制转杯竹节纱,其基本原理是精确地控制喂给罗拉的动态速率增量,以产生纤维喂人量的高速可控变化,从而实现可控的转杯纱花式结构.即竹节纱。
2工艺理论研究
转杯竹节纱的最基本参数有以下四个:基纱号数、粗节倍数、竹节长度和竹节间隔,如图1所示。
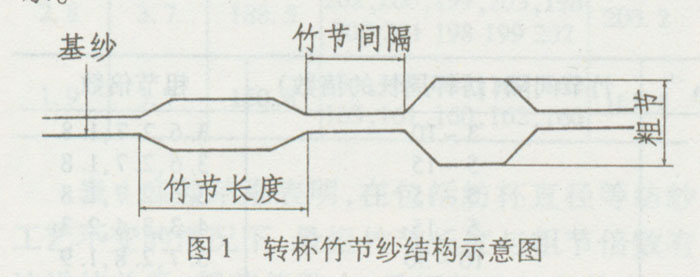
粗节倍数是指粗节相对于基纱(细节)的倍数。粗节倍数和最短竹节长度是转杯竹节纱基本参数理论研究中的两个主要方面。
2.1粗节倍数的研究
由于转杯纺纺制竹节纱仍然处于研究发展阶段,其工艺理论也很少有人研究。关于粗节倍数的估算还未见任何报导,但是根据实践经验,在同样纺纱工艺条件下,如突然增加喂给量,捻度传递长度也会缩短。当突然增加的喂给量达到一定值时,捻度传递长度将缩短到难以维持正常纺纱的状态,此时即可认为在该工艺条件下,竹节已达最大粗度。因此可以通过对捻度传递长度的研究来估算粗节倍数。
捻度传递长度(Peripheral Twist Extent,简称P.T.E)对转杯纺的纺纱稳定性至关重要。纺杯对纱条施加的捻度和假捻盘对纱条施加的假捻捻度向凝聚槽内传递,使凝聚槽剥离点后方的凝聚须条上产生了一段有捻纱段,这一纱段长度称为捻度传递长度。
在捻度传递长度的实验研究方面前人做了不少工作,但在系统的理论研究方面国内外还未见报道。这是因为捻度传递长度涉及的因素太多,假捻盘规格,纺杯规格和转速,纱线的捻系数、线密度、纤维性能、纤维与假捻盘摩擦面及与纺杯凝聚槽摩擦面的摩擦因数等等均会对捻度传递长度有影响。我们将纱线在假捻盘上的运动和受力、假捻盘与纺杯之间的自由纱段的张力以及纺杯凝聚槽内须条的运动和受力这几方面作为一个系统整体研究,得到了求解捻度传递长度的微分方程组,并得到了捻度传递长度与纺纱线密度之间的关系,在实验室纺纱基纱为36 tex以下时,纺制粗节倍数为4倍~5倍的转杯竹节纱是没有问题的。
2.2最短竹节长度研究
由于转杯纺纱的特性,转杯竹节纱的最短竹节有一个极限值。前人根据图解法曾得到这样的结论:在喂给罗拉速度不变,改变引纱罗拉的情况下,当引纱罗拉反转或停止时,转杯竹节纱的最短竹节长度是纺杯的周长。根据转杯纺并合和凝聚的机理,我们得到了转杯竹节纱最短竹节长度大于纺杯周长,且竹节长度与粗节倍数有内在的关系。
3实验及测试结果
3.1纺纱工艺参数
在实验室,转杯纺纺制竹节纱的装置与单头转杯纺纱机配套进行试纺实验。转杯纺的主要工艺参数有纺杯速度、纺杯直径、假捻盘规格、分梳辊规格及速度、喂给罗拉及引纱罗拉速度等等,竹节纱还另外有粗节倍数、竹节长度及竹节问隔等。我们对不同的纺杯速度、纺杯直径、纺纱号数进行多方案试纺。
纺纱基本参数:
纺纱号数:基纱32.4 tex
棉条定量:12 g/5 m×2
纺杯直径:66 mm
纺杯速度:28 000 r/min
分梳辊规格:OS21型锯齿辊
分梳辊转速:6900 r/min
假捻盘规格:D17 mm×2 mm
捻系数:450(选用此捻系数时,已经考虑了加捻效率的问题)
经计算喂给罗拉的转速nw=3 r/min
则丝杆转速ns=48 r/min(纺竹节纱时,提高丝杆速度)
3.2竹节纱的特征参数
竹节纱的特征参数主要有粗节倍数和最短竹节长度。
粗节的倍数实际是丝杆高低速之比,本实验机的最大粗节倍数为4倍左右。另外通过改变电机运行速度可改变粗节倍数,本实验另外设置的粗节倍数为3倍和2倍左右。
根据研究,竹节的最短长度与纺杯的周长及粗节倍数有关,其值可根据公式(1)计算:
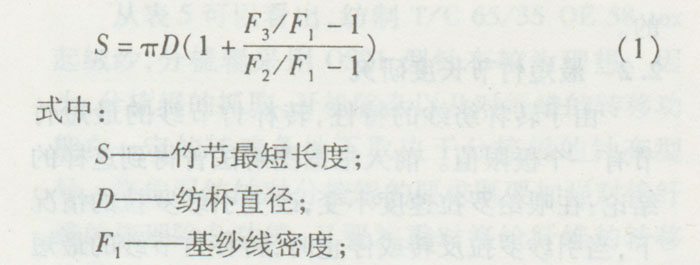

假定纺杯直径为66 mm,则当粗节倍数为3.6时,竹节长度为414.7 mm;当粗节倍数为2.7时,竹节长度为342.9 mm;当粗节倍数为1.8时,竹节长度为271.1 mm。
竹节的间隔在纺杯周长3倍~40倍的范围内取某段区间随机变化。
3.2.1试纺方案的确定
根据实验实际情况,确定了以下7个方案,具体工艺条件见表1。
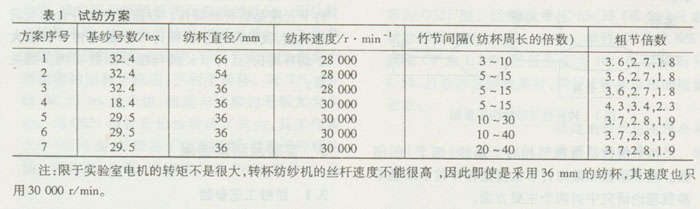
3.2.2粗节倍数
由理论分析可知,基纱线密度在36 tex以下时,粗节倍数为4倍~5倍将不影响纺纱的连续性和稳定性。以方案6为例,根据实际试纺的工艺条件,计算捻度传递长度随线密度的变化关系如图2所示。可见粗节线密度从29.5 tex增加到126 tex,其最小捻度传递长度也大于7 mm,因此能够顺利纺纱。实际试纺过程中,受实验室电机功率限制,粗节倍数最大在4倍左右。纺纱过程中,所有方案都能顺利纺纱,并且稳定性较好,这也证明了粗节倍数估算的正确性。
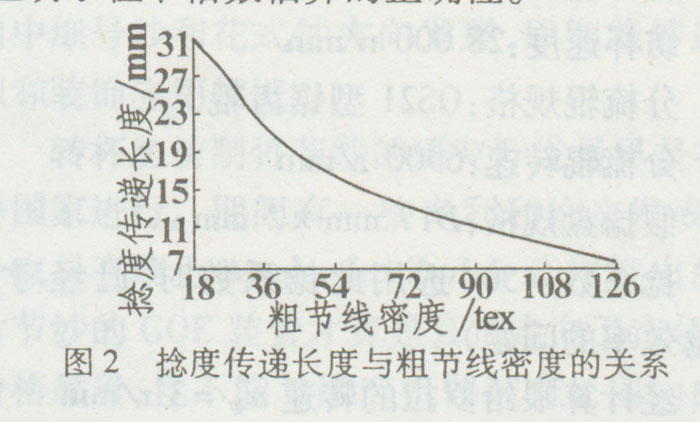
粗节线密度的测量采用间接方法,即求取5cm最粗的一段粗节测质量。对于方案1,取10组测定,结果如表2所示。
由表2可知,在喂给罗拉快速、相应输出的竹节纱长度大于纺杯周长的情况下,粗节线密度能达到设计要求,即粗节倍数可达到设计要求。
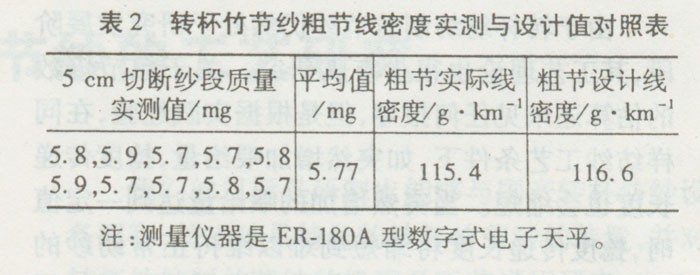
3.2.3竹节长度
竹节长度与纺杯直径有关,直径越大,其竹节长度也越长。从表1中的前三个方案中可见,其他工艺条件相同,仅是纺杯直径不同,分别为36mm、54 mm、66 mm,得到的竹节长度也不同(见表3)。
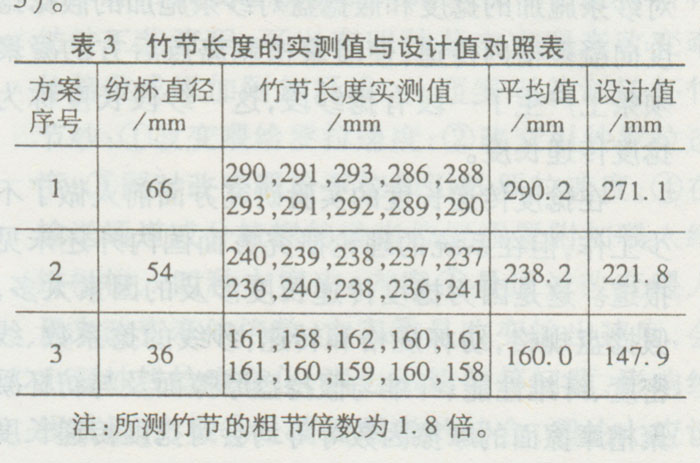
表3表明:在其他纺纱工艺条件相同的情况下,竹节长度与纺杯直径有关。其中设计值是根据理论计算得到的。比较实测值与设计值,可以发现,实测值比设计值大,主要原因是设计值是在电机速度跃变的理想情况下得到的,而实际运转中变速是有一个过程的。
由(1)式可知,竹节长度与F3/F1,、F2/F1,有关,对方案7进行研究测量,结果如表4所示。

表4实验结果表明,在包括纺杯直径等纺纱工艺不变的情况下,最短竹节长度与粗节倍数有这样的关系:粗节倍数大,最短竹节长度就大,粗节倍数小,最短竹节长度短。这与理论研究结果是吻合的。
3.2.4 竹节间隔
竹节间隔要求在设计范围内随机分布,通过对方案5、方案6、方案7所纺竹节纱的竹节间隔进行测试,表明竹节间隔能够在设计的范围内随机变化。而且当竹节间隔在大于某一值(指竹节长度)的范围内变化时,不会影响竹节长度和粗节倍数。
4转杯竹节纱与环锭竹节纱的风格
转杯竹节纱与环锭竹节纱的风格有很大不同,环锭竹节纱的竹节比较饱满,竹节短而粗;而转杯竹节纱的竹节细而长,有些类似于麻的风格_一般来说,亚洲市场环锭竹节纱比较受欢迎,而转杯竹节纱则在欧美市场较受青睐。应该说,两种竹节纱各有自己的特点,相互不能替代。
5 结语
基纱号数、竹节长度、粗节倍数和竹节间隔是竹节纱的四个基本参数,其参数的改变对竹节纱的风格有影响。其中,竹节长度受基纱号数、纺杯直径和电机性能等因素的影响,且由于转杯纺成纱的特殊机理,其最短竹节长度大于纺杯周长,并与粗节倍数有内在的联系。粗节倍数主要受基纱号数、电机性能和竹节长度所影响,同时也受纺纱工艺所限制,倍数不可能非常大,而是有一个范围。竹节间隔主要是最终反映到纱线风格上的不同。基纱号数则影响到竹节长度和粗节倍数。
采用改变喂给罗拉速度的方法来纺制竹节纱是切实可行的,通过对转杯纺纺制竹节纱的工艺理论研究,能够设计竹节纱。该套系统已经完成了实验室的研制,目前正在进行长车实验。