我公司主要以生产纯苎麻布、纯亚麻布以及苎麻类、亚麻类混纺布为主,随着纺织行业的发展,竞争越来越激烈,原来加工的一些粗号产品如亚麻/棉53/53 200/185等品种,几乎无利润可言,为了企业的生存和发展,必须向高附加值的中高档品种发展。根据市场需要我厂把开发亚麻/粘胶39/39 213/213 160混纺布作为主要攻关品种之一进行试生产,但在前期试织中,效果很不理想,主要是织机织造时经向断头太高,几乎无法生产。为此我们成立了质量攻关小组,对亚麻粘胶混纺布全面跟踪分析,采取一系列措施后,织机效率稳步提高,最后形成大批量生产,现将生产经验介绍如下。
1断头原因分析
我们结合试织情况,对织机经向断头进行了测试,逐个分析断头原因,对各种疵点所引起的断头数占断头总数的百分比进行了统计:细节35.8%,麻丝15.6%,拉头11.9%,松捻10.1%,脱结10.1%,倒断头9.2%,其他7.3%。
可以看出纺部纱疵占疵点总数的73.4%,是造成经纱断头的主要原因,而纱疵中细节和麻丝又占主导地位,主要是因为我们所用的经纱是环锭纺纱,条干不均匀,杂质含量多所造成。经与纺部联系,选择转杯纺亚麻/粘胶39 tex作为经纱,试织后,虽然条干和麻粒明显改善,织机经向断头从27.26根/台•h降为9.76根/台•h,但织造效率仍然较低,不能大批量生产。经过统计,引起断经的各类疵点所占比例分别为:倒断头38.5%,断边23.1%,绞头17.9%,麻丝10.3%,细节5.1%,其他5.1%。可以看出倒断头、断边、绞头占经向断头的79.5%,为经向断头的主要原因。
造成浆纱倒断头的原因有以下两个方面,一是上浆率过高,伸长过大,烘房温度过高,使纱线手感粗硬,失去弹性,在浆纱大张力作用下,发生脆断造成浆纱倒断头;另一方面是浆纱设备上纱线通道不光滑,如烘房花篮、防粘夹破损,浆纱伸缩筘筘齿纱痕拉断经纱,造成浆纱倒断头增多。
2 改进措施
针对上述原因,我们一方面在设备上更换破损的防粘夹和有纱痕的伸缩筘齿,检查所有的纱线通道,更换磨损件,使纱线通道光滑不挂纱;另一方面调整浆纱机拖引辊包布,调整七级齿轮箱速比,减少浆纱伸长,保持纱线弹性。
G142D型浆纱机的车速为18 m/min~20/min,蒸气压力0.25 MPa,浆槽温度85℃~90℃,pH值7~8。在工艺配方上,我们以“轻浆、低温、保弹性”为原则,调整浆料配方,反复试验。四种浆料配方及浆纱工艺如下。配方一:玉米淀粉25kg,PVA 25 kg,CMC 10 kg,乳化油3 kg,丙烯酸类浆料10 kg,硅酸钠3 kg,JFC 1 kg.浆槽粘度J1s,上浆率12%,回潮率6%。配方二:玉米淀粉25kg,PVA 12.5 kg,QL-90 12.5 kg,乳化油3 kg,JFC1 kg,浆糟粘度9 s.上浆率10%,回潮率6%。配方三:氧化淀粉30 kg,PVA 12.5 kg,QL-90 12.5kg,QL-w 3 kg,浆槽粘度7 s,上浆率8%,回潮率7%。配方四:氧化淀粉30 kg,PVA 6.25 kg,QL-90 12.5 kg,QL—W 2 kg,浆槽粘度6 s,上浆率7%,回潮率7%。四种配方的上浆及织造效果见表1。
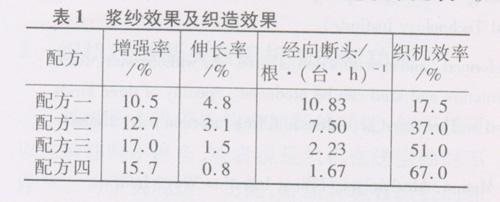
由表1可知,配方一、配方二经向断头较高,效果不理想;配方三增强效果最好,但伸长偏高,经向断头较高,织机效率低于配方四;配方四伸长率最小,纱线弹性也最好,经纱断头低,织机效率高,所以我们选择配方四作为亚麻/粘胶39/39213/213 160混纺布的上浆配方。
在操作上,加强对浆纱挡车工起机操作的检查,要求挡车工起机时经轴盘片两边对齐,目视在一条直线上,防止边纱摩擦,减少断边疵点。起机开车20 m后,不准挑经纱,不准重排筘齿,以免造成经纱绞头。加强挡车工巡回,及时处理经纱倒断头,严格控制浆槽和烘房温度,减少经纱脆断。
通过采取以上措施,织机经向断头叫显减少,由最初的13.63根/台•h,降低为1.2根/台•h,织机效率由最初的40%上升为70%。
3 结束语
通过采取一系列改进措施,解决了亚麻/粘胶混纺产品生产中经向断头等几个关键问题。到2004年8月份,我公司累计生产亚麻/粘胶混纺布150万m,织机效率达到70%以上,入库一等品率达到97%,产品得到客户的一致认可,取得了较好的经济效益。总的来说,提高亚麻/粘胶混纺产品的关键是把好原料关,严格控制细节和麻丝等纱疵,对织布厂来说,应做好浆料配方的选择与浆纱工艺控制,搞好设备维修并严格按照操作法操作,从而减少经纱断头,提高织机效率。