20世纪80年代由于电子计算机技术、传感器技术及变频调速技术等一系列先进技术与并条机的有机结合,使新一代并条机的速度提高,并且其质量保障体系更加完善。如自调匀整装置、棉条粗节监控系统、牵伸罗拉隔距自动调节系统、高效负压清洁系统等,使棉条质量更高,为下游工序的优质高产创造了有利条件。
并条机是纺纱工序中改善成纱质量,降低条干不匀率、减少纱疵,提高混和均匀度的主要工序。20世纪80年代以来,随着电子计算机技术、传感器技术及变频调速技术与纺织的有机结合,使纺织走向高科技化,并条机也不例外,经过不断改进,使现代并条机具备了在线条干自调匀整、粗节疵点自动监控、牵伸罗拉隔距自动调节系统,形成了电子计算机监控体系,此外,还改进了机器负压净化功能,以及单独传动的自动换筒体系,使并条机功能更加完善。现代并条机质量保障体系的技术进步尤为突出,现就现代并条机在线质量保障体系的有关问题讨论如下。
1 自调匀整系统
1.1并条机自调匀整形式的确立
自调匀整装置有开环、闭环及混合环等形式。开环自调匀整系统具有喂入检测点棉条的线速度比输出检测点棉条的线速度低很多的优点以及喂入部分棉层比较厚的特点,与闭环自调匀整相比有检测准确的特点,尤其是自调匀整装置控制电路完全实现数字化后,匀整频率不是以时间作为扫描基础,而是以喂入棉条经过检测罗拉的长度为基础。先进的乌斯特自调匀整扫描长度为每次1.5 mm,有的还缩短到1 mm,扫描检测一次所需时间达到毫秒级,速度快,精度高,匀整频率高,一般可将±25%范围内的喂入棉条匀整到±1%以内,因此,并条机自调匀整器的形式,目前已大都确定为开环形式,即检测点与调整系统同在喂入侧。
1.2 传感器与AC伺服电机工作原理
图1是RSB-D35型并条机的自调匀整系统,是由一对沟槽罗拉及舌簧对全部喂人棉条进行检测,检测到的信号经舌簧的变形及时转换成匀整电量信号,经微型计算机处理后,在原棉条即将进入主牵伸区时,由微型计算机指令高灵敏的伺服电机变频,修正主牵伸区的牵伸倍数,达到对输入棉条匀整的目的。传感器对棉条的检测频率很高,而且与速度变化无关,对输入棉条每1.5 mm检测一次。这种开环自调匀整系统反应时间可缩短到毫秒级,所匀整的棉条片段长度被缩短到几厘米。即使并条机输出速度达到1000 m/min,自调匀整装置也足以相适应,而且对于生条、半生熟条及精梳条接头所造成的不匀,也有很好的匀整作用。
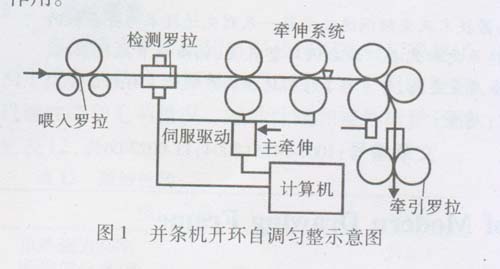
1.3 自调匀整装置的应用
由于自调匀整装置设计原理具有不同的探测棉条的频率,因此,不同的自调匀整系统,适应于不同的喂人棉条线速度。
乌斯特自调整系统可配备在速度较高的并条机上,最高适应速度可达到1000 m/min,国产BYD型自调匀整系统适应出条速度在600 m/min一800 m/min,车速在650 m/min左右的自调匀整系统可采用台湾东夏的THD-901AL型自调匀整装置。
目前国产自调匀整装置很多,但适应高速而且匀整效果还要进一步提高。据调查,在国产并条机上应用乌斯特自调匀整系统及台湾东夏自调匀整系统,车速也开的不理想,如果车速开的较高,匀整效果也达不到理想的水平。
1.4 自调匀整效果与并条机输出速度、生产品种
及原料质量的关系
高速并条机因加工的原料不同,线速度亦不同。如1000m/min的高速并条机只可加工普通原棉;加工化纤及混纺条,输出速度在650 m/min~900 min,精梳条线速度在600 m/min,低级棉、废棉多的混和棉条限开在500m/min以下,甚至RSB系列并条机,在加工低等级原料的棉条时车速也只能开到250 m/min。生条及半熟条短绒含量的高低也会影响匀整的效果。
由此可见,原料不同、产品品种不同及棉条中含短绒率不同不仅影响并条输出线速度,而且自匀整效果也达不到应有的水平,这是自调匀整系统能否发挥正常作用的关键。
以精梳18.2 tex环锭纱为例:开环乌斯特自凋匀整系统在正常条件下,匀整后熟条条干的1m、3 m及5 mCV值分别达到0.3%、0.2%及0.1%,重量偏差在±0.5%左右,可达到乌斯特2001公报5%水平。
自调匀整并条机一定要加强短绒率的管理才可使成纱条于达到较理想的水平。如果精梳条中短绒率含量在8%以上,其成纱条干CV值仅可达到25%水平,如果短绒率含量减少到2%,细纱条干CV值可达5%水平。1.5匀整效果的讨论
电子计算机控制的自调匀整系统,通过操作面板,可以设定棉条匀整界限(重量偏差和1 m、3m及5 m条干CV值),如果重量偏差、条干CV值超限,机器自动停车。
自调匀整系统一般都应用在末道并条。对喂人棉条长片段的平均重量偏差和短片段周期性重量波动,仅依靠并合作用只能解决短、中片段的不匀,而长短片段的自调匀整装置能解决长短片段周期性不匀,并条机将棉条并合及自调匀整作用相结合,可比较理想的使熟条达到较高的均匀度水平。
解决长短片段不匀,可解决对纱条重偏及纱条重量不匀的控制,而长片段自调匀整则保证长片段平均重量的稳定性,这样才能保证成纱重量不匀稳定在一定的水平。
细纱重量不匀率下降,必定会影响成纱条干均匀度变异系数的下降,从而改善成纱强力的均匀度,使平均强力提高,减少强力极差,提高细纱最低强力,减少细络及织造工序的断头,提高下游工序的效率。
新型并条机自调匀整的概念还包括保证并条机停机及启动时,能使棉条质量保持在较高的水平。不管并条机车速快慢,测试重量不匀率虽然不代表重量偏差,但两者又相互影响,重偏控制不当,会使重不匀增大,反之,当重量不匀率大时,重量偏差就难以控制;纱条重量不匀率与纱条条干均匀度有关,重量不匀率低的纱条条干均匀;重量不匀率与乌斯特条干CV值也相关,重量不匀率低,说明纱条单位长度的重量比较均匀。
2棉条粗节疵点的在线监控
及早发现处理或报警并条机上棉条粗节疵点,可以减少对下工序产品的危害性,并使长片段质量得到保证,现代并条机不仅配备了自调匀整系统,还配有对棉条粗节疵点的在线检测技术,可很好的监控棉条粗节疵点,对提高纺纱质量有十分重要的作用。
2.1棉条粗节疵点的基本概念
新型并条机的粗节监控器,设在输出部分,称为质量监控器QUALITY MONITOR。如图2所示,生条经过乌斯特条干仪检测后,粗节疵点在波谱图上的曲线形状是呈现出两个长而宽的峰值,由于受检棉条长度远大于125 m,根据波谱图上粗节疵点的距离可准确查出粗节疵点产生的原因。经过长期摸索分析,确定棉条粗节疵点最短长度可为20 mm,断面粗度偏差在+15%以上,低于+15%波谱图所反应的情况不够确切,同时低于+15%的棉条,对纺出细纱粗节的影响不显著,对下工序的产品质量的负面影响较小。
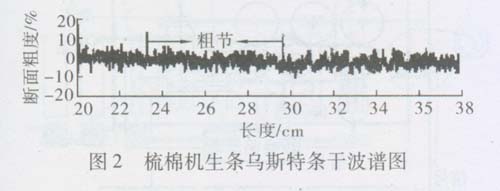
经过大量试验得出结论:当棉条粗节长度大于20 mm,棉条重量偏差大于+15%时,定为熟条棉条粗节疵点,也是熟条粗节疵点在线监控的下限。上限控制在+25%,并条机粗节监控系统会自动停车报警。
2.2粗节疵点的在线监控技术
粗节是发生在棉条或纱线上的偶发性疵点,其外观是沿棉条长度方向上横截面粗大的偏差。一般纺纱厂大都利用试验室离线乌斯特条干仪对棉条进行检验,通过检验发现纺纱过程中这种偶发性粗节疵点及产生的原因,但此时粗节已流人到细纱工序,除了切除以外已无其他方法挽救,以致会造成一定程度的浪费。
现代并条机已配置了独立于自调匀整系统以外的单独检测与消除粗节疵点的在线自动监控体系,可直接在线检测一定长度内的棉条重量偏差,这种在线监控技术是设在并条输出部分,可连续不断的对棉条粗节疵点进行质量监控。
新型高速并条机都配有粗节检测系统。HSR1000型并条机装有高精度弹簧负荷扫描系统“SLiverFocuS”,这种监控系统反应很灵敏,当棉条输出速度在1000 m/min的动态条件下可将测得的棉条粗节数据(重量偏差)应用无接触、无摩擦感应式远距离传感器,可靠的检测全部棉条长度范围内的粗节变化,而且被检测的棉条不因设置粗节监控器改变前进的导条路线。这种新式检测仪可在线检测棉条号数、号数偏差、短片段棉条不匀率(CV值),并设有长度方向的重量变化曲线——波谱图,可直接读出周期性棉条重量偏差等。监控操作简单,只要操作机上控制板即可完成监控并从检测信号中应用特定的计算方法推导出粗节疵点的偏差程度(见图3)。
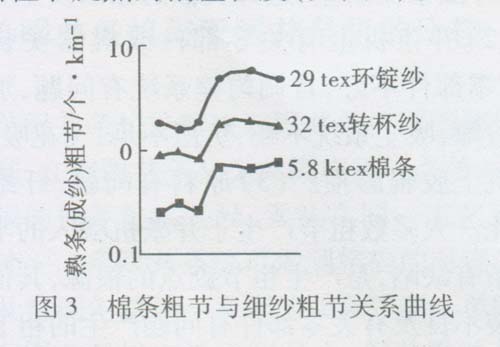
2.3熟条疵点与成纱粗节相关程度
并条机在线检测的粗节疵点与环锭细纱机、转杯纺纱机纺出的细纱长度粗节疵点相比较,根据纱疵分级仪检测结果,可看出熟条粗节与细纱长粗节相关,如图3所示为熟条粗节与细纱粗节疵点的相关曲线。
图3中的试验条件:熟条号数58 ktex,环锭细纱29 tex,转杯纱32 tex,可试验长度为10万米粗节疵点数,熟条疵点为粗节千米个数,在图3曲线中可看出环锭纱、转杯纱粗节疵点的分布基本与熟条疵点的分布状况相类似。
对并条机棉条粗节疵点的在线检测,可及早发现半制品熟条的重量偏差,并迅速反映出问题所在,以便及时解决。
在线熟条粗节疵点检测系统可直接将条干均匀度、重量偏差、粗节疵点以波谱图方式报告出,并配有报警功能,可及早纠正粗节疵点,以减少下游工序(络纱机电子清纱)的负担。
并条机上在线监控系统及早从熟条中发现粗节并予以消除是减少纱疵,提高纱线质量的超前性基础工作。当发现粗节疵点超限时,会自动指令并条机停车,一般超限停车的界限是正常棉条粗节的三倍。即正常粗节在+15%及以下,超限粗节疵点为+25%及以上,介于正常水平及停车界限之间的粗节偏差程度是正常的,对后工序成纱质量的影响并不显著。为了正确掌握并条粗节疵点并进行正确分类,将1 km长度棉条分成三级:+15%,+20%及+25%。+15%的粗节疵点与牵伸本身产生的疵点相关;+25%的粗节疵点与喂人部分的缺陷有关。与正常棉条相比较时,如果这类粗节疵点是呈显著比例增加趋势,可将产生的疵点很快鉴别出来。
产生粗节疵点的原因一般有三种:(1)喂人并条机的棉条有缺陷,即半熟条、生条质量有问题,如生条短绒多,头道并条机圈条器传动带有问题,头并圈条质量差.这种类似的原因发生频率很高。(2)并条机上有关零部件或机器安装有问题,如零部件不好,自调匀整系统有问题,加压系统有故障,吸尘系统不畅,负压不足,飞花吸不走,并条机上胶辊磨损。(3)原料有问题,纤维长度有变化。大多数粗节产生于并条机喂人的半熟条或生条有缺陷,是产生粗节疵点的根源,其他末并条安装不良及有关零部件有问题产生的粗节疵点以及原料的改变,对产生粗节的影响很少。
在并条机上应用在线粗节监测有助于提高棉条及棉纱的质量,还可以根据统计资料的分析结果进一步优化纺纱工艺及设备状态,使产生粗节疵点的相关因素得到及时纠正。
在线粗节监控系统对粗节疵点的反映很及时,并加以区分,凡超过规定极限值时,会自动指令停机,并在荧屏上显示报告,终端显示还可报告出每个条筒中粗节数量及其他质量数据;如喂人棉条不匀率,3 cm、10 cm及1 m的棉条不匀率及重量偏差等,甚至报告出每个条筒中粗+15%的粗节疵点数。
在运转管理中如果粗节疵点增加不足以使机器自动停车或报警,挡车工也应对这些疵点作出标志,以便下工序发现,并根据波谱图快速判断产生粗节疵点的原因。
2.4罗拉钳口隔距、胶辊状况对产生粗节的影响
如图4所示,每次抽查输出的500 m棉条,并以不同的钳口隔距进行对比,主牵伸区罗拉钳口距离与粗节疵点分布的关系经过反复试验发现:若钳口隔距太小,粗节疵点的发生会相应增加。一定长度的纤维都有最佳的罗拉钳口距离,从图4中可看出安全钳口隔距约在2 mm左右,最佳钳口距离为43 mm,此数可做为并条机初始安装的依据。
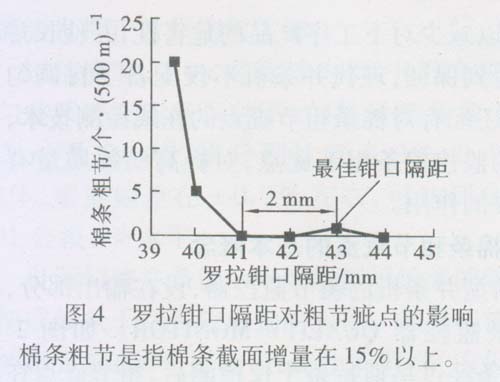
3 罗拉隔距调整系统
新型并条机下罗拉中心距(隔距)已做到集中快速调节定位,以适应纤维长度变化,进一步保障了熟条质量的提高(见图5)。

并条机在牵伸过程中会造成各种误差及不匀,一种是由故障造成的不匀,如牵伸罗拉偏心或弯曲及传动部件造成的牵伸波,这种周期性误差及不匀,经过检测及调整会很快消除。另外一种不匀是与纤维长度相关的工艺隔距不正确而造成。由于纤维沿棉条长度方向的分布不均匀,尤其在涤棉混纺条中纤维沿棉条长度方向分布不匀的现象比较多,使纤维沿棉条长度方向的分布有差异,即纤维长度与牵伸罗拉中心距不符合工艺设计要求。如瑞士RSB系列并条机,应用微型步进电机可很方便的在线自动调整中后罗拉钳口中心距,应用电子转换器、驱动器调节前区隔距,电子式转换器将改变的电子脉冲值输入步进电机,以控制步进电机的运行。从而及时改变罗拉中心距,适应纤维长度的变化。
常用的自动调节中心距的体系是闭环系统。检测点设在输出喇叭口处,经电子计算机测得的转换驱动器使步进电机改变后区中心距及前区中心距。
4“自动牵伸系统”的配置
在高速并条机上配有AUTODRAFT伺服电机,增加了并条机“预牵伸”程序,通过自我调节使预牵伸比例自我最佳优化,传动预牵伸的伺服电机还可同时传动牵伸罗拉及整台并条机,通过预牵伸带负荷的牵伸调节,优化牵伸倍数,牵伸调节范围大,可改进熟条质量,控制熟条重量偏差。只要把熟条定量设计值输入到计算机中,在计算机控制下使熟条在线定量达到设定值。不再需要人工离线监控及人工调换齿轮等,新型并条机全自动牵伸系统,使并条机重量偏差的调节实现了无级调节(见图6)。
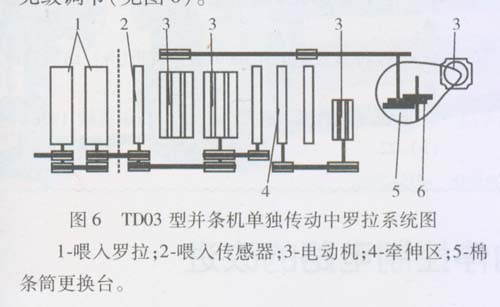
TD03型并条机为了实现“自动牵伸系统”的自动控制作用,牵伸罗拉已改为应用单独的伺服电机传动中罗拉,不仅可自动设置预牵伸,而且可以带负荷试车,从试车中获得正确的预牵伸值,调整运转中牵伸参数,形成自动牵伸倍数调节智能系统,对控制熟条重量偏差的作用十分显著。
5离线专家系统(Sliver Professional)
离线专家系统(sliver Professional)即并条机外设置的棉条专家系统具有两大功能:(1)原料和棉条重量数据输入后,能以最简便的方式提供最佳整机工艺设计方案供工厂采用。(2)对波谱图中波峰具有分析功能,在输入波谱图波长之后,Sliver Professional专家系统会提出故障原因,可迅速排除故障,进行处理,提高了机器运行的稳定性,对稳定与提高棉条质量也是一个有力保障体系。
6高效负压清洁系统
在喂人罗拉和出条检测罗拉之间,增加负压吸风点,可提高自调匀整系统对喂入棉条条干均匀度监测的精确性,消除不必要的误差。加强牵伸区负压吸尘作用,形成清洁的牵伸区域,消除积聚短绒及杂质。挡风刮板具有自动过滤清洁作用,形成恒定的吸风量。过滤网面积及沉积箱容量大,保证负压在线较长时间稳定。
7 单眼并条机与双眼并条机的比较
单眼并条机能解决双眼并条机不能解决的眼差问题,在双眼并条机上共同应用一个传动系统,对各眼的棉条重量差异,无法在同一工艺条件下达到统一。单眼并条机可做到精确的对棉条重量偏差及自调匀整等一系列的质量控制。单眼并条机比双眼并条机占地面积稍大,但单眼并条机的停开车只影响一个眼的产量。因此在同样的车速条件下生产效率比双眼高,弥补了占地面积比双眼多的不足。更重要的是单眼并条机的质量保障体系能精确的完成各项质量监控任务,使熟条质量稳定在较高水平。
8 其他方面
8.1 速度
现代并条机最高输出速度达到1000 m/min,从目前圈条器的设计技术上看,1000 m/min的输出速度已使圈条器运转速度加快,高速运转的圈条器会使进入条筒中的棉条受到较大的离心力作用,破坏了棉条的成形,对棉条质量带来负面作用。因此,可否认为并条输出速度1000 m/min在目前技术水平的基础上也达到极限,如果圈条器技术问题不能有突破性的进展,并条机的输出速度不可能再提高。
8.2条筒形式
新型并条机已采用矩形条筒,主要供应新型纺纱(转杯纺、喷气纺、涡流纺)用。目前在一些传统纺工艺系统中也有应用矩形条筒供应粗纱机。在同等锭距的纺纱机上,矩形条筒容量比圆形条桶容量增加50%,减少了换筒及接头次数,这对提高纺纱质量也是一项有效措施。
8.3牵伸系统加压
牵伸系统配备气动自动加压及自动释压体系,当出现故障停车时(如纤维绕胶辊、粗节疵点超限及其他故障引起停车等),上胶辊会自动御压,杜绝了停车后加压所造成的上胶辊变形,从而保证了熟条质量及下游工序质量的稳定与提高。
9结束语
现代并条机具有十分完善的质量保障体系,具有在线自调匀整系统、在线粗节疵点监控系统、自动调整罗拉中心距系统、全自动牵伸系统、高效负压吸尘系统,形成一体化质量监控体系,全机的运行都是在电子计算机控制下,由多台变频调速伺服电机、各式传感器以人机对话实现触摸式荧屏操作系统及大容量数据贮存记忆功能。
国产新型并条机,如马佐里(东台)纺织公司VNIMUX单眼并条机、陕西宝成纺机FA322型并条机、沈阳宏大纺机FA326A型并条机及杭州东夏纺机HSD961型并条机等,设备也很先进,具有国际20世纪90年代水平。国外高科技并条机,如瑞士RSB系列并条机、德国:HSRl000、TD-03型并条机及意大利沃克UNIMAXR型并条机等都是当代世界先进水平的新型并条机。这些并条机都在不同程度上具有完善的产品质量保障体系,是现代化纺纱工程中提高纺纱质量的重要环节。