0 前言
在棉纺环锭纺纱系统中,粗纺工程通过牵伸,可将须条中纤维伸直度由87%以下提高到90%~93%,有利于提高条干均匀度。但经过粗纱机的牵伸卷绕,成纱质量指标如条干均匀度、重量不匀率、强力不匀率、结杂等都有恶化趋势。由于传统粗纱机结构的缺陷,开关车时牵伸、卷绕机构不同步产生的细节,大大影响成纱单强不匀率、重量不匀率及细纱断头率,形成成纱强力弱环。日本纺织界认为细纱质量及断头率80%由粗纱质量决定,因而提高粗纱机质量乃是提高粗纱质量及细纱质量的关键。
新型棉纺粗纱机采用悬锭锭翼,承载锭翼的上龙筋固定不动,使粗纱机纺纱系统与卷绕系统分离,一旦粗纱发生断头,锭翼高速回转产生的气流不再冲击粗纱,纤维不会飘逸而产生大量纱疵。悬锭锭翼为粗纱机高速、大卷装和自动化创造了条件,其机电一体化程度得以大大提高。新型棉纺粗纱机采用四罗拉或三罗拉双胶圈牵伸,配以高质量的弹簧摇架或气动摇架加压和高效可靠的上、下罗拉清洁系统,提高了牵伸系统的工作质量和可靠性。由电子计算机控制变频或伺服电机的多电机传动粗纱机,取消了传统的变速机构、成形机构及多数工艺变换齿轮,粗纱机运转速度进一步提高。多电机传动粗纱机设有张力微调控制系统(CCD装置),可检测粗纱下垂量,以保持卷绕张力稳定。多电机传动粗纱机采用3个~4个变频或伺服电机分别传动牵伸罗拉、锭翼、筒管及升降机构,锭翼工艺速度最高可达1500 r/min。由于牵伸和卷绕机构分别由单独电机传动,关车时卷绕机构先停,牵伸机构后停,使前罗拉至锭翼之间的粗纱略为松弛,再开车时张力又趋正常,可从根本上防止关车细节的发生。
新型棉纺悬锭粗纱机在我国纺织厂使用已有20多年历史,许多厂对其进行了纺纱工艺探索,取得了一定的经验,但多数厂仍沿用托锭粗纱机的传统工艺,影响了新型粗纱机正常使用和潜力发挥。笔者试图抛砖引玉,从新型粗纱机的设计,结合纺纱工艺,提出一些粗浅的意见供大家讨论。
1 粗纱张力和“恒张力纺纱”
为实现正常卷绕,粗纱机筒管的卷绕速度与前罗拉输出速度之比应略大于1,且在一落纱过程中保持稳定。卷绕速度与前罗拉输出速度之差决定了卷绕张力,在纺纱过程中,该张力尚无法感知和度量,但其大小可用前罗拉钳口至假捻器之间的粗纱段间接反映。该段粗纱张力可以目测、手感、以线阵摄像传感器(CCD)来度量;或以粗纱伸长率来间接反映,此段粗纱张力称之为纺纱张力或习惯上认为是粗纱张力。卷绕张力与纺纱张力的关系:(1)纺纱张力源于卷绕张力;(2)纺纱张力的大小与假捻点以下粗纱在锭套管绕扣包围角、粗纱压掌处的摩擦包围角、粗纱须条与锭翼间的摩擦因数及假捻器等因素有关。
纺纱过程中卷绕速度与前罗拉输出速度之比确定之后,一般认为卷绕张力就已确定,但纺纱张力则可通过粗纱在压掌上绕扣数不同;粗纱在锭杆导纱孔位置的不同(1/4圈或3/4圈);假捻器不同等方法来进行调节。因此卷绕张力与纺纱张力既互相关联又有严格的区别。
“当粗纱捻度为一定时,张力大则伸长大”_实为不全面之说,最简单的例证是:当纺纱张力很小,粗纱下垂量较大,此时粗纱强力很低,其伸长率很大,且条干恶化,相反,在假捻效果良好,粗纱张紧时其伸长率并不大。新型棉纺粗纱机大多采用四罗拉牵伸,并使用高效聚氨酯(PU)假捻器,在一定范围内采用较大的卷绕张力,不但不会使伸长率增加,相反由于卷绕张力的增加而使假捻效果增加,使最易发生意外伸长的前罗拉钳口处无捻三角区缩小,不但不会增加粗纱伸长率,而且会使伸长率减小,并取得卷绕密度增加的效果。新型棉纺粗纱机采用大卷绕张力纺纱是与托锭粗纱机纺纱工艺的最大区别。
众所周知,粗纱在一落纱纺纱过程中,由小纱到大纱,粗纱的卷绕张力须由大到小变化才能满足粗纱卷绕的工艺要求,才不至于发生冒纱。以锥轮或齿链式无级变速器(PIV)为变速机构的传统粗纱机均以经过修正的锥轮或凸轮曲线,并辅以或电气式张力微调控制系统,来达到纺纱过程中卷绕张力由大变小的目的;多电机传动(电脑)粗纱机则以植入CPU内的数学模式,并辅以张力微调控制系统(CCD)来达到纺纱过程中卷绕张力由大到小的目的。因此“恒张力纺纱”不符合粗纱卷绕工艺要求,其提法值得商榷。
“压掌叶的离心力随卷绕直径的增加而增加(因回转半径增加),压掌杆的离心力随卷绕直径的增加而减小(因回转半径减小),故压掌的压力随卷绕直径的增加而减小。这样内层粗纱不至被挤出卷装的两端。”也是片面的,甚至是错误的。因为它忽略了纺纱过程中卷绕张力变化的工艺要求,认为依靠锭翼压掌的“自动”调整作用,便可以避免冒纱的发生。为此可通过以下试验来说明:(1)增加压掌杆重量及加大压掌杆绕其支点的回转半径,即使其离心力增加而增大压掌叶对筒管的压力,希望以此增加粗纱的卷绕密度来提高容纱量,试验结果前后的容纱量没有变化,即卷绕密度没有增加。而当改变压掌由无导纱钩变为有导纱钩,并适度增加卷绕张力,在粗纱伸长率适当的前提下,粗纱的容纱量由原4200 m增加到5400 m。(2)将压掌杆重量减小到锭翼回转时压掌叶不向心,即“压力”为负数,由于卷绕张力的作用粗纱卷绕仍能正常进行。因此可以认为锭翼压掌压向筒管表面的压力(压纱力)应是以下两种力的合力。(1)卷绕张力牵拉压掌叶压向筒管的压力;(2)压掌杆的离心惯性力作用使压掌叶压向筒管表面的压力。
试验说明前者产生的压力远远大于压掌自身产生的压力。为了防止粗纱机空运转时相邻锭翼压掌互不干绕,则仍应保证在较低转速时(如400r/min)压掌叶能自动向心。
2 关于捻度和假捻度
新型棉纺粗纱机由于高速和大卷装,粗纱的捻系数必须较传统的托锭粗纱机纺纱工艺中的推荐值大。这是因为:(1)粗纱卷装增大,在细纱机上退绕时粗纱承受的张力增加,因此必须在允许范围内增加粗纱捻度以保证粗纱退绕时减少意外伸长。(2)新型粗纱机高速和大卷装使筒管表层粗纱承受的离心张力大大增加,为降低粗纱断头,保证粗纱机效率,粗纱的捻度也必须适度增加。当然粗纱捻度的设置必须与所纺纤维、粗纱定量及细纱的牵伸能力相匹配,增加粗纱捻度还会影响粗纱机的产量,但为提高成纱质量及粗纱机运行效率,大捻度仍然是新型棉纺粗纱机纺纱工艺的主要特征之一。
新型棉纺粗纱机设置了高效假捻器,利用假捻的方法来增加前罗拉钳口至假捻点之间粗纱的强力,缩小无捻三角区,防止和减少粗纱纺纱段的意外伸长,提高粗纱质量。这里引入“假捻度”的概念:粗纱机正常运转时停车,在纺纱段截取10cm粗纱,其上包含的捻度可以定义为假捻度。假捻度一般为粗纱捻度的一倍至数倍,假捻效果好则假捻度高;假捻度的大小与纤维种类、粗纱定量、纺纱张力大小、导纱角大小、锭翼转速及假捻器材质、形状、假捻直径大小等因素相关,其中纺纱张力为关键的可调因素。
棉纺粗纱机筒管前后配置,相应的锭翼亦为前后排配置。由于自前罗拉输出的须条纵向位于一条直线上,被引向锭翼入口时,若为等高锭翼便形成前排导纱角小,后排导纱角大,在捻度作用下前罗拉钳口处形成的无捻三角区后排粗纱较前排粗纱大。无捻三角区处易发生意外伸长,为了使前后排粗纱伸长差异减小,便把后排锭翼的上部抬高,形成前排低后排高,使其导纱角一致的等导纱角锭翼。采用三罗拉牵伸机构的粗纱机,等导纱角锭翼使用效果较显著,因为三罗拉牵伸机构的主牵伸区不允许采用较小的集合器,否则粗纱条干恶化,此时,输出的粗纱须条较宽(一般达8mm-10 mm),前罗拉钳口处无捻三角区长度较长,前后排差异大,造成前后排粗纱伸长差异增大。但是现代新型棉纺粗纱机大多采用四罗拉牵伸机构,在主牵伸区前增加有集束区,集束区内采用了较小的集合器,不影响粗纱条干,此时,输出的粗纱须条宽度仅5 mm左右,使用高效假捻器后使无捻三角区缩短到10 mm以内,使用等高锭翼前后排差异也不大,因此采用等导纱角锭翼的效果就不明显。表1分别为两钟规格粗纱机试验数据,均为四罗拉牵伸,但一种是等高锭翼,另一种为等导纱角锭翼,试验数据表明,两者的效果相近(不同工厂伸长率试验有差异,仅供参考)。
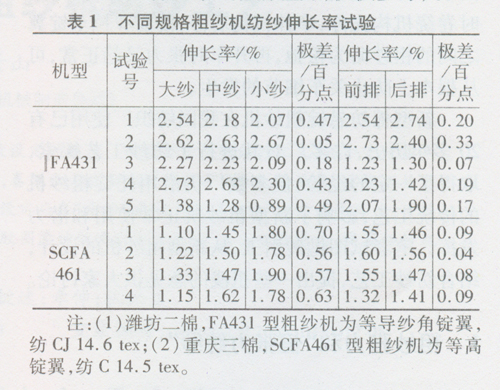
等导纱角锭翼因前后排锭翼不同而增加了锭翼备件;后排锭杆抬高使下清洁器取出困难;锭翼齿轮保养时,上龙筋盖板必须取下。曾有个别厂将等导纱角锭翼改回等高锭翼的例子。从纺纱工艺角度分析,等导纱角锭翼的后排锭翼假捻器至前罗拉钳口间粗纱长度短,弹性减少,对张力的敏感性增加,对卷绕张力的调整要求提高,当调整不当或假捻效果欠佳时,反而不利于条干的改善和伸长率差异的减小。也有纺织厂发现,等高锭翼纺某品种粗纱时,后排粗纱强力低于前排,在细纱机上退绕时易断头。改用等导纱角锭翼后,后排锭翼退绕断头有所减少。但一台粗纱机锭速不存在差异,粗纱的捻度前后排粗纱是一致的,出现上述现象有待更多纺纱实践证实和探讨。
3 锭速和“恒离心力纺纱”
高速和大卷装是新型棉纺粗纱机的主要技术特征,目前新型粗纱机的工艺转速可达1200 r/min~1500 r/min,粗纱卷装的直径达150 mm-178 mm,此时绕在筒管表面的粗纱所承受的离心张力往往超过粗纱的强力而发生卷绕部位的断头,造成纤维大量飘逸,产生严重的纱疵。因此,提高锭速以提高粗纱机产量不仅受粗纱机因素的制约,更受到粗纱强力的制约。定量5 g/10m,捻度4捻/10 cm的粗纱离心张力与锭速、卷绕直径的关系如图1所示。离心张力随锭速和卷绕直径的增加而急剧上升,当卷绕直径为150 mm时,锭速1000 r/min,粗纱承受的离心张力为3.5cN,但当锭速达到1500 r/min时,其离心张力已达8 cN,已大大超过粗纱的强力,必然会使筒管表层的粗纱发生断裂,影响正常卷绕。
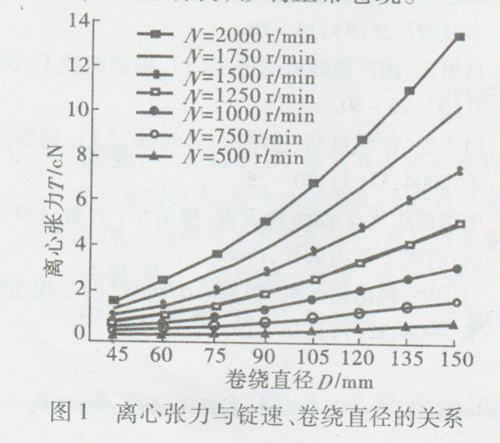
为了兼顾粗纱机的产量和效率,新型棉纺粗纱机包括使用变频调速的单电机传动粗纱机和多电机(电脑)粗纱机都设置了在中纱以后降低锭速(即降低筒管转速)的电气控制系统;中纱以前在粗纱强力可以承受的前提下,粗纱机以设定的高速运行,而中纱以后按粗纱强力大小设计锭速的降低方案,以保证尽可能减少大纱断头,确保粗纱机运转效率,这里所述的“中纱”并不是一个确定的直径或卷绕长度。因为粗纱强力随所纺粗纱的纤维品种、定量、捻度乃至温湿度等种种因素而变,各纺织厂在纺纱过程中可按实测断头率数据和经验确定。粗纱-落纱过程中“恒离心力纺纱”的提法既不科学又不切合实际。粗纱机为了达到较高的纺纱效率,应找出“中纱”的位置,限制中纱以后的锭速(筒管转速),使筒管表层粗纱的离心力小于该品种粗纱强力即可。否则,追求“恒离心力纺纱”将会大大降低粗纱机产量,或在小纱时会发生“离谱”的高锭速。
4 与牵伸有关的工艺参数
新型棉纺粗纱机大多采用三罗拉或四罗拉双胶圈牵伸。三罗拉双胶圈牵仲为双区牵伸,即主牵伸区和后牵伸区,四罗拉双胶圈牵伸则在主牵伸区之前增加了整理区,后者的主要特点:(1)主牵伸区不设置集合器,须条横向宽度大,钳口对纤维的控制作用加强;浮游区减小,纤维变速点前移且较稳定,粗纱条干质量得以提高。(2)经主牵伸区较大牵伸后须条进入整理区,使纤维急弹性变形减少,有利于提高粗纱须条纤维伸直度。(3)在整理区中设置了较小的集合器,须条输出宽度窄,无捻三角区小,在此处发生意外伸长的可能性减小,伸长率和伸长率差异均减少。(4)粗纱毛羽减少,在整理区内使用小集合器后,前罗拉输出的须条接近圆形,捻度向上传递使无捻三角区减小,导致粗纱结构改善,毛羽显著减少。(5)四罗拉双胶圈牵伸适合重定量粗纱的纺制,提高了粗纱机增产的潜力。但四罗拉双胶圈牵伸比三罗拉双胶圈牵伸增加了一根罗拉,也会带一些弊病:(1)易发生波,主牵伸区前钳口(二罗拉)为被动罗拉,一二罗拉传动托架设计制造或调整不当,易出现波。(2)主牵伸区前钳口的上、下罗拉位于一罗拉之后,当清洁器效果不佳时,二罗拉积花挡车工难以发现,会造成严重纱疵,对成纱质量威胁很大。(3)增加一列罗拉,增加了制造成本及使用成本。
与牵伸有关的工艺参数设置,如隔距、隔距块、加压、牵伸分配等各纺织厂都有很丰富的经验,不多赘述,这里提出两点意见供讨论。
4.1 粗纱定量和牵伸倍数
粗纱的定量要与熟条定量、细纱的牵伸能力等工艺条件相适应,对粗纱工序而言,其产量决定于定量及锭速两大因素,重定量能适当减小捻系数增加产量或相对降低锭速,有利于粗纱工序生产稳定和粗纱机寿命的提高。粗纱工序牵伸倍数大小的设定必须与细纱牵伸能力和成纱质量综合考虑,一般而言,粗纱加大牵伸倍数后,慢速纤维与快速纤维的比值增加,有利于纤维伸直度提高。粗纱牵伸倍数加大,能减小细纱的牵伸负担,纺特细号纱时,粗纱加大牵伸后条干恶化的损失,可以在细纱用较小牵伸获得条干改善得以补偿,综合效果会更好。
4.2 1cm波问题
采用四罗拉双胶圈牵伸的新型棉纺粗纱机,很多厂在粗纱的波谱图中发现有l cm左右的波,经细纱机牵伸之后则为25 cm~30 cm 左右的波。不同国别、不同型号、不同使用时间的粗纱机大都有l cm左右的波,其造成的原因至今未查明也未真正解决。某厂经多方案的对比试验,得出趋向性结论:牵伸力增加则此波的频次就增高;牵伸力降低则此波的频次就减少。1 cm波是牵伸波还是波,如何解决,谨提出请同行讨论。
5 结语
新型棉纺粗纱机纺纱工艺,在一定范围内以大卷绕张力纺纱为宜,为符合卷绕工艺要求,在小纱到大纱的纺纱过程中,卷绕张力的变化规律应由大到小。适当加大捻系数,重视假捻器的假捻效果是新型棉纺粗纱机的纺纱工艺的又一特征。锭速的设定应为“中纱”前等高速,“中纱”以后逐渐降速,使筒管表层粗纱所承受的离心张力小于粗纱强力。四罗拉双胶圈牵伸装置能减少粗纱毛羽,改善粗纱结构,提高粗纱机增产潜力,但存在1 cm左右的波值得探讨。
成为纺织技术精英,注册纺织人才网
找纺织人才,来纺织人才网