本标准是对GB/T 6508—1986((涤纶长丝与变形丝染色均匀性试验方法》的修订。
本次修订的主要内容为:
1.增加了变形丝(纱)测试仪法(方法B)。
2.织袜染色法(方法A)修订的主要内容为:
a)染料由分散蓝H3G改为2BLN。
b)煮练和染色时的浴比由1:70改为1:20~1:100,按有关的设备说明书要求确定。
c)对织袜条件进行了补充。
d)明确判色用光源及条件按FZ/T 01047—1997《目测评定纺织品色牢度用标准光源条件》规定。
变形丝(纱)测试仪法(方法B)非等效采用美国试验与材料协会.ASTM Z 7667—1999《用动态变形丝试验仪测定变形丝的最大卷缩率、收缩率和变异性标准试验方法》。
本标准自实施之日起,同时代替GB/T 6508—1986。
本标准由国家纺织工业局提出。
本标准由上海化学纤维(集团)有限公司归口。
本标准起草单位:中国化纤工业协会化纤产品检测中心、苏州振亚丝织厂、纺织工业标准化研究所。
本标准主要起草人:陆秀琴、傅泽芝、王卫亚、李志恩。
本标准1986年首次发布。
1 范围
本标准规定了涤纶长丝染色均匀度试验的两种方法——织袜染色法(方法A)和仪器法(方法B)。仲裁时使用方法A。
本标准的方法A适用于涤纶低弹丝和牵伸丝,方法B适用于涤纶低弹丝和BCF丝。
2引用标准
下列标准所包含的条文,通过在本标准中引用而构成为本标准的条文。本标准出版时,所示版本均为有效。所有标准都会被修订,使用本标准的各方应探讨使用下列标准最新版本的可能性。
GB 250—1995评定变色用灰色样卡
GB/T 6502—2001 合成纤维长丝取样方法
GB/T3291.3—1997 纺织 纺织材料性能和试验术语第3部分:通用
FZ/T 01047—1997 目测评定纺织品色牢度用标准光源条件
3定义
除方法A和方法B中规定的定义外,其他定义按GB/T 3291.3规定。
4试验方法
4.1织袜染色法(方法A)
4.1.1 定义
4.1.1.1 卷缩丝
片段性变形不良,造成卷曲不明显,有原丝风格,织物表面发亮,手感变薄,较正常丝透明的丝或卷缩率过高,织物变厚、发毛的丝。
4.1.1.2僵丝
僵直发亮,缺乏卷曲弹性的变形丝。
4.1.1.3 紧点
假捻变形丝沿丝条轴向出现的不规则未解捻或熔融粘结的紧缩状细节。
4.1.1.4 临界色调
在一定条件下,织物具有最大吸色率时的色调。
4.1.2原理
在单喂纱系统圆形织袜机上,将涤纶长丝试样(丝筒)依次织成袜筒,并在规定的条件下染色,对照变色用灰色样卡,目测评定试样的染色均匀度等级。
4.1.3试剂
4.1.3.1染料
分散蓝2BLN(又名 分散艳蓝E-4R)
结构式:
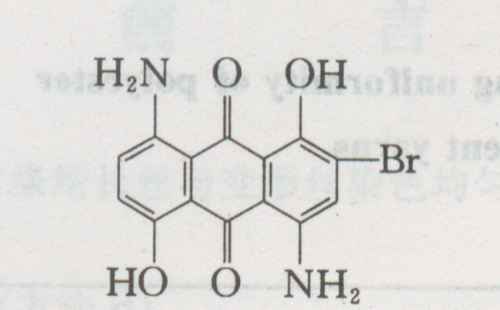
4.1.3.2 乙酸一乙酸钠缓冲溶液(pH=5)
称100 g乙酸钠溶于600 mL的蒸馏水中,加入200 mL乙酸充分搅拌,用蒸馏水稀释至1 L。
4.1.3.3中性皂粉或中性皂片
含脂肪酸80%以上,不含加白或着色物质。
4.1.3.4去离子水、蒸馏水或软水
对软水的要求是:氯化物<100×10-8总硬度<5X10-8铁<0.25×10-8总碱度<100×10-8
本试验方法中用的水均为上述三种水之一。 .
4.1.4装置
4•1•4•1单喂纱圆形袜机:直径88.9 mm(31/3),具有张力调节装置。
4•1•4•2染色机:具有控制升温速率的温度控制系统和能使试样在运动状态下染色的装置。
4•1•4.3天平:具有适当的称量范围,称量精度为士1%。
4.1.4.4洗衣机或离心脱水机。
4.1.4.5 D65标准光源,光源周围为中性灰色调。
4.1.4.6评定变色用灰色样卡(GB 250--1995)。
4•1•4•7判色用框:用直径10 mm左右的不锈钢管制成的约900 mm×90 mm,两端呈圆弧形的框。
4•1•4•8判色用板:用厚度约3 mm的乳白色半透明塑料板或黑色塑料板制成宽度分别为110 mm、100 mm、90 mm,长约900 mm,两端成圆弧形的板。视袜带松紧选择使用。要求套进袜带后平整,没有横向拉伸。
4.1.4.9超声波发生器或研钵。
4.1.4.10量筒、量杯、烧杯、温度计及特种笔等。
4.1.5取样
出厂检验时为全数检验,对每个卷装逐筒织袜染色;验收和仲裁时按GB/T 6502规定取样。
4.1.6试验程序
4.1.6.1编织袜带
a)根据名义线密度,按表1要求确定袜机针数,并选择相应针数的袜机。
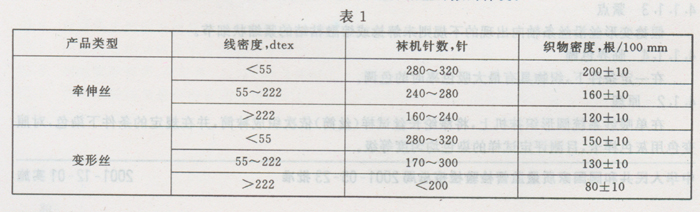
b)摇袜前必须预先调节袜机的张力螺丝,使进丝张力为0.003~O.065 cN/dtex(按名义线密度计算),筒子车距袜机约2~2.5 m,在摇袜的过程中视卷装的位置要左右旋转筒子车,使进丝张力基本保持一致。
c)依次将每个卷装在袜机上织一段约5 cm的袜带后打结换头,连续织成一条袜带后,按顺序在袜带上做出标识。
d)将织好的袜带在天平上称量(精确至1%)。
4.1.6.2煮练
a)煮练条件
中性皂粉(皂片):4%(对织物质量)。
浴比:1:20~1:100(对织物质量),按有关的煮练设备要求确定。
温度:60℃。
时间:20 min。
b)煮练程序
煮练可以直接在染色机内进行,也可以在其他能达到煮练温度并有搅拌的设备内进行。
1)根据袜带质量按4.1.6.2a)规定称取中性皂粉(皂片)(精确至1%),用60℃的少量水溶解成皂液。
2)根据煮练设备要求,确定浴比。在煮练设备内倒入水、皂液,配成煮练浴。充分搅拌后放人袜带,升温至60℃后,保温20 min;
3)排放废液,取出袜带,用70℃左右的水洗至无皂液后脱水待染。
4.1.6.3染色
a)染色条件
1)染料:分散蓝2BLN,在1%~1.5%范围(对织物质量),根据产品的吸色性能确定加入量。
2)浴比:1:20~1:100,按有关染色机的要求确定。
3)染色温度:沸染(沸点温度视不同地区的大气压不同而略有不同)或按有关染色机的要求确定。
4)缓冲剂:乙酸-乙酸钠溶液(pH一弓),每升染浴加1 mL。
5)保温时间:60 min,或按有关染色机的要求确定。
b)染色程序
1)按袜带质量称取相应的染料,用超声波溶解或用少量软水在玻璃研钵中研成糊状,(注意不能有细小染料颗粒存在)然后洗人1 000 mL内有适量近沸水的烧杯中充分溶解。
2)按4.1.6.3a)2)确定浴比,在染色机中加入相应的水,并开始升温。当温度升至60℃时,加入
4.1.6.3b)1)制备的染料溶液。搅拌均匀后,用乙酸一乙酸钠缓冲溶液调节至pH值呈酸性,放入袜带,并将袜带整理平服。用20 min左右将染浴温度升至4.1.6.3a)3)规定的温度,并保持4.1.6.3a)5)规定的保温时间。
3)排放废液,冷却后取出袜带,用水洗净脱水后在阴凉处凉干或45℃左右烘干。
注:染色程序也可以按有关染色机规定。
4.1.7染色均匀度的评定
4.1.7.1 照明条件
照明条件按FZ/T 01047—1997第5章,采用D65标准光源,照度为600~1 000 lx,光线来自样品上方。
4.1.7.2牵伸丝袜带的观测和评定
将袜带套在判色用框或黑色判色板上,织物表面与入射光成45°、观察方向大致垂直于织物表面,观测距离30~40 cm,在观测不清楚时,可将织物表面与入射光成70°,与观察人员目光成30°,逐段观测,将袜带中最深段与最浅段之间的色差与灰色样卡对比,确定该产品的染色均匀度等级。如同一段袜带内呈现深浅条纹(或斑、点),也属染色不匀,评定时应包括其深浅程度。
4.1.7.3低弹丝袜带的观测及评定
将袜带套在乳白色半透明判色板上,按4.1.7.2规定观察评定该批产品的染色均匀度等级。必要时,上举让光线透过判色板,观察人员在判色板的下方,目光与织物表面垂直,观测卷缩丝。卷缩丝按有关要求判定等级,并做好记录。
4.1.8试验报告
试验报告应包括以下内容:
a)产品名称、规格;
b)纺丝机号或出厂批号;
c)使用染料的名称及用量;
d)主要试验参数;
e)试验中的异常现象;
f)试验日期、班别及操作者。
4.2变形丝(纱)测试仪法(方法B)
4.2.1 定义
4.2.1.1 卷曲率
变形丝经热空气处理后,其潜在的卷曲重新显现所产生的收缩率。以潜在卷曲除去后的长度与热处理后的长度之差,对原始长度的百分率表示。

注:因在变形丝(纱)测试仪(TYT)上,输入辊、中间辊和输出辊的直径相同,故卷曲率、纤维残余收缩率和总回缩率
计算可以用速度变化代替长度变化。
4.2.1.2纤维残余收缩率
变形丝经热空气处理后所产生的收缩率,以原始长度与潜在卷曲除去后的长度之差,对原始长度的百分率表示。

4.2.1.3总回缩率
变形丝经热空气处理后,所产生的卷曲率和纤维残余收缩率之和,以原始长度与热处理后的长度之差,对原始长度的百分率表示。

4.2.2原理
由于变形丝的染色均匀度与纤维的取向度和结晶度有关,而变形丝的总回缩率、卷曲率和纤维残余收缩率也与纤维的取向度和结晶度有关。因此,可以通过在变形丝(纱)测试仪上,测定变形丝的总回缩率、卷曲率和纤维残余收缩率及其变异来判定变形丝的染色均匀度。
4.2.3装置
变形丝(纱)测试仪(TYT)由以下主要部件构成:
4.2.3.1 自动卷装交换器
用于大容量的生产性试验,选择件。
4.2.3.2热应力主机
热应力主机的主要部件为:
a)非接触式加热管
对于22-890 dtex的长丝(纱),温度范围为100-205℃(精度为士2℃);对于890-4200 dtex的纺织用丝或BCF丝,温度范围为130~250℃(精度为士2℃)。
b)预张力装置
对于22~890 dtex的长丝(纱),张力控制范围为4.9~24.5 cN[5-25 g](精度为±3%);对于890~4 200 dtex的纺织用丝或BCF丝,张力控制范围为9.8~245 cN [10~250 g](精度为±3%)。
c)传感器装配件
用于第1区和第1区。
1)细丝(纱)传感器:用于22~890 dtex。
2)粗丝(纱)传感器:用于890~4 200 dtex。
d)输入辊、中间辊和输出辊,三个辊直径相同。
4.2.3.3数据处理系统
包括计算机、软件和打印机等。
4.2.3.4静电消除器(选择件)
当长丝(纱)中的静电引起长丝(纱)闪光或造成试验部件上的长丝(纱)擦毛时,应采用静电消除器。
4.2.3.5张力器等。
4.2.4抽样
4.2.4.1全数检验
出厂检验为全数检验时,对该产品的所有卷装进行试验。
4.2.4.2抽样检验
出厂检验为抽样检验时,其抽样数量和抽样方法按有关产品标准规定或供需双方之间的协议进行。
确定抽样方案时,应考虑机台之间、锭位之间的离散性,以便提供一个包含生产方风险、消费方风险和可接受质量水平(AQL)等诸方面内容的抽样方案。要使所取的实验室样品能代表整个货批。
4.2.5调湿
不需要调湿和预调湿。可以在生产区域(在线)内进行试验。
4.2.G试验条件 .
4.2.G.1热应力主机速度
名义线密度22~890 dtex:100 m/min;
名义线密度>890-4 200 dtex的纺织用丝或BCF地毯丝:50 m/min。
4.2.G.2张力
a)预张力
9.8 cN(10 g)或0.088 2 cN/dtex(90 mg/dtex)。
b)第1区传感臂张力
变形丝0.001 8 cN/dtex(1.8 mg/dtex);牵伸丝0.000 9 cN/dtex(O.9 mg/dtex);某些高膨松丝,如锦纶高弹丝可采用0.003 5 cN/dtex(3.6 mg/dtex)。
c)第Ⅱ区传感臂张力
9.8 cN(10 g)或0.088 2 cN/dtex(90 mg/dtex)。
d)中间辊与第Ⅱ区输入辊之间的张力
名义线密度在890 dtex及以下者,张力为1.9~4.9 cN(2~5 g);名义线密度在890 dtex以上,张力为4.9~14.7 cN(5~15 g)。
4.2.6.3试验温度
按4.2.7.13确定。
4.2.6.4试验数量
从按4.2.4所取的每个卷装上取出试样,每个样品试验10次,每次2 m。
4.2.7装置的准备、校准和试验条件的设定
根据仪器说明书按如下步骤调整和校准试验仪,并设定试验条件。
试验条件可能因仪器版本不同而略有变化,应参照仪器说明书设定。
4.2.7.1 开动马达,检查计算机控制器的速度。
4.2.7.2检查第1传感器区域和第Ⅱ传感器区域的喂纱速度。
4.2.7.3设定加热器的温度约为100℃,给出足够的时间让它达到该温度。该温度是加热曲线的起点。
4.2.7.4按仪器说明书做零点校验,检查传感臂,并调整水平和第1、Ⅱ区的零点。
4.2.7.5按4.2.6.1设定主机速度。
4.2.7.6按4.2.6.2a)设定预张力。
4.2.7.7设定第1区传感臂的张力
按4.2.6.2b)设定第1区传感臂的张力,并选择相应的砝码,挂在第1区传感器上。调节拨盘使传感器水平,以小增量的方式进行调整,使传感臂达到平衡。
4.2.7.8按4.2.6.2c)设定第Ⅱ区传感臂的张力,并按4.2.7.7的方法校准。
4.2.7.9关闭马达,把丝(纱)穿入仪器。
4.2.7.10挂起试验仪,使软件从标准状态转为测试状态,启动马达,确保试样穿过加热管中心。
4.2.7.11 为了校正纱线通道,可用位于试验仪前方右侧的吸纱器压力表,按需要调节吸纱器的压力,如果纱线从吸纱器通过区域I不是直线流动,数据将受到影响。
4.2.7.12按4.2.6.2d)设定中间辊和第Ⅱ区输入辊之间纱线的张力,可用张力器和转动第Ⅱ区喂入器的调节器进行调节。
4.2.7.13确定试验温度
随机取1~2个卷装,按仪器说明书要求测温度曲线。测温度曲线时,从100℃开始,连续测至卷曲率曲线达到一峰值(这一点的卷曲率值最大,以后曲线开始反方向下降)后开始反方向下降时,终止试验并观察打印输出的温度曲线,以曲线上卷曲率峰值所对应的温度为试验温度。
若不出现峰值时,试验温度可设定为190℃。
4.2.8试验程序
4.2.8.1 按4.2.7规定对仪器做初步调整。
4.2.8.2当进行日常试验以及参数在此之前已设定时,按如下步骤试验。
a)穿入纱线,让测试仪运转约1 min,检查并保证纱线自由地通过测试仪和加热管的中心。
b)按4.2.7规定设定预张力。
c)把纱线标识信息输入计算机,开启试验仪。
d)如果试验多个线密度不同的卷装,则必须按线密度的变化,重新设定传感区域内的张力和预张力。
e)试验结束后,将试样从试验仪中取下。
4。2.9结果计算
全部计算;包括试验样品单个和批的平均值、标准差及变异系数,都由计算机软件完成。各性能的计算按4.2.9.1~4.2.9.4。
4.2.9.1 总回缩率
总回缩率按式(3)进行计算,精确至小数点后一位。
4.2.9.2卷曲率
卷曲率按式(1)进行计算,精确至小数点后一位。
4.2.9.3纤维残余收缩率
纤维残余收缩率按式(2)进行计算,精确至小数点后一位。
4.2.9.4标准偏差
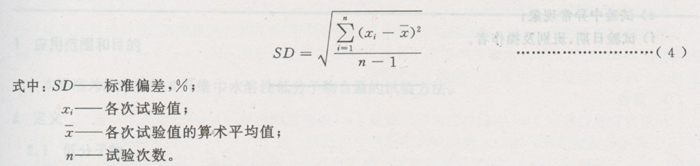
4.2.10 TYT参数的染色均匀度定等范围
4.2.10.1一等品设定范围
a)在被测样品中,随机取2车丝,按仪器说明书中的生产型自动(或手动)顺序和4.2.7规定的试验条件及4.2.8规定的试验程序,测定该2车丝各卷装的总回缩率、纤维残余收缩率的平均值和标准偏差,去掉异常数据,按4.2.9规定算出该2车丝的总回缩率平均值和纤维残余收缩率的平均值。用该2车丝的总回缩率的平均值(T±3σ)和纤维残余收缩率平均值(S±3σ)并参考他们的标准偏差(SD)值设定染色均匀度定等范围,在此区间内的卷装为一等品。算出一等品率。
b)将4.2.10.1a)中的2车丝按本标准规定织成袜带染色和判色,确定一等品率。
c)将4.2.10.1a)和4.2.10.1b)得到的一等品率及根据TYT测试数据(见4.2.9)与所对应的袜带色差程度进行比较之后,稍做调整,确定TYT参数的一等品设定范围。
d)若该2车丝TYT测得的总回缩率离散性较大或与织袜染色判色结果差异较大,则增加测试数量,并同时织袜染色,再确定TYT参数的一等品设定范围。
4.2.10.2合格品和等外品TYT参数的设定范围
根据织袜染色的判色结果和后加工(用户)要求,在一等品设定范围的基础上,适当放宽确定合格品和等外品的设定范围。
4.2.11染色均匀度试验结果的判定
按式(3)和式(2)计算的各个卷装的总回缩率和纤维残余收缩率,对照4.2.10.1和4.2.10.2规定的产品等级设定范围,确定该卷装的染色均匀度等级。
4.2.12注意事项
为使TYT测定结果正确并有可比性,操作中必须注意以下几点:
4.2.12.1 每落丝测试之前和测试结束后,分别用同一自备的较稳定的样品进行测试,以校验仪器和检查数据正确与否。
4.2.12.2在测试过程中要经常检查第1区和第Ⅱ区传感臂张力的灵敏度是否符合要求,是否在规定的范围内波动,当不符合时应及时调整。
4.2.12.3检查四个辊筒是否磨损。
4.2.12.4检查刮丝器定位是否正常。
4.2.12.5检查检结器的过丝距离调整是否恰当。
4•2•12.6检查打结器、剪刀及四个斜辊上是否有废丝并及时清除。
4.2.13试验报告
试验报告应包括以下内容:
a)产品名称、规格;
b)纺丝机号或出厂批号;
c)试验参数;
d)TYT参数的染色均匀度设定范围;
e)试验中异常现象;
f)试验日期、班别及操作者。